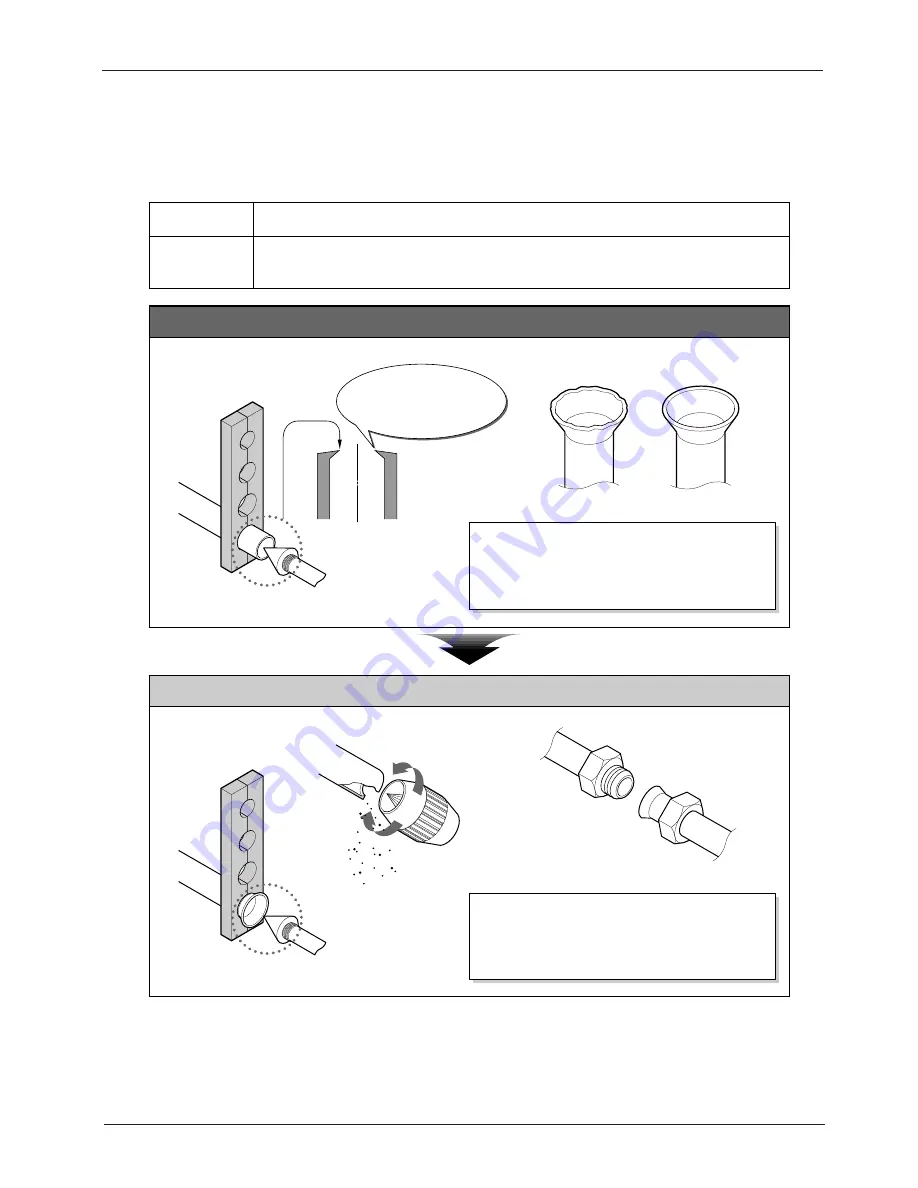
Leakage /Freon - 2/4
Case-2
Key Factor
Removing burrs of pipes.
Gas Leaks due to the burrs caused by cutting and not removing properly.
Troubles &
Causes
Defect Details
Guidelines
Reamer
• Burrs should be removed clearly with REAMER.
• Only clean surfaces prevent gas leakages.
Burrs not removed properly
after cutting.
• Flaring the pipe with burrs(not removed after cutting)
can make freon gas leakages.
• Burrs won't make smooth contacting surfaces.
TCL Air Conditioner Service Manual
21