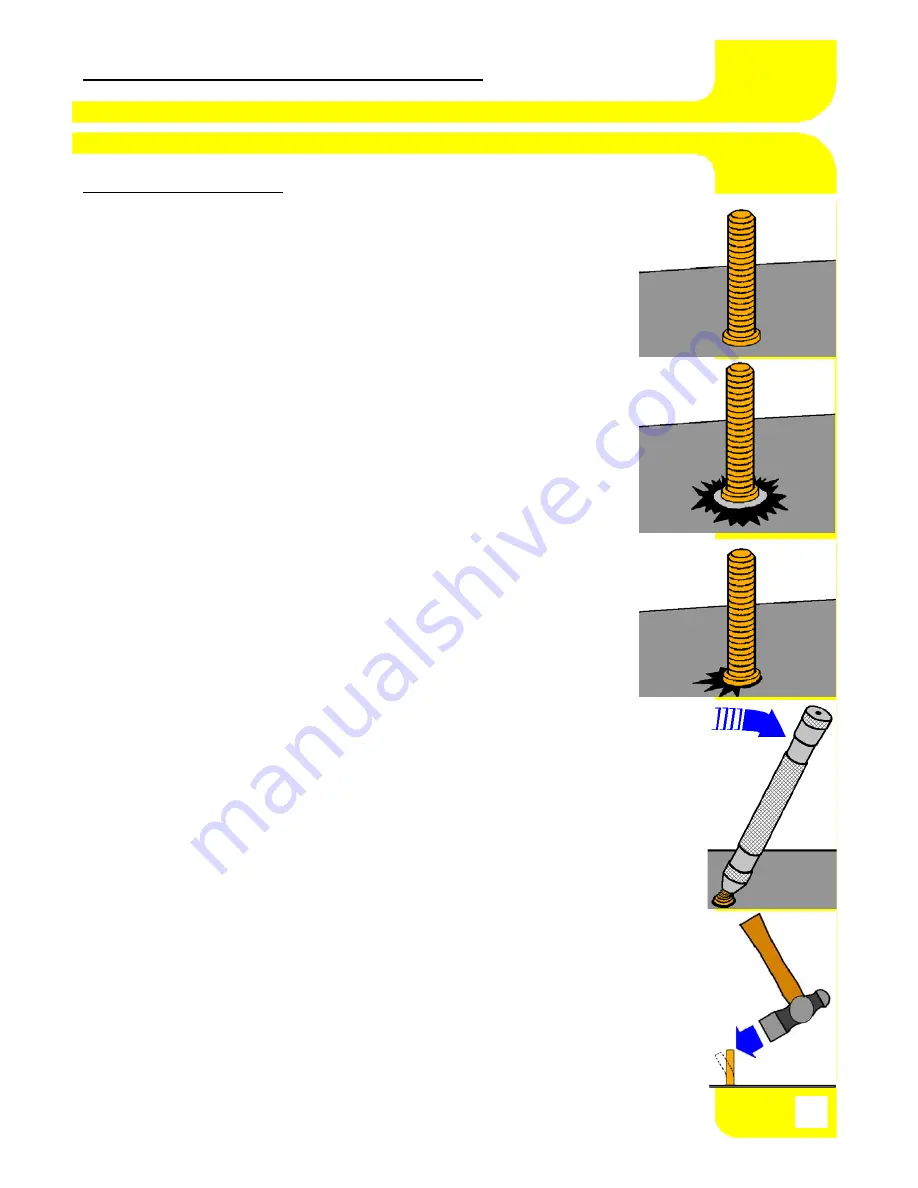
SETTING UP & WELDING
SETTING UP & WELDING
A cold stud weld is noticeable by undercutting of the flange and
lack of / minimal formation of spatter. A cold weld is usually
caused by too little energy and / or too high spring pressure.
A hot stud weld is noticeable by excessive spatter formation and
partial melting of the flange. A hot weld is usually by too much en-
ergy and / or too little spring pressure.
A one sided stud weld (arc blow) is usually caused by incorrect
earthing of the work piece. This may be corrected by placing the
welding earths opposite each other across the area where the weld
is to occur.
Finished studs may be subjected to a bending test to ascertain the
strength of the weld. This may be achieved by placing a bending
bar assembly, fitted with the correct nozzle, over the stud and
bending the stud through 30° and then back to the vertical. This
test follows the specification of DVS 0905 part 2.
A simpler test may be achieved by bending the stud over 30° using
a hide mallet.
15
Summary of Contents for SYSTEM CD200 SERIES
Page 44: ...EMC CERTIFICATE 42...