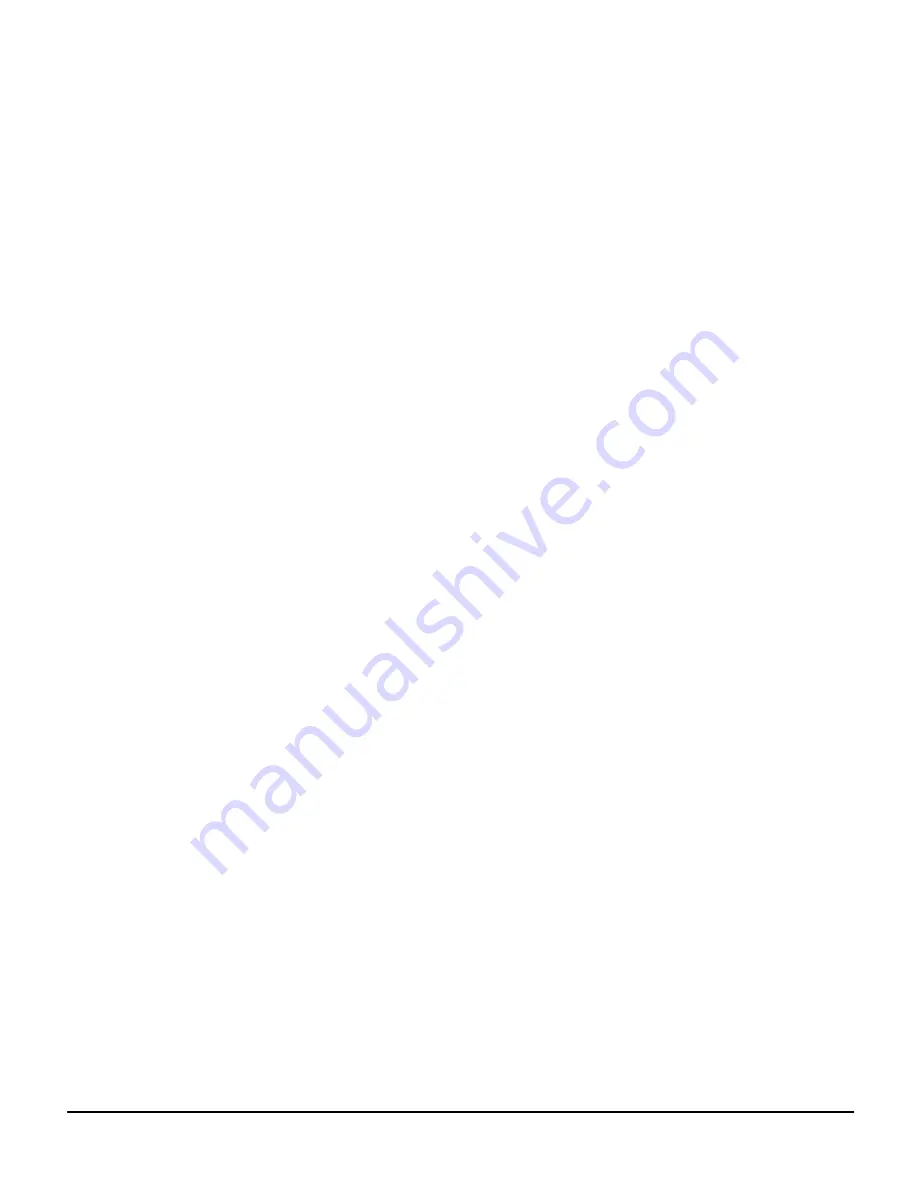
Release 7/2009 Ver. 1.0
Technical Manual: GS-120 Light Curtain Systems
TAPESWITCH CORPORATION
Phone: 631-630-0442
100 Schmitt Boulevard
35
Fax: 631-630-0454
Farmingdale, New York 11735
www.tapeswitch.com
4.0 INTERFACE AND AUXILIARY UNITS
4.1
GENERAL
In applications where the two PNP or solid state outputs
are not suitable for the machine control circuit, an
interface unit must be utilized. This interface unit may
be user supplied, provided it is compatible with either
the PNP or SSR outputs and has two channels. A
number of manufacturers produce units containing
circuits of this type. The interface unit must be designed
to the same level of integrity as the GS-120 in order to
maintain the same overall level of safety.
