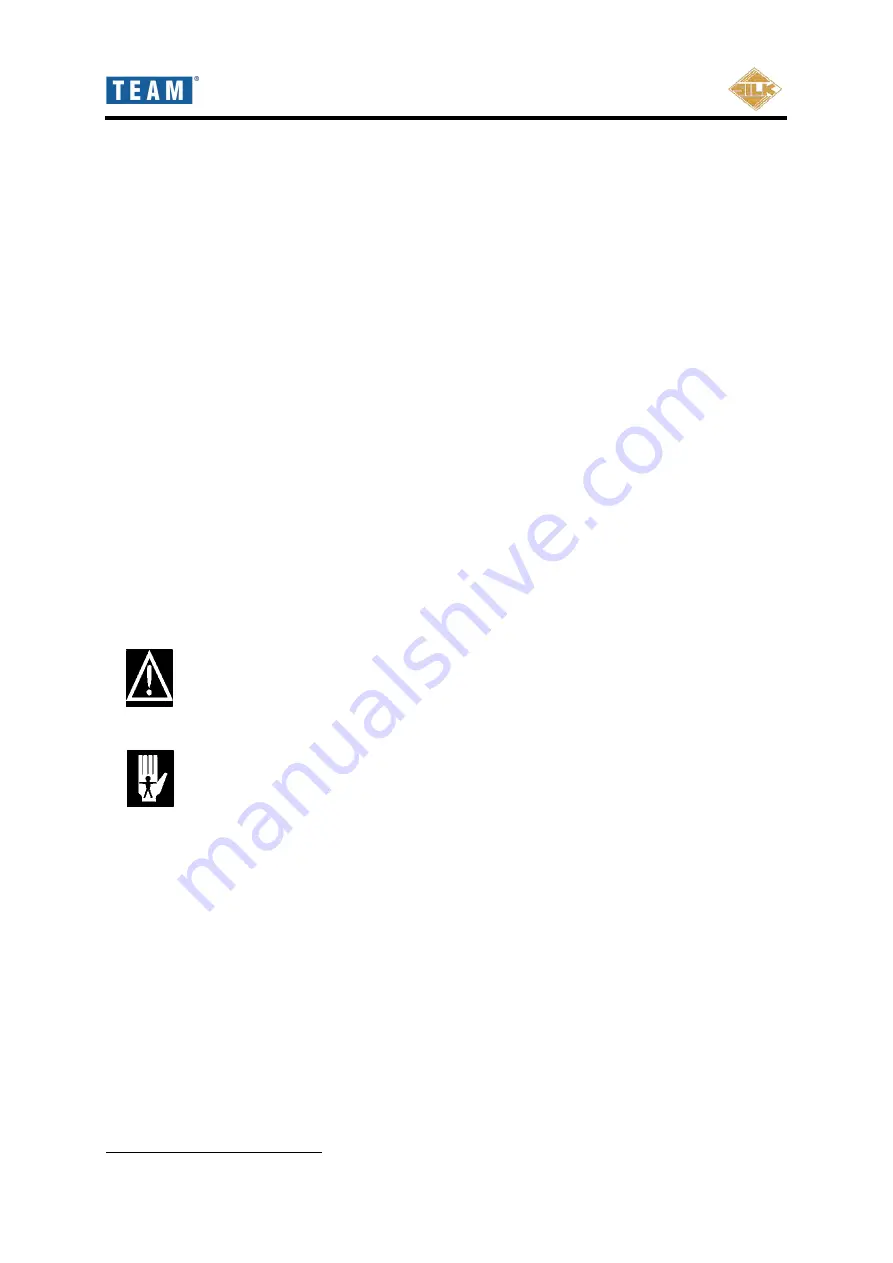
FXB630 Flange Facing and Grooving Machine
74
PACKING CASE CONTENTS
The following amendments will relate to the packing case contents –
Section 5.2
when a Hydraulic
Drive option is required the subsequent items will not be supplied;
Hydraulic Drive:
2.
Pneumatic Drive Motor with Key and Flange
16
.
Filter Lubricator
17.
Air Pipe and Control Valve
20
.
Air Motor Manufacturers Information
OPERATING INSTRUCTIONS
The following instructions are for operating the flange facing machine when correctly installed on a
flange
(See installation procedures)
it is assumed that an appropriate Hydraulic supply is available
(20l/min / 4.4GPM)
CONNECTION TO HYDRAULIC SUPPLY
When connecting the machine to the Hydraulic supply observe all warning and cautions
details;
CAUTION: ALL HOSES MUST BE CONNECTED PRIOR TO OPERATING THE
FLANGE FACING MACHINE.
ENSURE THE CORRECT PRESSURE RATED HOSES ARE USED.
1
Saeur Danfoss Technical Information – Hydraulic Systems Rev AD- June 2009
GENERAL:
(A) ALL SAFETY PROCEDURES MUST BE OBSERVED AND STRICTLY
ADHERED TO BEFORE AND WHEN OPERATING THIS EQUIPMENT.
(B) ONLY QUALIFIED AND COMPETENT PERSONNEL SHOULD OPERATE THIS
EQUIPMENT.
(C) ONLY QUALIFIED AND COMPETENT PERSONNEL SHOULD SERVICE AND
MAINTAIN THIS EQUIPMENT.
(D) IT IS ADVISABLE THAT THE HYDRAULIC POWER SUPPLY IS FITTED WITH
A SUITABLE FILTER (MAX 10µm)
1
(E) DO NOT EXPOSE THE MOTOR TO PRESSURES, PRESSURE
DROPS AND SPEEDS ABOVE THE MAX. VALUES STATED.
Summary of Contents for SILK FXB630
Page 45: ...FXB630 Flange Facing and Grooving Machine 44 Fig 24 FXB630 mast and power cap assembly ...
Page 48: ...FXB630 Flange Facing and Grooving Machine 47 Fig 25 Surfacing arm assembly ...
Page 50: ...FXB630 Flange Facing and Grooving Machine 49 Fig 26 Gearbox assembly ...
Page 53: ...FXB630 Flange Facing and Grooving Machine 52 Fig 27 Base assembly ...
Page 55: ...FXB630 Flange Facing and Grooving Machine 54 Fig 28 Toolpost assembly ...
Page 58: ...FXB630 Flange Facing and Grooving Machine 57 ...
Page 59: ...FXB630 Flange Facing and Grooving Machine 58 TOOLS FOR V GROOVE PLUNGE MACHINING ...
Page 63: ...FXB630 Flange Facing and Grooving Machine 62 APPENDIX C V GROOVE MEASUREMENT ...
Page 64: ...FXB630 Flange Facing and Grooving Machine 63 ...
Page 65: ...FXB630 Flange Facing and Grooving Machine 64 APPENDIX D AIR MOTOR MANUFACTURERS INFORMATION ...
Page 66: ...FXB630 Flange Facing and Grooving Machine 65 ...
Page 67: ...FXB630 Flange Facing and Grooving Machine 66 ...
Page 68: ...FXB630 Flange Facing and Grooving Machine 67 ...
Page 69: ...FXB630 Flange Facing and Grooving Machine 68 ...
Page 70: ...FXB630 Flange Facing and Grooving Machine 69 ...