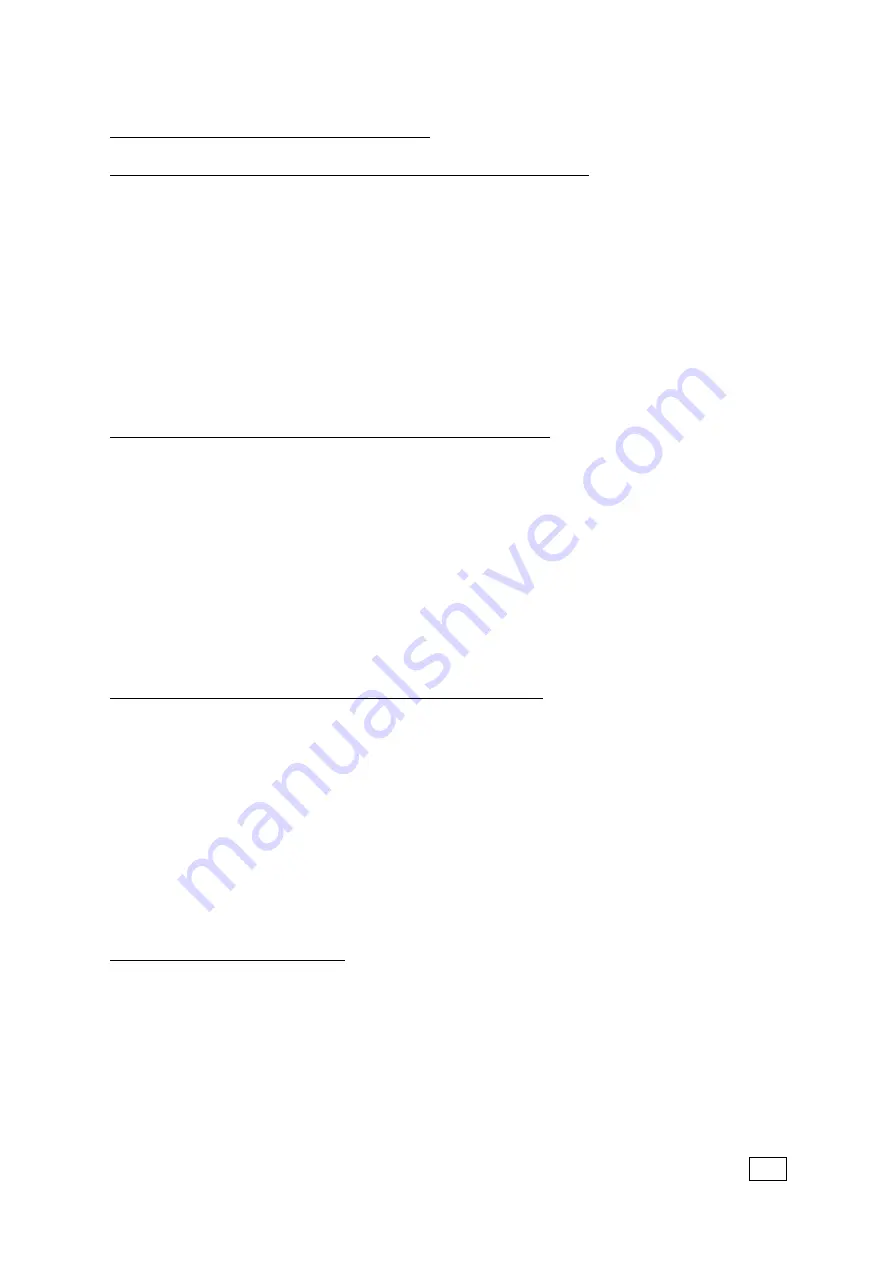
V
-
21A
STUDWELDING TECHNIQUES
20
5. WELDING STUDS LESS THAN 25 mm LONG USING FERRULES.
As we have seen previously, the stud is held in a recess in the chuck and must be long
enough to allow us to set the correct protrusion. A standard chuck has a recess 12 mm
deep and ferrules vary in length up to 13.5 mm high. Thus if a stud is much less than 25
mm LAW we shall not be able to obtain the correct protrusion, i.e.. The chuck may hit the
ferrule on the return stroke and prevent the stud returning to the plate correctly.
This problem may be overcome by using "shallow recess" chucks (the recess depth is only
6 mm) or if the studs are required to be very short, by using a special type of stud known
as a "break-off" type. These studs have an overall LAW of 30 mm and are welded using a
standard chuck and ferrule. The stud is "grooved" at the required length from the welding
end. After welding, the surplus portion of the stud is broken off with a pair of pliers. By
these means, very short studs can easily be welded.
6. USING TEMPLATES TO ENSURE POSITIONAL ACCURACY.
When welding studs around the periphery of a flange, i.e. for cover plates, inspection
doors etc., positioning of the studs in relation to each other becomes most important. A
simple template made from 2 mm sheet, shaped to suit the component and provided with
clamps is usually the answer to this problem. The position of the studs is accurately
marked and holes drilled in these positions to accept either the ferrule of the stud to be
welded or, if using short cycle, the pistol gas shroud. The size of the holes should be the
outside diameter of the ferrule / 0.4 mm. It is also advisable to provide 2 mm
thick pads underneath the template so that there is a space between the component and
template, this space will allow the gases developed during welding to vent properly from
the ferrule / shroud. For any further advice or help in the design of jigging or templates
contact your local field sales engineer.
7. MINIMUM PLATE THICKNESSES WHEN STUD WELDING.
When using standard Drawn Arc with ceramic ferrules, the minimum ratio of stud diameter
to plate thickness is 4 : 1 for plate thickness greater than 3 mm and 3 : 1 for plate
thickness between 1.5 mm and 3 mm. When using the short cycle system with or without
gas purging it is possible to weld equivalent size studs onto slightly thinner sections, due
to the short weld duration. These ratios ensure that the strength of the plate is sufficient to
support a stud of a given size when it is loaded, without there being a tendency for the
plate to distort.
Occasionally, however, it may be necessary to weld a stud outside of these ratios. This
can sometimes be accomplished without distortion by "heat sinking" the component, by
using a flat copper or water cooled backing piece behind the weld area, to support the
plate and assist in dissipating heat quickly.
8. WELDING STAINLESS STEEL.
Austenitic stainless steel studs of the 18/8 g/N : weld decay proof type can be supplied for
welding to similar parent material or mild steel. The technique does not differ from that
used for mild steel stud welding. There is a tendency with larger diameters of stainless
steel studs for metal transfer across the arc to take the form of large particles. If short
circuits occur then the arc can be heard to splutter. This may occur with any diameter of
stainless steel stud if the lift of the hand tool is not correct. Due to this tendency to transfer
in large particles increased lift may be required and time settings should be kept as low as
possible.