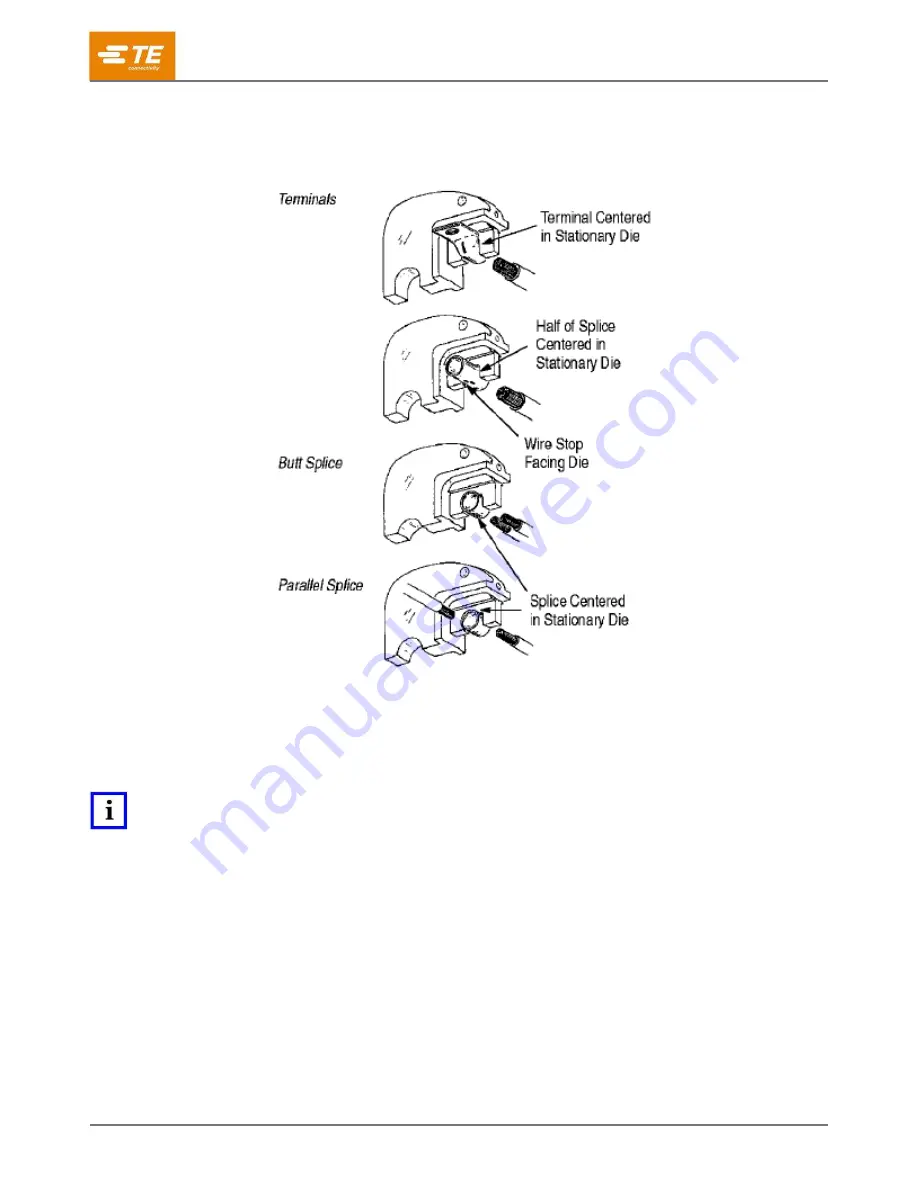
408-1602
Rev
C
4
of 11
4.2.
Using Single-Crimp Die Assembly
1. Center the terminal or splice in the stationary die as shown in Figure 4.
Figure 4
2. Activate the power unit so the moving die advances and holds the terminal or splice in place; but
without deforming the wire barrel.
3. Insert the stripped wire until it bottoms in the terminal or splice.
NOTE
The end of the wire must be visible thru the sight hole.
a. For parallel splices, make sure the ends of the wires are at least flush with, or extend slightly
beyond the end of the wire barrel.
b. For butt splices, make sure the wire stop faces either die.
4. Activate power unit to complete crimp.
5. To crimp the other half of a butt splice, remove and position the un-crimped half in the stationary die.
Insert wire until it bottoms against wire stop and crimp the splice.
6. Remove the terminal or splice from the dies and inspect the crimp in accordance with Section 5;
CRIMP INSPECTION.