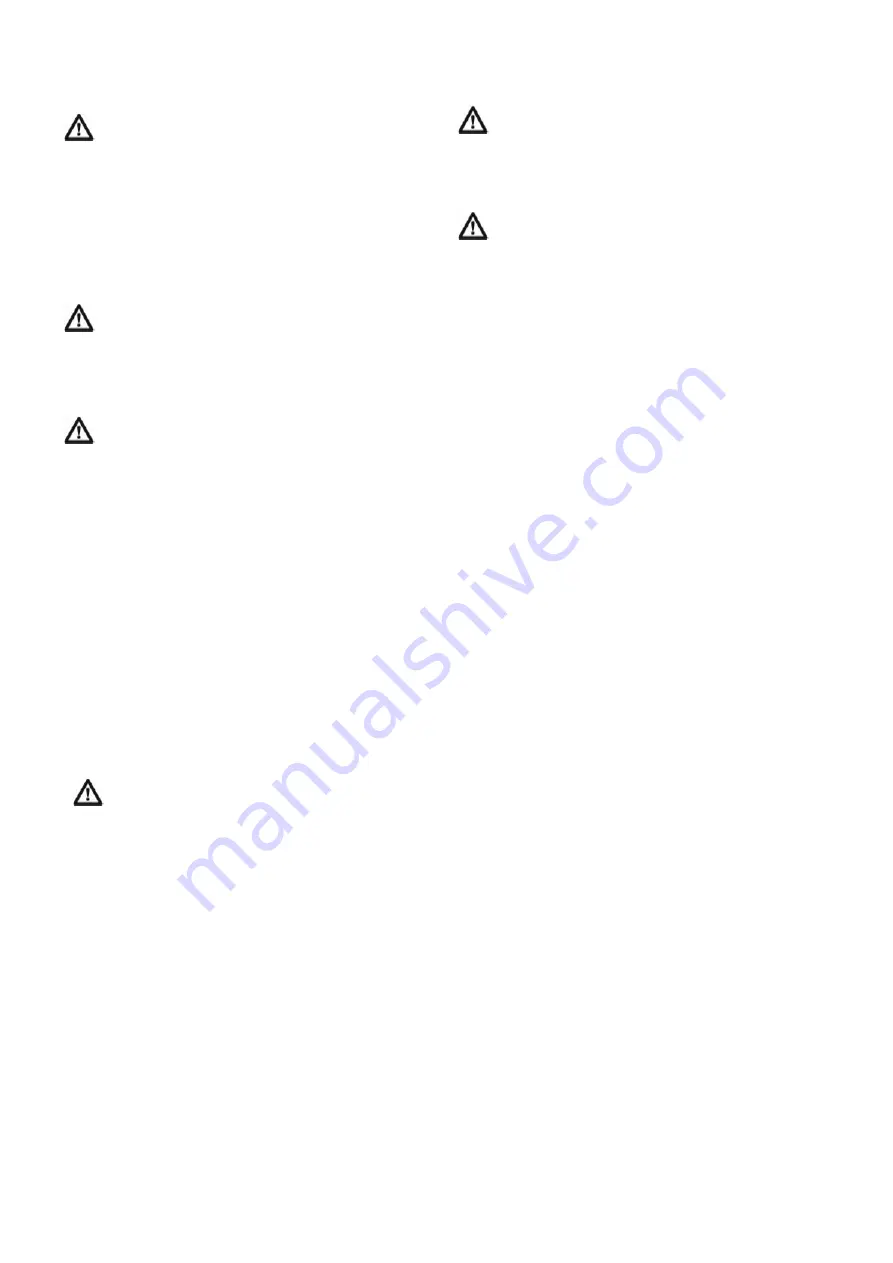
Remove the bolts retaining the rotor mounting bearings to
the frame at the front and rear of the rotor.
Due to the weight of the mill rotor assembled with the
bearings and pulley lifting equipment capable of
lifting
500kg
will be required. Attach the lifting
equipment to the rotor and remove it from the bale
chamber using a vehicle with suitable lifting equipment
capable of lifting the rotor over the height of the bale
chamber (see specifications page for height of bale
chamber).
Refitting the rotor is the reverse of the above.
12.15 Conveyor Belt
Never attempt to maintain or adjust the conveyor belt
rollers unless the PTO has been disengaged, the
engine has been stopped, the key removed and the
machine come to rest. Whilst power is connected to the
machine the red beacon will remain flashing until the rotor
comes to rest.
