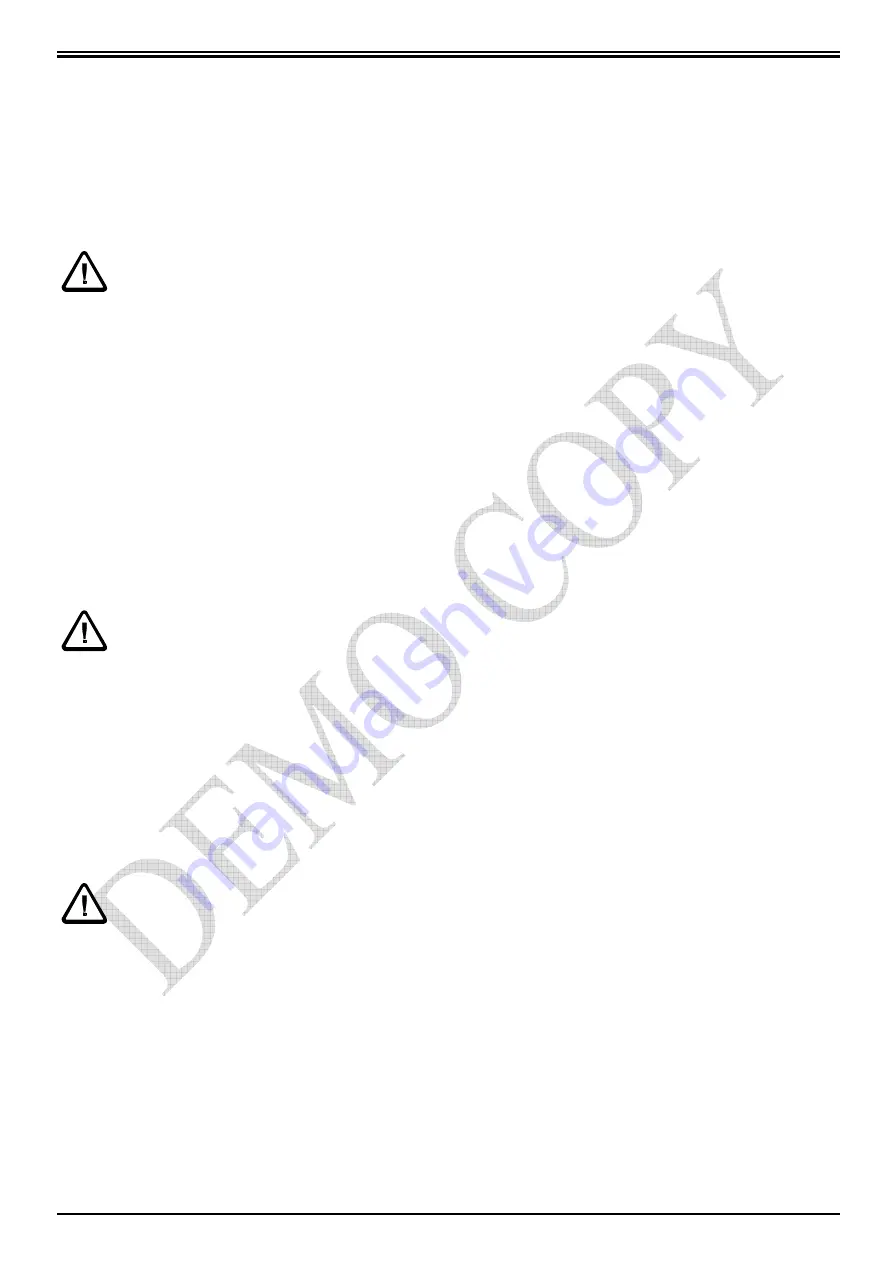
tecn@
WELDERS ITEM 8201N ÷ 8214N
EDITION: MAY 2008 PAGE 21 OF 32
7 MAINTENANCE
7.1 ORDINARY MAINTENANCE
This chapter states the necessary maintenance operations to be carried out for:
1) keeping the welding unit safe operating and preserving its efficiency;
2) avoiding the most common causes of wrong working worsening the welding quality.
GENERAL WARNINGS
Always disconnect both electrical and pneumatic supply before carrying out the
following maintenance operations.
•
Keep always the screws of both arms, electrode holder, plates and rigid/flexible connections
well tightened.
•
Remove oxidation from secondary circuit with fine sandpaper.
•
Periodically lubricate (at least every 6 months) with some drops of oil the cylinder stem after
having removed the grub screw on the piston base.
•
Lubricate with grease the anti-rotation device; if necessary, adjustment can be made by
means of both screws and nuts placed on the sides of the piston.
•
Keep welder clean from dirt and metal scraps attracted by magnetic field generated by the
welder during operation.
•
Neither washing the welding unit with jets of water which could enter it, nor use strong
solvents, thinner, nor benzine that could damage either painting or the machine plastic
components.
ELECTRODES MAINTENANCE
Electrodes maintenance must be carried out with the welder switched off.
•
When operating, the electrodes must be kept clean and their diameter must be kept suitable
for the work to be carried out. Too worn electrodes must be replaced.
•
When replacing electrodes, check that the tube bringing water to the electrode inside stops at
a few mm from the bottom of the electrode hole.
•
Do not use sealing products to remove water leakage on the electrode taper. To facilitate the
electrode removal and to prevent from both taper seizure and leakage, use high conductivity
grease similar to the standard one.
PNEUMATIC CIRCUIT MAINTENANCE
Pneumatic circuit maintenance must be carried out only by specialised personnel
trained to accomplish it under safety conditions. When possible, maintenance
must be carried out with the welder switched off and disconnected from the
pneumatic supply, with the circuit free from left air. Pay attention to the welding
cylinder descent following this operation.
•
In case of air leakage, immediately stop operating and remove it.
•
Periodically drain the moisture from the filter group.
•
Periodically discharge also the moisture eventually present in the built-in small air tank by
means of the tap placed at the bottom of the tank itself.
•
Check pressure gauges calibration.
•
Check the status of both compressed air and corresponding connections.