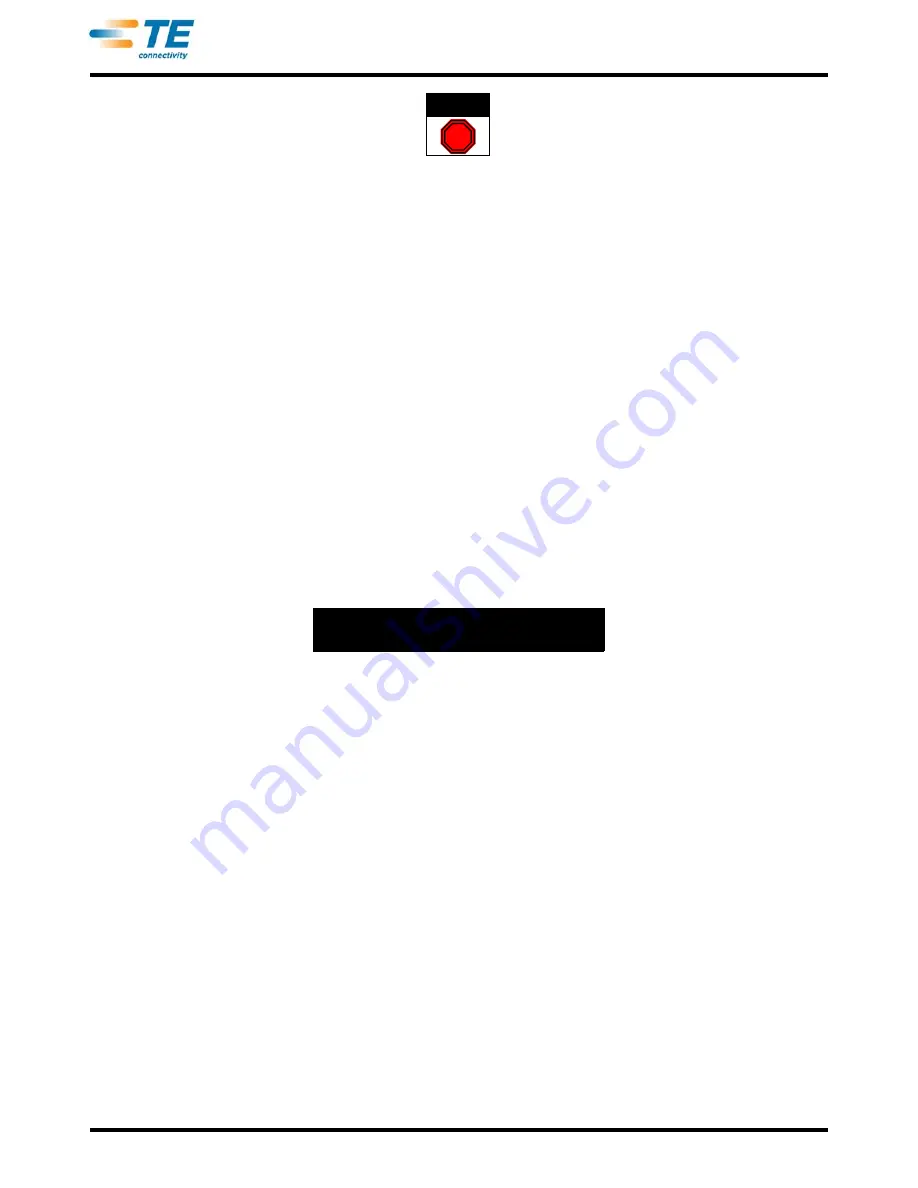
409-10064
SAFETY PRECAUTIONS AVOID INJURY
Safeguards are designed into this application equipment to protect operators and maintenance personnel from
most hazards during equipment operation. However, certain safety precautions must be taken by the operator
and repair personnel to avoid personal injury, as well as damage to the equipment. For best results, application
equipment must be operated in a dry, dust-free environment. Do not operate equipment in a gaseous or
hazardous environment.
•
Carefully observe the following safety precautions before and during operation of the equipment:
•
ALWAYS wear appropriate ear protection.
•
ALWAYS wear approved eye protection when operating powered equipment.
•
ALWAYS keep guard(s) in place during normal operation.
•
ALWAYS insert power plug into a properly grounded receptacle to avoid electrical shock.
•
ALWAYS turn off the main power switch and disconnect electrical cord from the power source when
performing maintenance on the equipment.
•
NEVER wear loose clothing or jewelry that may catch in moving parts of the application equipment.
•
NEVER insert hands into installed application equipment.
•
NEVER alter, modify, or misuse the application equipment.
TOOLING ASSISTANCE CENTER
CALL TOLL FREE 1-800-722-1111 (CONTINENTAL UNITED STATES AND PUERTO RICO ONLY)
The
Tooling Assistance Center
offers a means of providing technical assistance when required.
In addition, Field Service Specialists are available to provide assistance in the adjustment or repair of the
application equipment when problems arise which your maintenance personnel are unable to correct.
INFORMATION REQUIRED WHEN CONTACTING THE TOOLING ASSISTANCE CENTER
When calling the Tooling Assistance Center regarding service to equipment, it is suggested that a person familiar
with the device be present with a copy of the manual (and drawings) to receive instructions. Many difficulties can
be avoided in this manner.
When calling the Tooling Assistance Center, be ready with the following information:
1.
Customer name
2.
Customer address
3.
Person to contact (name, title, telephone number, and extension)
4.
Person calling
5.
Equipment number (and serial number if applicable)
6.
Product part number (and serial number if applicable)
7.
Urgency of request
8.
Nature of problem
9.
Description of inoperative component(s)
10.
Additional information/comments that may be helpful
2 of 26
Rev B
DANGER
STOP