The hydraulic pump is driven from the drive to the
mill rotor and means that there is a risk that it can
move unexpectedly until the mill rotor has come to
rest.
12.15.1 Conveyor Belt Tension
The discharge conveyor drive roller position is adjustable
to allow for belt stretch. If the belt slows down or stops
during operation the belt will need tensioning until it stops
slipping. It is normal for the belt to sag on the lower side,
the tension should be judged on if it slips not on the
amount of sag.
Overtightening of the belt should be avoided, it may cause
damage to the belt or cause pulsation in the hydraulic
circuit.
To tension the conveyor belt unfold and lower the
conveyor belt fully. Release the locking bolts holding the
bearing tension plates. Adjust both bearing tension bolts
by the same amount until the belt stops slipping. Align belt
with the slots, on the cover but making sure it doesn’t hit
the conveyor bar.
Tighten the clamping bolts, lift the conveyor to a
working height, start the machine slowly and run the
conveyor checking that the belt is running centrally in it’s
frame avoiding damage to the belt from rubbing on the
frame. If it is not running centrally stop the conveyor and
the machine and wait until the mill rotor comes to rest.
Adjust the position of 1 tensioner, retighten and test the
operation of the conveyor again.
It may be necessary to adjust the front roller to ensure the
belt is running centrally. This can be achieved by
releasing the bearing mounting bolts on one side of the
conveyor and adjusting the position of the bearing.
12.15.2 Conveyor Belt Replacement
Should it be necessary to remove or replace the conveyor
belt extend and fully lower the conveyor. Stop the
conveyor belt with the joint on the upper surface just in
front of the tension roller. Stop the machine and wait until
the mill rotor comes to rest. Release the locking bolts
holding the bearing tension plates and take the tension
roller to it’s fully slack position. Lift the belt and remove
the pin from the joint. Pull the belt from the conveyor
frame.
Reassembly is the reverse of the above procedure.
12.16 Hydraulic Circuit
Never attempt to maintain the hydraulic circuit
unless the PTO has been disengaged, the engine
has been stopped, the key removed and the
machine come to rest. Whilst power is connected to the
machine the red beacon will remain flashing until the rotor
comes to rest.
The hydraulic pump is driven from the drive to the
mill rotor and means that the pump will continue to
operate until the machine comes to rest.
If the machine has been operating then the hydraulic oil
and components will be hot, allow time for the system to
cool before working on the hydraulic circuit.
Before working on the hydraulic circuits to operate the
rams that position the conveyor make sure that the
conveyor is unfolded and fully lowered to avoid there
being oil under pressure in the circuit.
12.16.1 Hydraulic Oil Reservoir
All machines are delivered from the factory filled with
hydraulic oil. With the machine on level ground and
attached to tractor the oil level in the reservoir should be
in between the minimum and maximum marks on the
sight gauge on the left hand side of the tank.
Only a good quality ISO HV46 grade hydraulic oil should
be used. Total capacity of the tank is approximately 150
litres (33 gallons).
When filling the tank make sure the strainer inside the
filler cap is in place.
12.16.1 Hydraulic Oil Change
The most accurate way of determining when the oil needs
replacing is to undertake oil analysis to check if the base
oil has degraded or if the additive package has become
depleted. As a guide a 1000 hour oil change interval
would be recommended.
To drain the tank remove the drain plug at the base of
the tank and collect the oil in suitable containers. Oil
may drain faster if the filler cap is loosened.
Waste oil is considered to be a hazardous substance and
as such should be stored and disposed of in compliance
with local legislation.
Whilst the tank is empty the condition of the suction filter
should be checked by removing the filler cap assembly
and visually inspecting it. Should it need to be replaced it
can be removed by reaching down into the tank and
unscrewing it. Screw the new filter into the tank.
Replace the drain plug and refill the tank.
12.16.2 Return Filter
The return line filter should be changed when the gauge
on top of the filter housing indicates it needs replacing.
Failure to replace the element at the appropriate time will
result in the filter bypass opening when the back pressure
reaches 1.75 bar. At this point filtration will no longer be
taking place exposing all elements of the system to
damage. The filter should be replaced when the indicator
on the gauge fitted to the top cover reads 1.4 bar (the top
of the green section on the gauge).
To replace the element remove the 3 screws holding the
top cover onto the filter body, there is a spring underneath
14