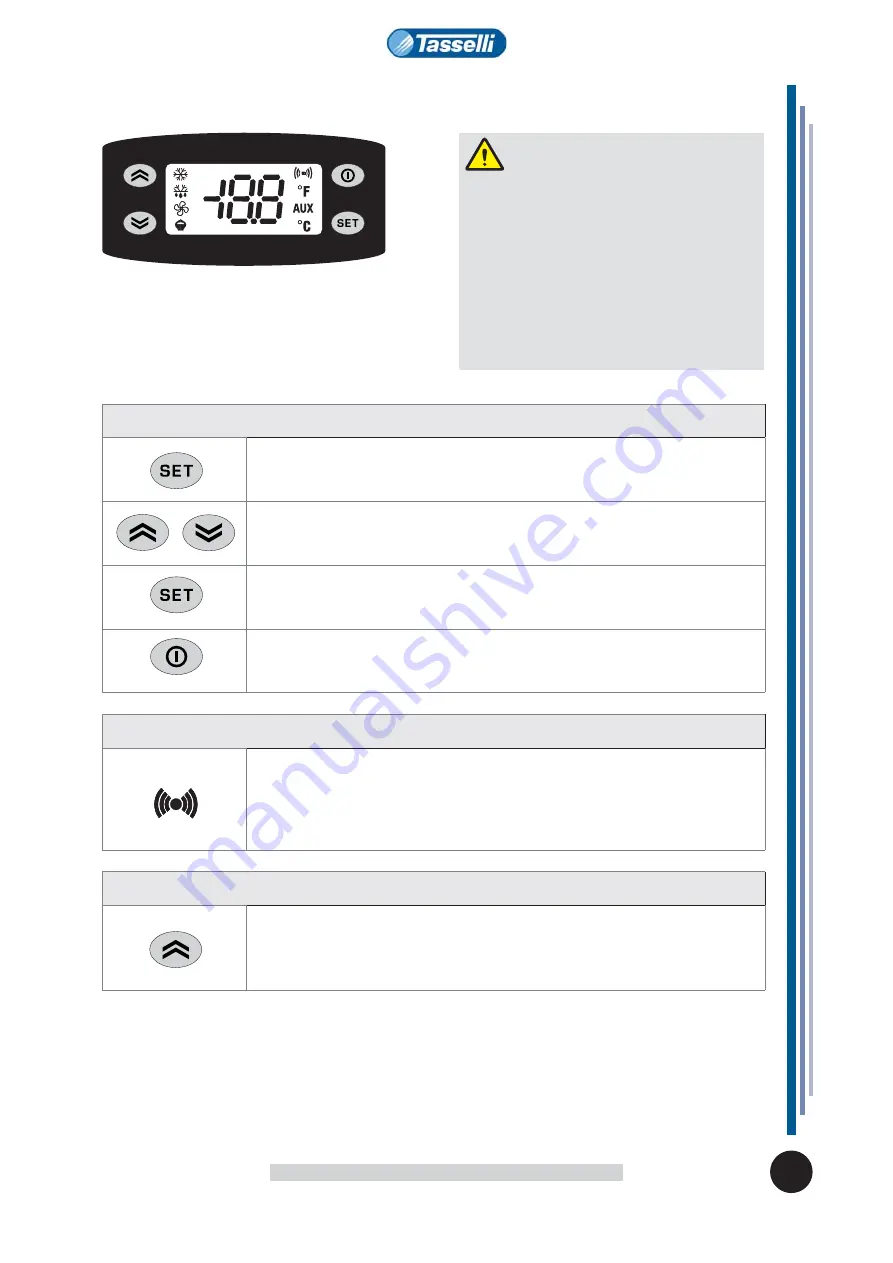
60
PANDA
USE AND MAINTENANCE MANUAL
428900224
237
EN
SETPOINT SETTING
Press the SET (ENTER) button and release immediately.
The “Set” label will appear.
To view the Set point value, press the SET (ENTER) button again.
The Set-point value will appear on the display.
To change the Set point value, press the UP and DOWN buttons within 15 seconds.
To confi rm the new Set-point value set, press the SET (ENTER) key again.
By not operating on the keyboard for more than 15 seconds (time-out) or pressing
the STAND-BY (ESC) key once, the last value displayed is confi rmed and you go
back to the previous display.
MANUAL ACTIVATION OF THE DEFROSTING CYCLE
To manually activate the defrosting cycle, press and hold the UP key for 5 seconds.
If defrosting conditions are not present (for instance the temperature of the evaporator
probe is higher than the temperature at the end of the defrosting process), the
display will fl ash three (3) times to indicate that the operation will not be performed.
Attachment 21 - CONTROL PANEL -
EW 978
- Sheet 2 of 3
Attention
The electronic control board is installed already
programmed.
Any changes to the control board settings can
be carried out exclusively by qualifi ed technical
personnel.
At start-up, the instrument conducts a LAMP
TEST for a few seconds. The display and LEDS
fl ash
to verify their integrity and to ensure they are
working correctly.
CHECK UP
Alarm conditions are always signalled by the buzzer (if present) and by the
corresponding alarm icon LED.
The alarm signal deriving from a faulty probe (probe 1) appears directly on the
instrument display with the indication E1.
The alarm signal deriving from a faulty evaporator probe (probe 2) appears directly
on the instrument display with the indication E2.
Summary of Contents for PANDA H205
Page 29: ...29 EN PANDA USE AND MAINTENANCE MANUAL 428900224237 Attachment 4 BRACKETS ...
Page 31: ...31 EN PANDA USE AND MAINTENANCE MANUAL 428900224237 Attachment 6 UNPACKING AND HANDLING ...
Page 32: ...32 PANDA USE AND MAINTENANCE MANUAL 428900224237 EN Attachment 7 BRACKETS ...
Page 33: ...33 EN PANDA USE AND MAINTENANCE MANUAL 428900224237 Attachment 8 MIRROR ...
Page 34: ...34 PANDA USE AND MAINTENANCE MANUAL 428900224237 EN Attachment 9 BASE BOARDS ...
Page 35: ...35 EN PANDA USE AND MAINTENANCE MANUAL 428900224237 Attachment 10 CHANGE IN SHELVES ...
Page 36: ...36 PANDA USE AND MAINTENANCE MANUAL 428900224237 EN Attachment 11 HOOKS ...
Page 37: ...37 EN PANDA USE AND MAINTENANCE MANUAL 428900224237 Attachment 12 SPACERS REAR ...
Page 67: ......
Page 68: ......