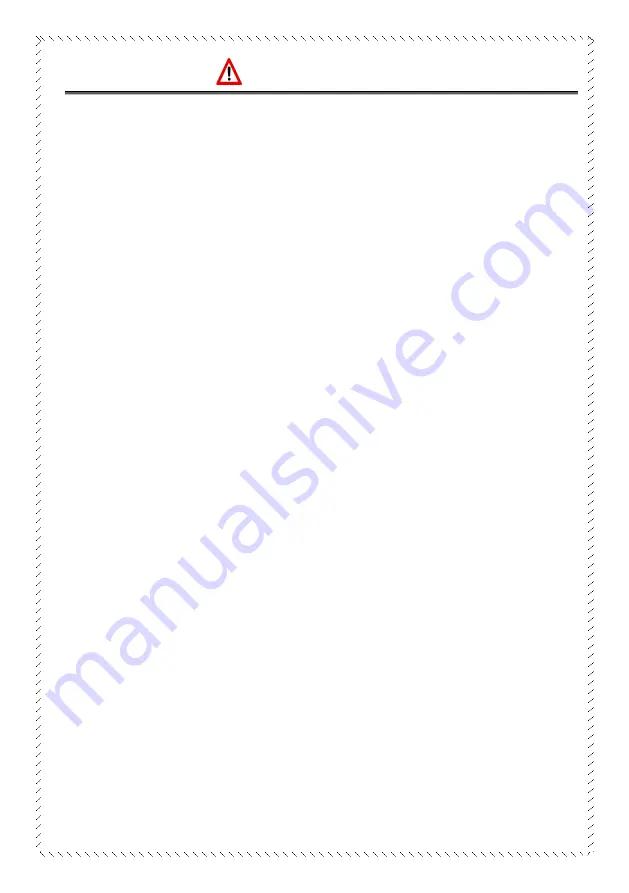
- 3 -
Safety Precautions
The equipment is designed for use by qualified personnel who have completed
professional training and have obtained a qualification certificate as a welder/cutter.
The operator shall have sufficient professional knowledge of welding, cutting and
circuitry. The machine should be operated only after having read and fully
understood all the safety precautions and warnings contained in this manual and
those generally applicable to welding operations. The risk of personal injury and
damage to equipment is reduced by safety precautions being followed when using
tools and equipment. This machine is easy to operate and the selection of its
functions is straight forward. Improper use and maintenance will reduce the safe
operation of the machine and the following safety precautions must be followed:
1.
The operator must be suitably qualified and certificated before operating the
equipment.
2.
A qualified professional should be employed to ensure that the machine and all
cables are properly connected, grounded and installed.
3.
Personal protective equipment approved by the local safety authority must be
used. All relevant safety procedures must be adhered to.
4.
Before operation, insulation layers on wires and cables as well as connection
sequences should be inspected and corrected if required.
5.
Repairs and maintenance should be carried out by qualified technicians only
after the machine has been disconnected from the electricity supply.
6.
Operating the machine in a humid environment may result in a short circuit or
may cause an electric shock to the operator.
7.
Modifications to the machine or equipment are not allowed.
8.
The disposal of scrap machine parts and equipment must comply with local
regulations
.