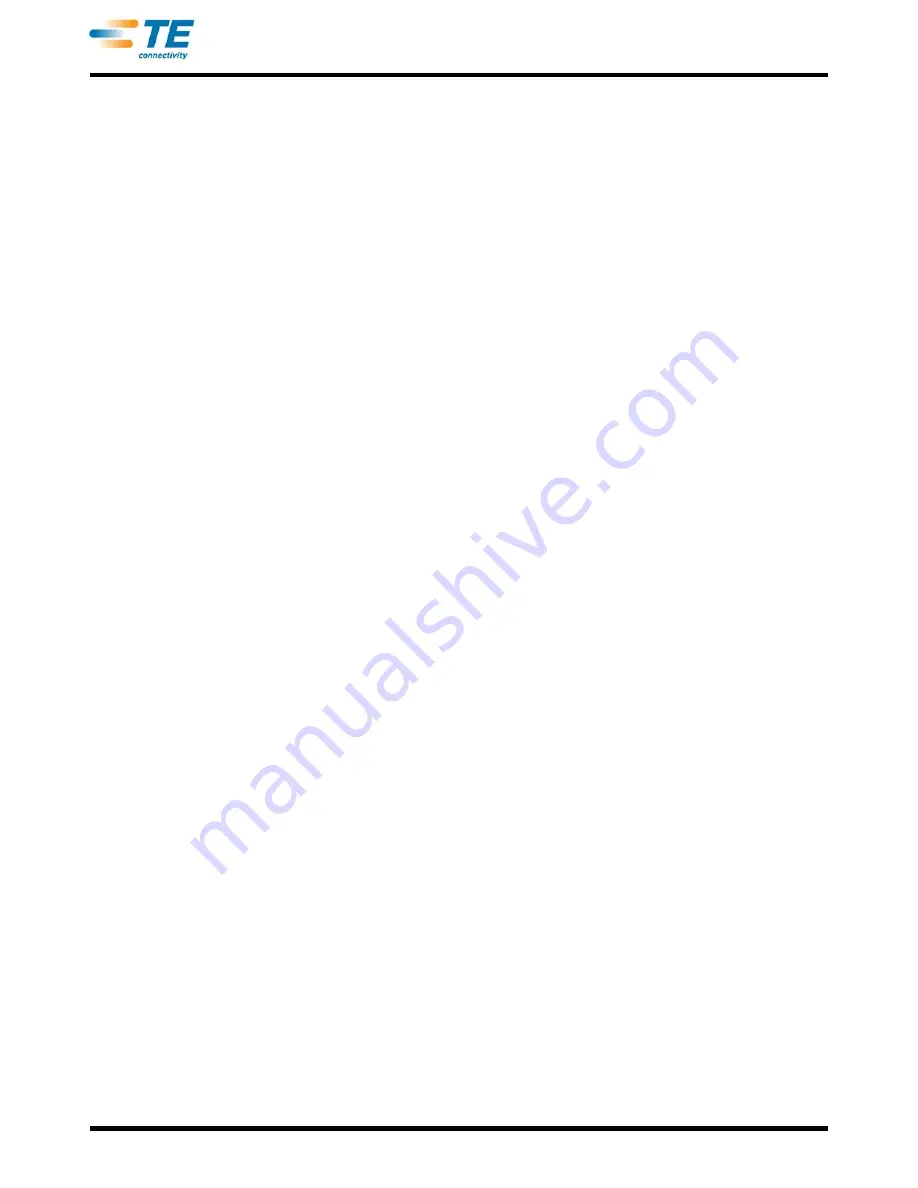
409-2908
20
of 32
Rev A
8.2. General Disassembly Procedure
The following steps are common to most of the tool maintenance procedures given in the paragraphs to follow.
Perform the following steps, as specified in each maintenance procedure, to prepare the tool for repair and/or
part replacement:
1. Unload clips from tool (Paragraph 6.7).
2. Remove mandrel (Paragraph 6.2).
3. Remove “E” ring (Item 72), and slide “O” ring (Item 63) and cover plate (Item 69) down over tubing. See
Figure 32.
4. Remove three screws (Items 85 and 74) from side cover and remove side cover (Item 4). Also, to prevent
parts from falling out of tool and being lost, remove clip positioner (Item 44) with spring (Item 43) and remove
spring (Item 42) from right post pickup (Item 86). See Figure 32.
5. Refer to applicable maintenance procedure for additional instructions.
8.3. General Reassembly Procedure
1. Assemble clip positioner (Item 44) in position and insert spring (Item 43, 1-1/4 in. long) into hole in clip
positioner. Also, place spring (Item 42, 5/16 in. long) into hole in right post pickup (Item 85). See figure 32.
2. Ensure that pin (Item 116) (installed in side cover) fits into spring in clip positioner and that spring in right
post pickup fits into hole in side cover. See Figure 32.
3. Install and tighten three screws (Items 85 and 74). The shorter screw (Item 74, 3/8 in. long) goes into hole
near reel bracket, and the longer screw (Item 85, 5/8 in. long) go into the other two holes. After tightening
screws, ensure that post pickups and clip positioner dial operate properly.
4. Bottom cover plate (Item 69) against tool handle, position “O” ring (Item 63) against cover plate, and install
“E” ring (Item 72) in slot in handle. See Figure 32.
5. Install mandrel (Paragraph 6.1).
6. Load clips into tool (Paragraph 6.4).
8.4. Pneumatic Assembly - Disassembly and Reassembly
1. Perform all steps given in general disassembly procedure (Paragraph 8.2)
2. Remove four screws (Item 85) holding top cover (Item 51) to tool. Slide front of top cover to right from under
pin (Item 39) in lever linkage (Item 38) to release top cover assembly from tool. See Figure 32.
3. Lift right post pickup (Item 86) from its pin (Item 98) and lay it aside. (This will keep this part from swinging
or falling out of tool while repairs are being made.)
4. Lift push rod (Item 79) from its pin (installed through shaft of air cylinder) and remove push rod.
5. Remove screw (Item 67 to release air block (Item 7) from tool.
6. Remove two pipe-to-hose fittings (Item 113) and disconnect air hose (Item 129) from air block. Do not lose
“O” ring (Item 10) on top opening of air block. Air block assembly can now be repaired or replaced, as
required. Cartridge valve (Item 8) can easily be pulled out of the air block and replaced, if necessary.
7. For repair or replacement of air cylinder subassembly (Item 108), remove end cap (Item 109) to release
end cover (Item 60) and air cylinder cover (Item 64) and remove these items. Use care not to lose “O” rings
(Items 63 and 59). Remove screw (Item 85) and stop (Item 50) to release shaft of air cylinder, and then
unscrew air cylinder subassembly from tool. Tilt rear of air cylinder up to allow drive pin in shaft of air cylinder
to clear tool and remove air cylinder subassembly from tool.
8. To reassemble pneumatic assembly, perform steps (2) through (7) previously in reverse order. Be sure that
drive pin in air cylinder shaft is positioned in slot in top of tool before screwing air cylinder into tool. After
screwing air cylinder subassembly into position, use a screwdriver against the drive shaft pin (through slot in
top of tool) to carefully force air cylinder shaft out far enough to install stop (Item 50). Use care to ensure that
“O” rings (Items 59, 63, and 10) are properly assembled. Otherwise, tool will have excessive air leakage
during operation. Also, ensure that tubing (Item 112) and air hose (Item 129) are properly assembled and that
pipe-to-hose fittings are tight.