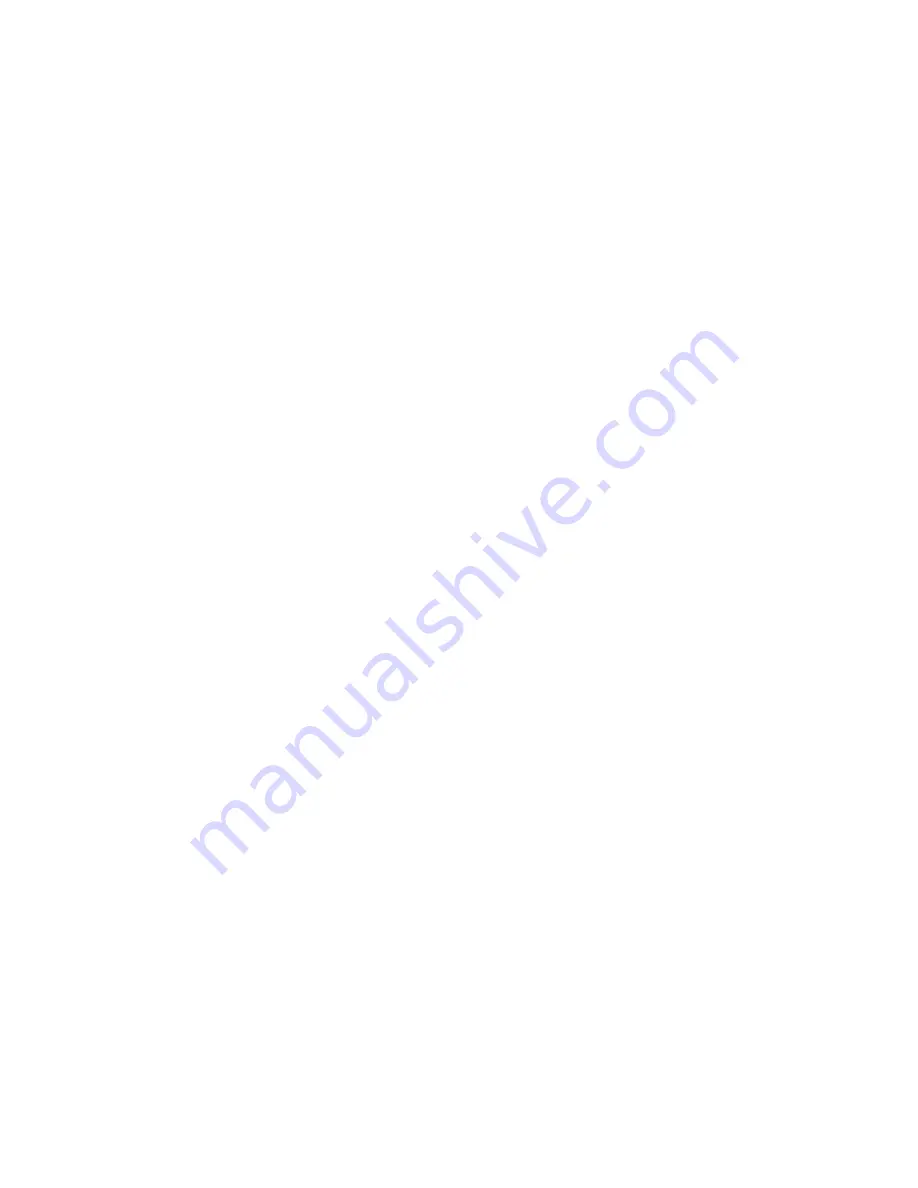
6
Set-Up Instructions
1.0 Setup
NOTE: the maximum allowable ambient temperature for the controller is 65 °C. Furthermore, the
maximum allowable temperature of the controller base (underneath the transistor-mounting area) is 80
°C.
1.1 Make sure the computer is off and the controller is un-powered. Connect the RS232
Communications Port from the controller (JP3) to the RS232 input (Serial Communications Port) on
the computer. Pin 1 of JP3 is the controller’s RX, Pin 2 of JP3 is the controller’s TX, and Pin 3 of
JP3 is the controller’s shield. Pin 1 of JP3 should connect to the clear wire on the RS-232 cable, Pin
2 of JP3 should connect to the red wire on the RS-232 cable, and Pin 3 of JP3 should connect to the
black wire on the RS-232 cable. See “
RS232 Communications Connections
” for further
information.
1.2 Attach the thermistor to the control location. Generally, this is the cold side of the cooler rather than
the part itself that is to be cooled/heated. This provides better control stability. As much wire
length of the thermistor should be thermally connected to the cold side as possible so that the
thermistor and its wire leads are as equivalent in temperature as possible. This can be accomplished
by using aluminum tape placed over the wire leads and adhered to the cold side of the cooler. This
will help eliminate errors resulting from heat conducting along the wire leads and affecting the
sensor reading.
The standard thermistor supplied with the TC-24-25 RS232 is the MP-2379. Appendix D
“
Thermistor Styles for TC-24-25 RS232
” shows dimensional data on the MP-2379 and other
thermistor styles readily available as well as temperature-resistance data. If you are using the MP-
2379, it is recommended that you use thermal grease (such as TE Technolgy TP-1) between the
thermistor and the surface to which it is mounted.
If you want to use thermistors that have different resistance-temperature curves than the standard
thermistor, it can be done as long as the operating resistance range is within that of the standard
thermistor. The thermistor should be a negative temperature coefficient device. Because the
temperature controller is really measuring the thermistor’s resistance and converting this to a
temperature, the temperature controller will be fooled into thinking that the thermistor is at a
different temperature than it really is, and the Set-Temperature will be skewed accordingly. A loss
of resolution and control stability may occur as a result. The user assumes all risks associated with
making any substitutions and TE Technology assumes no liability whatsoever for the operation of
the controller when a non-standard thermistor is used.
1.3 Connect the appropriate DC power (12 to 28 volts) to the controller between WP3+ and WP4- and
the thermoelectric cooler between WP1 and WP2 in accordance with the “
Controller Wiring
Diagram
.” NOTE: Generally there is approximately a 0.5 to 1.3 V drop from the power supply to
the thermoelectric modules. You may want to adjust the power supply accordingly to ensure full
power is delivered to the cooler when needed.