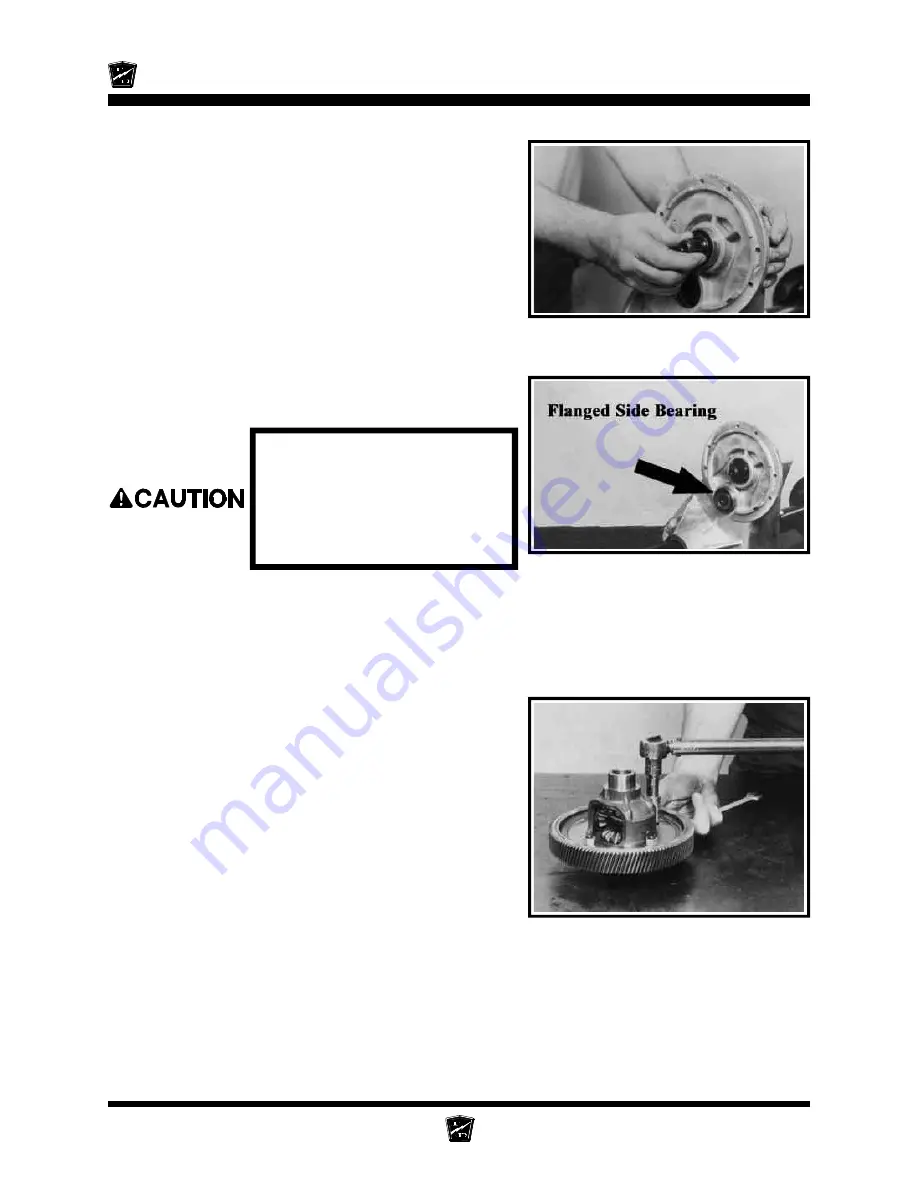
Maintenance, Service, and Repair
Transmission
Page 14
4. Install the input shaft into the housing and install
the snap ring.
5. Insert the intermediate shaft into the housing and support in place.
6. Insert the flanged side bearing into the bearing bore.
Press in just past the snap ring grove and install
the snap ring.
7. Repeat the above step for the opposite bearing.
8. Thoroughly clean both sides of the intermediate bore. All contaminates must be removed.
9. Apply Loctite #RC 609 to both sides of the intermediate bore and install new bore plugs.
NOTE: Drive the bore plugs until they are firmly seated against the snap
rings.
10. Install the final drive gear onto the differential
housing. Torque the nuts to 35-45 ft-lbs.
11. Install the differential assembly into the drive
housing and install the bearing caps. Torque the
bolts to 35-45 ft-lbs.
NOTE: The bearing caps are marked for
identification and must be installed in
their original locations.
12. Place a small bead of non-acidic silicone sealant
to the bottom flange of the housing.
NOTE: The sealant bead should be on the
inside of the cover plate mounting holes.
13. Install the cover plate. Torque the bolts to 18-28 ft-lbs.
14. Install the axles using new axle seals. Refer to
Rear Axle
section for information on installing
the axles.
15. Fill with 11 ounces of oil. Refer to the
Lubrication Table
for the proper type of oil.
Use a hard wood dowel the
same diameter as the bearing
bore to drive the bearing into
place. Do not drive against the
inner race as this will damage
the bearing.
Summary of Contents for B0-015-00
Page 2: ......
Page 6: ...TAYLOR DUNN...
Page 14: ...Model B 1 00...
Page 30: ...TAYLOR DUNN...
Page 36: ...TAYLOR DUNN...
Page 52: ...TAYLOR DUNN...
Page 66: ...Maintenance Service and Repair Steering Page 14 Exploded View of Steering Gear...
Page 90: ...TAYLOR DUNN...
Page 124: ...TAYLOR DUNN...
Page 130: ...TAYLOR DUNN...
Page 161: ...Wire Diagrams...
Page 194: ...Illustrated Parts PARTS PAGE 10 Front Suspension 4 3 2 1 5 10 6 8 9 7 11 12...
Page 202: ...Illustrated Parts PARTS PAGE 18 Motor 2 3 5 6 4 7 8 1 9 10 Armature 9...
Page 206: ...Illustrated Parts PARTS PAGE 22 Wheels and Tires Ref wheel hub 1 2 5 assembly 4 3 6 7 8 9...
Page 208: ...Illustrated Parts PARTS PAGE 24 Instrument Panel dash...
Page 217: ...Illustrated Parts PARTS PAGE 33 This page intentionaly left blank...
Page 220: ...Illustrated Parts PARTS PAGE 36 Seat Cushions Deck and Lights B 1 50...
Page 222: ...Illustrated Parts PARTS PAGE 38 Seat Cushions Deck and Lights MX 1600...
Page 224: ...Illustrated Parts PARTS PAGE 40 Decals B 1 50 VIEW FROM INSIDE OF COWL 1 2 3 4 5 6 7 8 9...
Page 230: ...Illustrated Parts PARTS PAGE 46 Stake Sides B 1 50 1 2 3 4 5 6 7 8...