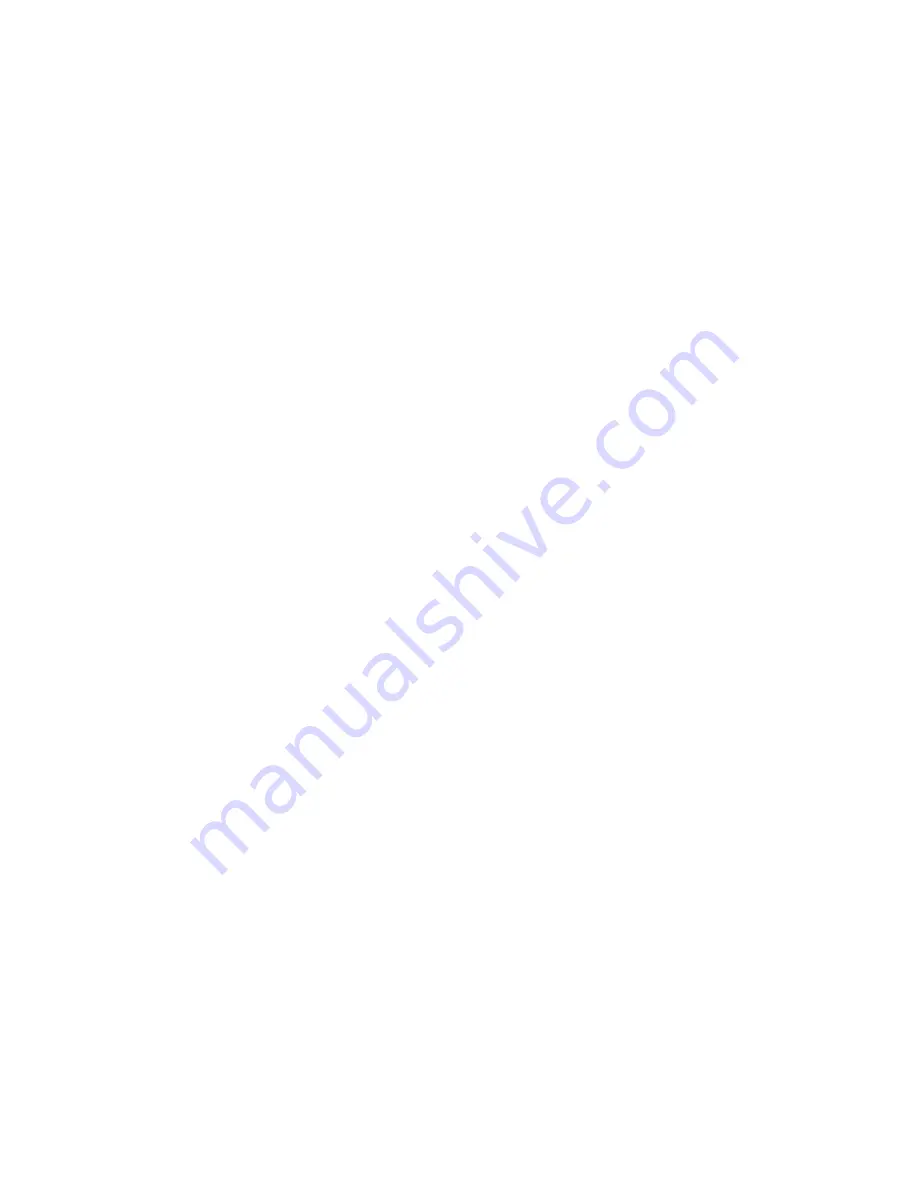
7
1.4 Turn power on to both the computer and power supply (which in turn powers up the controller).
The on-board green LED will flash at a steady rate to indicate that the controller is energized
correctly.
1.5 Insert the TC-24-25 RS232 software disk into the computer floppy-disk drive. To run the software
from the floppy disk, select START, RUN from your Windows Desktop and then enter A:\TC-24-
25 RS232.exe. This will load the software into your computer's RAM. Alternatively, copy the TC-
24-25 RS232.exe file to your hard-disk drive and run the program from there.
1.6 The Main Menu screen will appear on your computer monitor. All selections are made from this
menu screen. In the PC COMMUNICATIONS section, select the RS232 comm port (1 through 4)
to which the controller is connected by using the SELECT COMM PORT menu key. After making
this selection, click on the INITIALIZE button.
1.7 NOTE: If you receive an error message, please refer to Appendix A “
Troubleshooting
Communications Port
.”
2.0 Configure
2.1 In the CONFIGURE section, the various selections are used to establish the custom operating
criteria for the controller.
NOTE: To avoid damage to the thermoelectric cooler, confirm that
OFF
is selected in the
OUTPUT ON/OFF
menu key and then click the Send Box Values button prior to
proceeding!
2.2 First, select the PWM OUTPUT TIMEBASE menu key. Options for SLOW TIMEBASE 675Hz or
FAST TIMEBASE 2700Hz will appear. Select the option that is appropriate for you. Generally,
675 Hz will work fine and is the recommended default.
2.3 Next, click on the SET TEMP TYPE INPUT 2 menu key to reveal the options available.
COMPUTER SET VALUE is to be selected when using the software to set the desired control
temperature. The other selections, POTENTIOMETER SET, 0 TO 5vdc SET, and 0 TO 20ma SET,
are for external set temperature adjustments. Refer to the “
Controller Wiring Diagram
” and the
“
Block Diagram
” for additional information. The controller default setting for these options is the
full range of the thermistor input sensor. The DIFF.SET=INP2+FIXED SET establishes an actual
set temperature that is the sum of the temperature sensed by the optional, secondary thermistor input
sensor and the temperature entered as the FIXED SET TEMP value. This allows the controller to
maintain a constant temperature difference between the primary thermistor temperature and the
secondary thermistor.
2.4 Enter the SET TEMP HIGH RANGE and SET TEMP LOW RANGE values. These values are used
to linearly scale the temperature range that you are controlling within to the full range of the
external input. The set limit values must be within the temperature range that controller is capable
of controlling to.