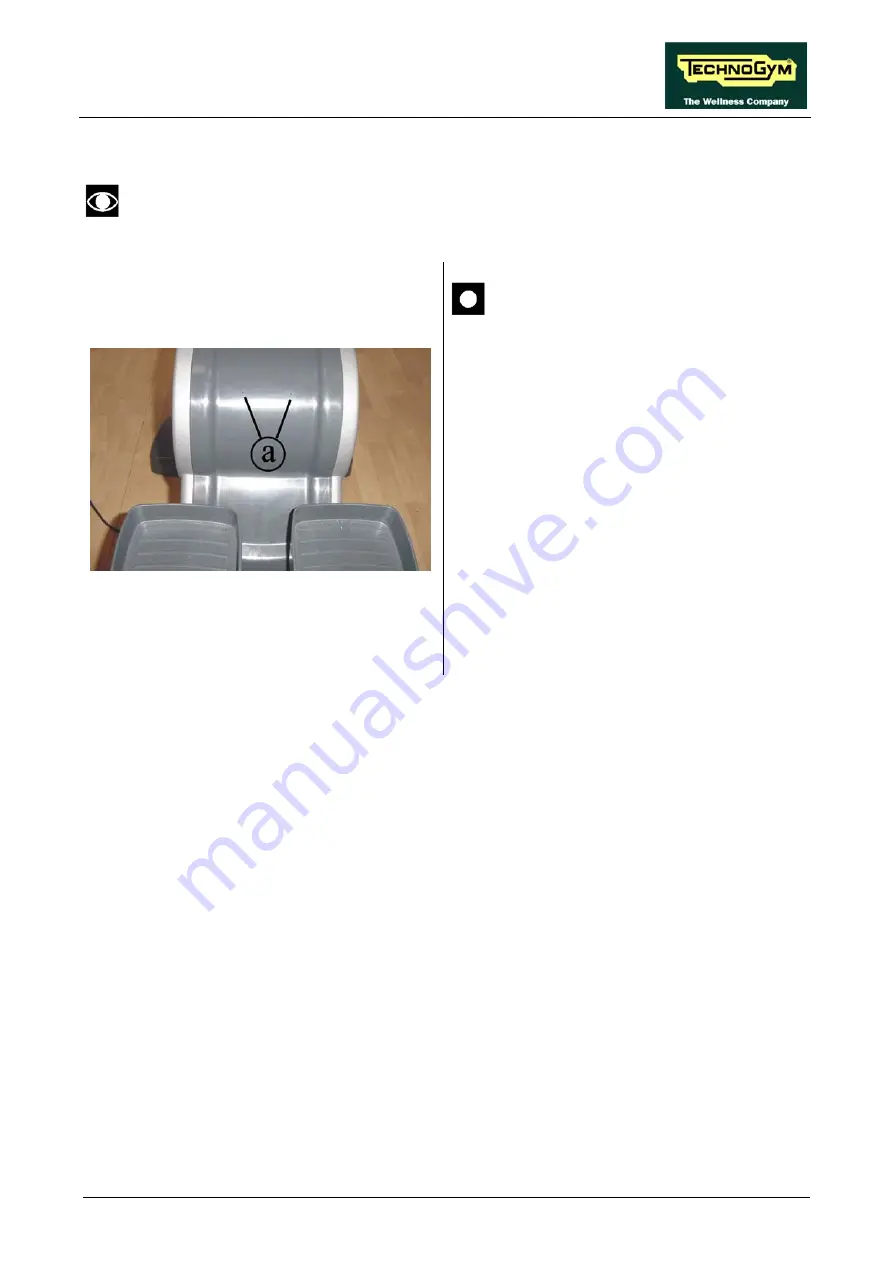
STEP EXCITE: Service & maintenance manual - rev. 1.4
Page 10.5
10.4.
LUBRICATION OF THE PEDALS CHAINS
This operation should be carried out whenever the following message appears on the
display “LUBRICATES THE CHAINS, THEN PRESSES A KEY TO CONTINUE”.
Figure 10.4-1
WARNING: to carry out this
operation, use only the lubricating oil
supplied with the machine.
1.
Insert the sprayer tube all the way into one
of the two holes
a
and spray the oil.
2.
Using one foot, slowly push down the pedal
corresponding to the hole and continue
spraying.
3.
Remove the sprayer tube and slowly allow
the pedal to come up.
Repeat the operations on both pedals of the
machine.
After carrying out the above-described
operations, change the value of the parameter
described in paragraph 9.1.16. “Lubricated”.
Summary of Contents for Step 500i
Page 1: ...SERVICE MAINTENANCE MANUAL REV 1 4...
Page 2: ......
Page 4: ......
Page 10: ...STEP EXCITE Service maintenance manual rev 1 4 Pagina vi Page intentionally left blank...
Page 44: ...STEP EXCITE Service maintenance manual rev 1 4 Page 3 14 Page intentionally left blank...
Page 54: ...STEP EXCITE Service maintenance manual rev 1 4 Page 4 10 Page intentionally left blank...
Page 88: ...STEP EXCITE Service maintenance manual rev 1 4 Page 6 32 Page intentionally left blank...
Page 132: ...STEP EXCITE Service maintenance manual rev 1 4 Page 7 44 Page intentionally left blank...
Page 140: ...STEP EXCITE Service maintenance manual rev 1 4 Page 8 8 Page intentionally left blank...
Page 178: ...STEP EXCITE Service maintenance manual rev 1 4 Page 10 6 Page intentionally left blank...
Page 181: ......