Several Tapeswitch interface units are available which
offer options in configuring the input power source,
mounting package and type of electrical interface
desired. All of the units perform the actual switching of
the electrical circuit of the dangerous machine using
positively-guided safety relays. All of the ac-powered
interface units (BSRSA and BSRUA-2) provide the
stepped-down +24 Vdc power for the GS-120 emitter
and receiver pair. The dc-powered interface units,
(SRUB and SRUS), are powered by an ex24
Vdc power supply and this supply
must also power the
GS-120 emitter and receiver pair.
All of the interface
units provide isolation from the low amperage GS-120
solid state outputs (0.5 A each) and the potentially
higher amperage required by the machine control
circuitry. Each interface unit provides LED status
indicators. All LEDs will be discussed in the description
of the applicable interface units. These units are
described in the appendices of this document.
4.1.1
METHODS OF INTERFACING
All of the interface units have a minimum of two safety
outputs.
These outputs are to be interfaced with the
machine primary control elements (MPCEs).
An
MPCE is defined as an electrically controlled element
which directly controls the normal operating motion of a
machine such that it is the last (in time) to operate when
motion is initiated or arrested.
The safety output contacts of the interface unit must be
connected to a machine’s MPCEs in such a way that if
either of the safety output relays is switched off, then the
machine will be brought to rest, regardless of the state
of the other relay.
This gives assurance that the failure of a single relay
cannot prevent the machine from being stopped. The
safety output relays are cross-monitored within the
interface unit. This means any disparity between the
two relays will be detected. The machine will be
disabled until the cause of the disparity has been
removed. Such a disparity could be the loss of signal on
one of the two channels coming from the light curtain.
The interface will only allow the safety relays to move to
the ON state if both channels are working correctly
together.
All interface units are provided with indicator lamps
which show the status of the interface. The number,
color, meaning and location of the indicators may
change with the type of interface. All interfaces
however, have indicators which specifically show the
commanded state of the output safety relays.
Both of these outputs must be used to take
advantage of the inherent redundancy of the
interface unit.
The two safety outputs are normally (NO). The outputs
are closed when no obstructions are in the light curtain
and no faults exist. Once the light curtain is broken the
outputs open. The state of the output may remain open
until a reset switch is applied (
MANUAL RESET
) or will
automatically close (
AUTOMATIC RESET
) once the
light curtain is cleared. Details of the resetting features
are discussed in the individual interface sections found
in the appendices.
The safety outputs can be used in several ways,
depending on the
MPCEs
found on the machine being
guarded.
MPCE
is the abbreviation for
Machine
Primary Control Element.
An
MPCE
is an electrically-
powered control device which directly controls the
guarded machines motion and is the final device in the
operating sequence when motion is either initiated or
halted. This would be the main hydraulic control valve
in a hydraulically controlled press. Some of the
common arrangements are described below:
• Normal risk machine - These usually have a single
MPCE. In this case both normally open safety outputs
should be used together as shown in
Figure 40
.
• High risk machines - These should have 2 MPCEs. In
some countries, it is customary for both MPCEs to
operate in the same mode. In this case, each of the
normally open (NO) outputs controls a single MPCE.
See
Figure 41
for an illustration of the type of
interface. Any additional output contacts can be used
as a monitor, e.g. as an input to a PLC.
To protect the contacts of the safety output relays from
the effects of switching inductive loads, an appropriately
rated power factor correction device must be installed
across the MPCE coils
. Figures 40 and 41
show Arc
Suppressors used for this purpose. Arc Suppressors
are user supplied.