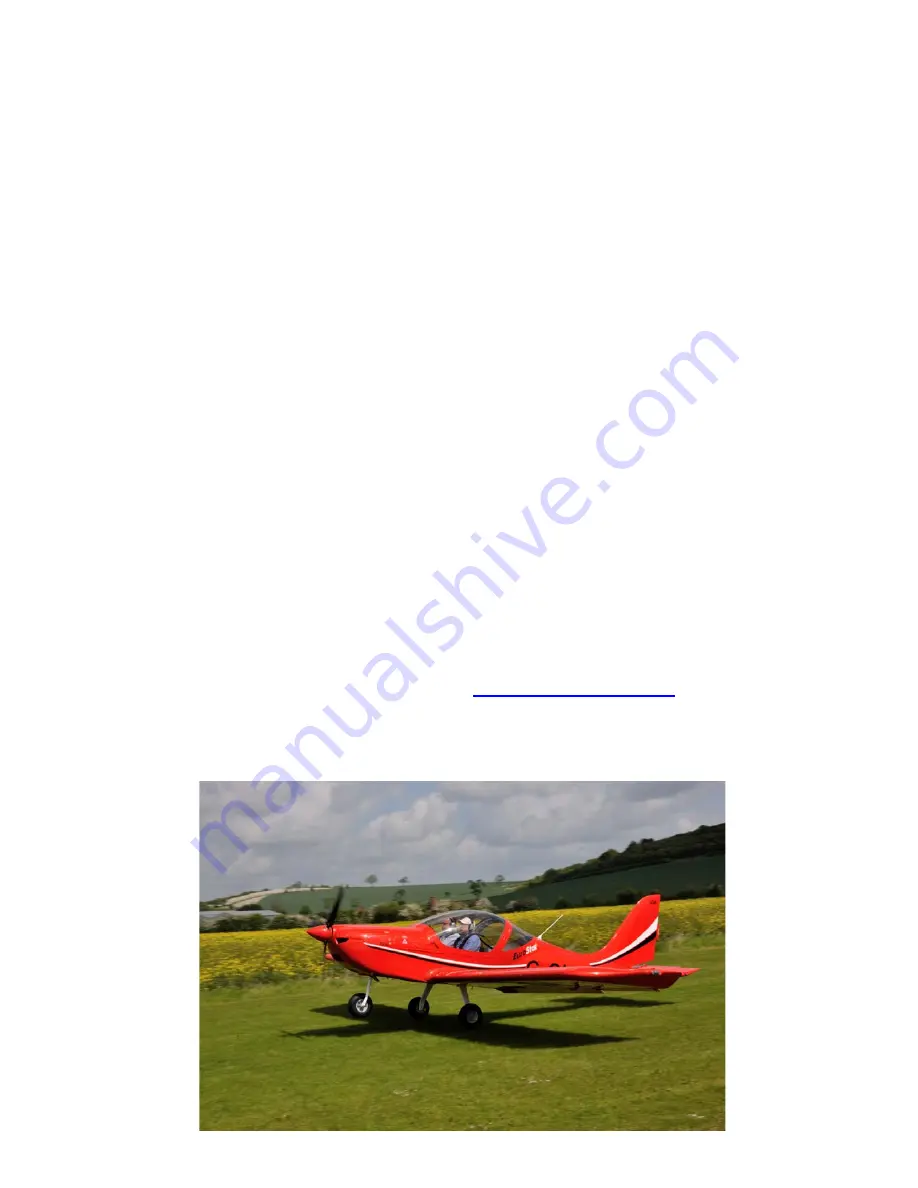
EV-97 EUROSTAR SL
MICROLIGHT
G-
MAINTENANCE MANUAL
GEN/EUR/04
Light Sport Aviation
Tel. Office: 01494 524020
Wycombe Air Park,
Email: [email protected]
Hangar 1
Web:
www.lightsportaviation.org.uk
Booker
Marlow
Buckinghamshire
SL6 3DP