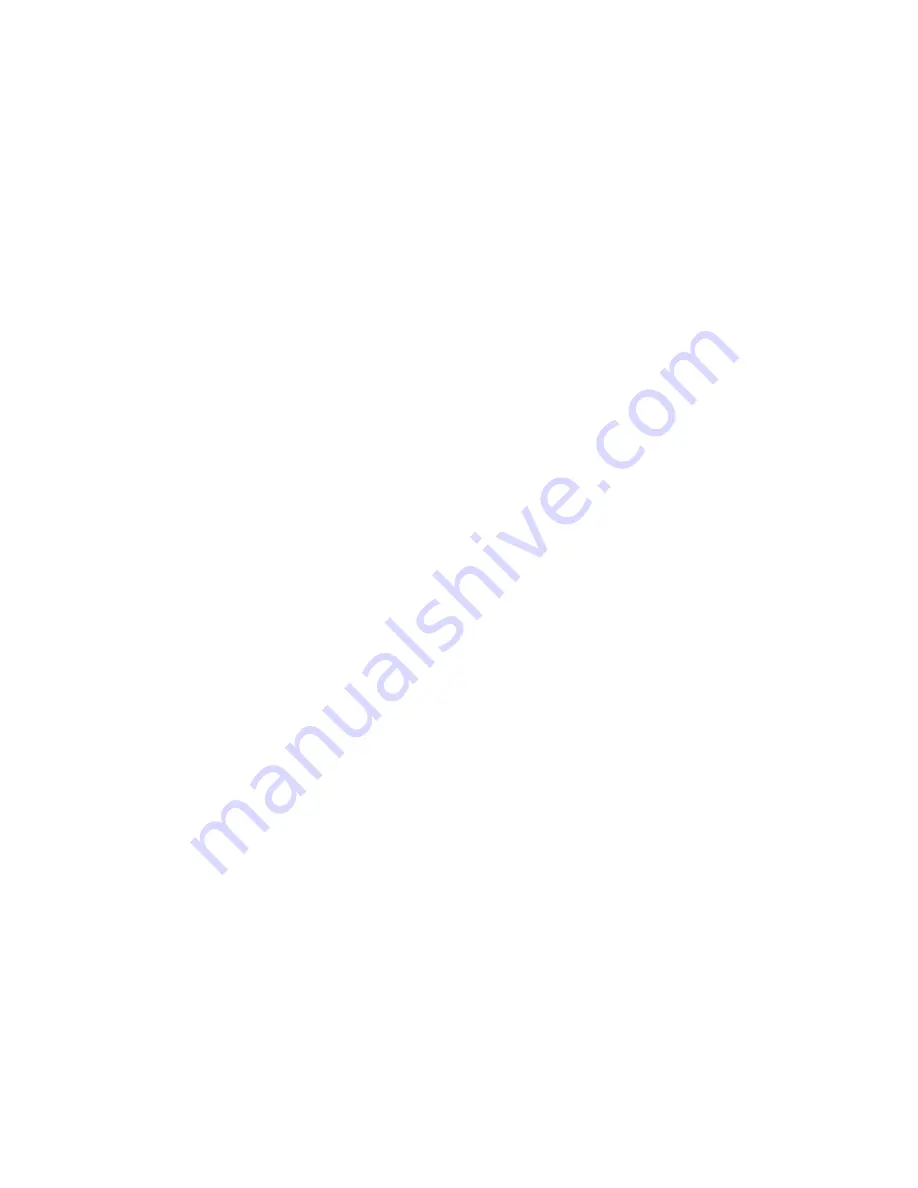
©Copyright Task Force Tips, Inc. 2016
LIA-212 December 8, 2016 Rev03
14
9.2 CRANKSHAFT OVERRIDE AND REPLACEMENT
The crankshaft includes an intentional shear joint to protect the gear train from overload, costly repairs, and loss of service. The
magnitude of torque required to shear the crankshaft is several times greater than the torque typically needed to operate the valve at
maximum operating pressure. If the crankshaft breaks during use, this is an indication that either there is something obstructing the
half ball internally or the crank shaft has been abused (e.g. used as a step for climbing).
9.2.1 CRANKSHAFT
OVERRIDE
In an emergency, the opposite side of the crankshaft can be turned using a 1/2” wrench or hex socket. This allows the valve to be
open or closed until the crankshaft is replaced. To prevent loss of the 1/8” square key on the crankshaft, do not allow the crankshaft
to slideout of gearbox until a replacement crankshaft is acquired. It is important not to rely on this as a long-term method of operation.
9.2.2 DIAGNOSIS
To diagnose the problem that caused the crankshaft to fail, complete the following steps:
1. Close upstream water supply. If possible, relieve pressure leading up to valve.
2. Locate 1/2” hex where crankshaft protrudes from opposite side of gearbox.
3. Gently turn crank shaft away from travel stop using a ½” hex wrench. Do not attempt to shock crankshaft free and do not
exceed 45 ft-lb (61 Nm) of torque.
4. If crankshaft will not rotate, then half ball is likely obstructed. Only after relieving pressure on fl anged joint, unbolt valve. Clear
any obstructions and evaluate whether repair is needed before returning to service.
5. If crankshaft is able to rotate, cycle the valve several times from open to closed to determine whether the crankshaft binds
at any place between the travel stops. If crankshaft binds, consult Task Force Tips Service Department to determine the
appropriate repairs.
6. If crankshaft rotates freely after clearing any obstructions, then a replacement crank shaft may be ordered from Task Force
Tips and replaced as described below.
9.2.3 CRANKSHAFT
REPLACEMENT
A broken crankshaft can be replaced at any time by completing the following steps, regardless of whether or not the upstream water
supply is pressurized. Referring to index numbers shown in section 6.3, follow the steps below:
1. Remove external retaining ring (index 13) adjacent to ½” hex on crank shaft. Do not over-expand the retaining ring.
2. Using a punch or Phillips head screwdriver at least 6” in length, gently push on dimple in ½” hex end of crankshaft (index 18).
Continue to push crankshaft through until it protrudes from opposite side of gearbox.
3. Grab broken end of crankshaft and pull out of gearbox. As crankshaft is withdrawn, grasp small key (index 17) on shaft so it
does not get lost.
4. If 1/8” square x 1” long key is not visible in shaft, it has likely fallen into gearbox bore and must be removed before installing
new crankshaft. If square key is visible in gearbox bore, slide it out of bore. Needle-nose pliers may be helpful depending on
position of key in bore.
5. Verify polymer bushings/thrust washers (index 16 and 14) are still seated in bores on each side of gearbox. If not, locate and
replace bushings.
6. Look through gearbox bore and note approximate orientation of square keyway in worm (index 15). Verify round notch in
polymer bushings/thrust washers (index 16) is aligned with square keyway in worm.
7. Prepare new crankshaft by applying small dab of grease to keyway and seating 1/8” square x 1” long key into keyway. Grease
will keep key in place during assembly.
8. Slide shaft into gearbox with key orientation the same as keyway in worm. Rotate shaft slightly in alternating directions until
key fi nds keyway, then push shaft in until it stops. Retaining ring groove and ½” hex should be protruding through opposite
side of gearbox. If hex is not visible, it may be necessary to slide polymer bushing back into gearbox bore.
9. Install retaining ring (index 13) onto shaft. Do not over-expand the retaining ring.