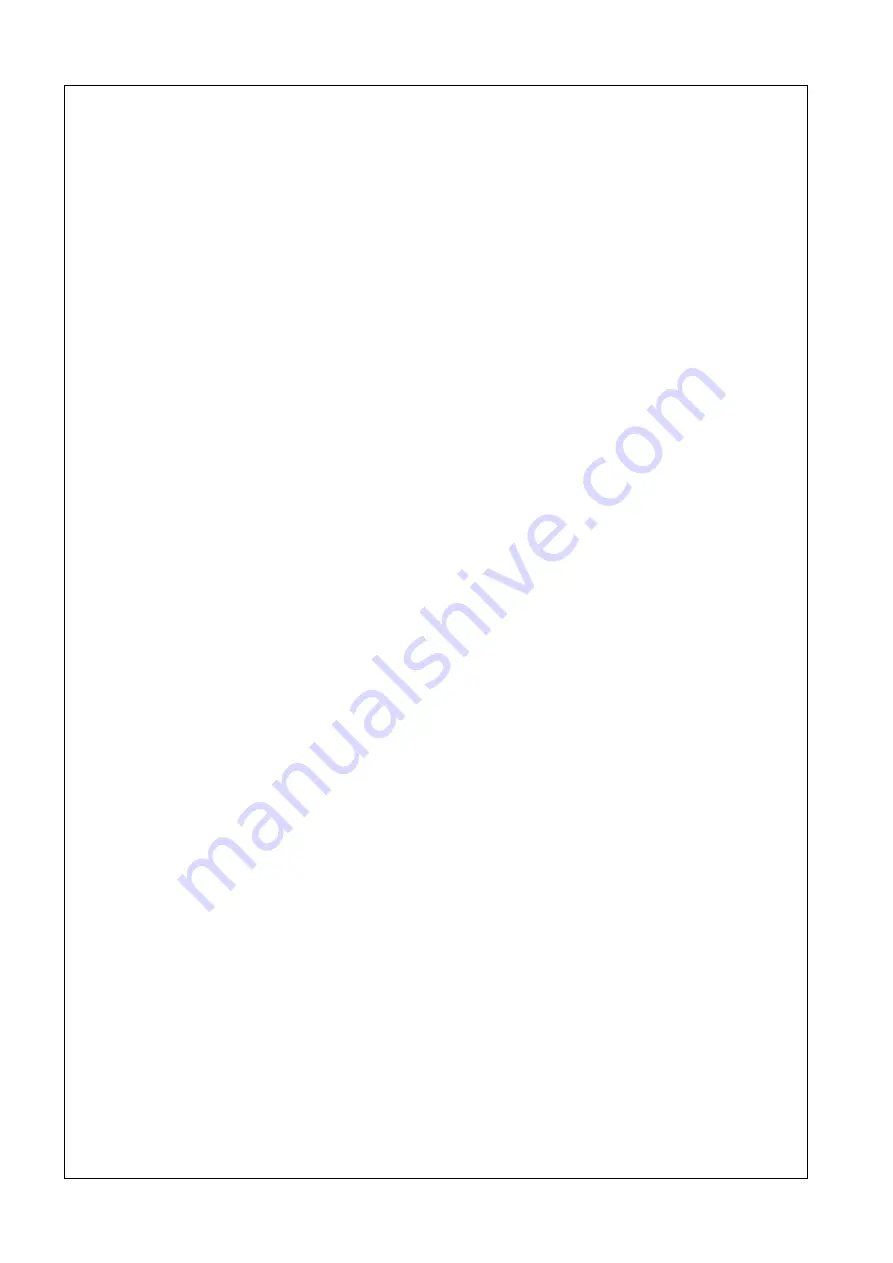
I F B - 1 3 1 O P E R A T O R ’ S M A N U A L
PAGE 22
v) Reset the central temperature monitor to a temperature of 200°C which will energise the
upper solenoid valve. Adjust the upper valve until the total indicated air flow rate is
approximately 160 l/min.
OR iib)
For units after Issue/5 (with solid state relay system).
Adjust the set point of the automatic air control temperature monitor which is located
within the electrical console so that both of the air control solenoid valves are closed. The
automatic air control temperature monitor is the left hand Eagle 848B controller.
iii) Adjust the manual valve at the left hand side of the pneumatic control console until the
indicated air flow is approximately 70 litres/min.
iv) Reset the Auto-Air temperature monitor to a temperature of 200°C which will energise the
left hand solenoid valve. Adjust the central valve until the total indicated airflow rate is
approximately 110 litres/min.
v) Reset the auto-air temperature monitor to a temperature of 400°C which will energise
both solenoid valves. Adjust the right hand valve until the total air flow rate is approximately
160 litres/min.
If the fluidisation in the bath does not produce satisfactory results when using the correct air
flow rates, the condition of the porous plate in the base of the fluidised bath must be
suspected.
An initial remedy is to operate the fluidised bath at approximately 550°C for a period of at
least one hour to allow any accumulated residue in the bath to be decomposed. However, if
the fault continues the bath should be emptied and the porous plate examined.
The fluidised bath must only be emptied when the bath is cold.
To empty the bath, use a scoop to remove the alundum, when the unit is fluidised. A small
quantity of fluidising medium will remain in the base of the bath; this should be removed
using a vacuum cleaner.
When the bath is empty, the stainless steel porous plate may be examined for any sign of
damage caused by the accumulation of plastic residue, distortion, or corrosion. Partially
blocked areas of the porous plate can be detected if the bath is fluidised with a small quantity
of fresh fluidising medium.
Removal of the porous plate assembly for renewal is as follows:
i) Turn bath upside down, remove brass elbow from air pipe.
ii) Remove 2 screws, hold thermostat bracket and lift bracket thermostat and over-
temperature cut-out sensor clear.
iii) Remove nut and washer, secure plate to bottom of chamber, remove plate and insulation.
iv) Remove nut and washer in centre of chamber this will release porous plate.
v) Turn bath upright remove old plate and fit new one, secure using nut and washer removed
in (iv).
vi) Reassemble in reverse order when fitting the new porous plate assembly. The felt
washer around the air inlet pipe should be re-sealed using a high temperature sealant such
as silicate of soda.
d) For further details of the temperature controller, see the attached Eurotherm temperature
controller instruction leaflet.
e) To check or replace the thermocouples, disconnect the thermocouple leads from the
controller and remove the thermocouple from the thermocouple pocket.
Summary of Contents for IFB-131
Page 1: ...IFB 131 OPERATOR SMANUAL Issue 8 Date of issue 3rd May 2005 Techne is a trademark Techne 2004...
Page 2: ......
Page 4: ...I F B 1 3 1 O P E R A T O R S M A N U A L PAGE 2...
Page 5: ...I F B 1 3 1 O P E R A T O R S M A N U A L PAGE 3 NOTES...
Page 27: ...I F B 1 3 1 O P E R A T O R S M A N U A L PAGE 25...
Page 28: ...I F B 1 3 1 O P E R A T O R S M A N U A L PAGE 26...
Page 29: ...I F B 1 3 1 O P E R A T O R S M A N U A L PAGE 27...
Page 30: ...I F B 1 3 1 O P E R A T O R S M A N U A L PAGE 28...
Page 31: ...I F B 1 3 1 O P E R A T O R S M A N U A L PAGE 29...
Page 32: ...I F B 1 3 1 O P E R A T O R S M A N U A L PAGE 30 Notes...