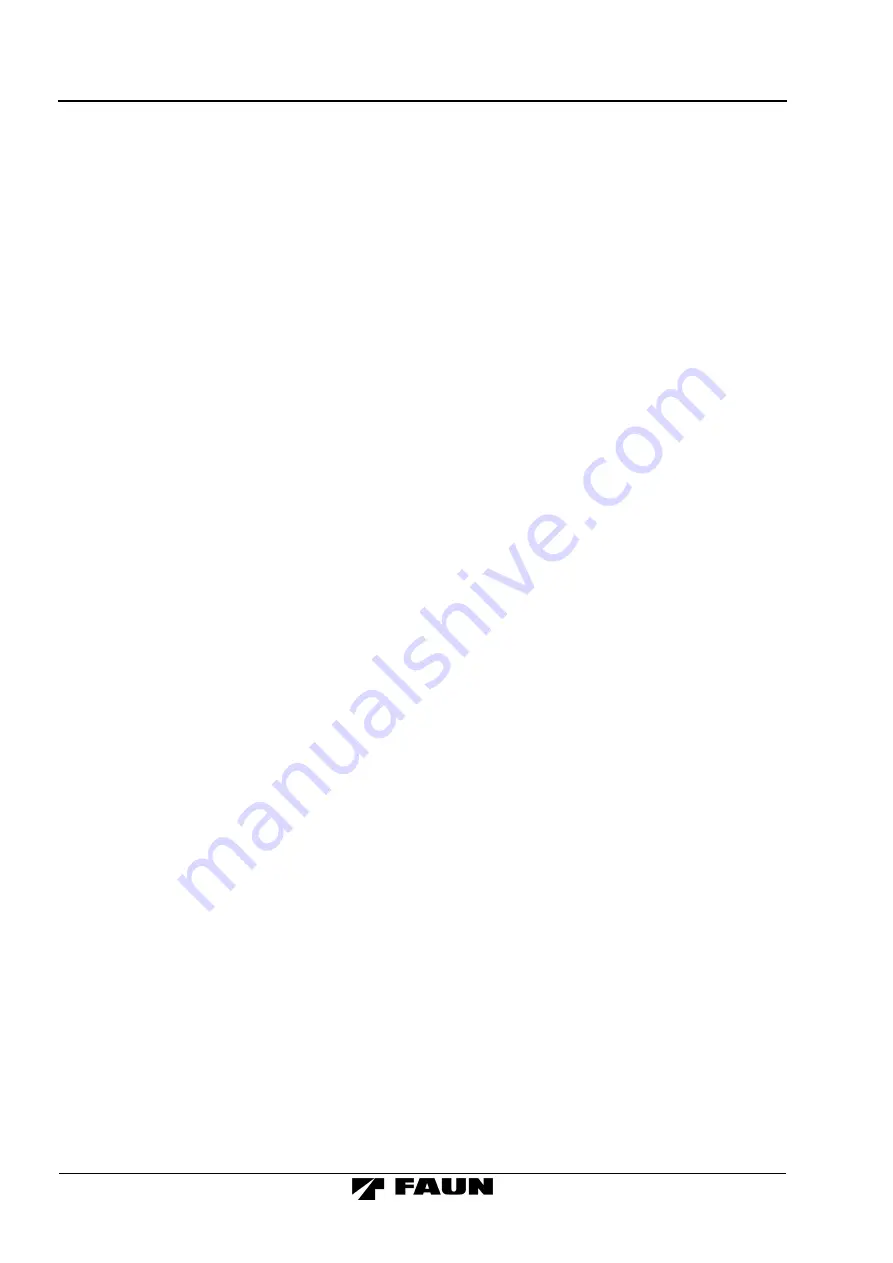
Work range
limit function
26/38
0710_EN_FA036_G2_01_01_00_AML
2003-01
(cont’d)
4.3 Display example
Function Summary
(1) Main function
<Work range>:
Activates the work range limit function. Moves item.
<Forward>:
Moves item.
<Back>:
Moves item backward.
<Set>:
Registration, cancellation of work range limit function, ends work range limit
registration and cancellation mode.
<Initial display>:
Exits work range limit registration and cancellation state.
(2) Limit symbols
Flashing:
Item is now selected.
On:
Item is not selected.
(3) LEDs
Off:
The work range function has been cancelled.
On:
The work range function is activated.
Flashing:
The work range function is activated and auto-stop control is being performed.
(4) Numerical Displays
Value turned on:
The work range function is registered.
Value flashing:
The work range function is cancelled and the current position value is
flashing.
‘---‘:
The work range function is cancelled and the item is not selected.
4.4
Saving the values for the work range limit function
The AML saves the registered work range limit function after power-off.
Summary of Contents for FAUN ATF 220G-5
Page 2: ......
Page 4: ......
Page 5: ...0015_EN_ALLGE_I_00_00_00 TABLE OF CONTENTS ...
Page 6: ......
Page 29: ...0025_EN_ALLGE_V_00_00_00 PREFACE ...
Page 30: ......
Page 32: ...V 1 How to use this Operating Manual 2 2 2002 12 0030_EN_FA036_V_01_00_00_FA029 Memo ...
Page 36: ...V 3 Handling of this Operating Manual 2 2 2002 12 0040_EN_FA036_V_03_00_00_FA029 Memo ...
Page 39: ...0050_EN_ALLGE_A_00_00_00 Part A Technical Details ...
Page 40: ......
Page 56: ...A 3 Technical details of components superstructure 8 8 0065_EN_FA036_A_03_00_00 2003 01 Memo ...
Page 58: ...A 4 Illustration of the vehicle 2 2 0070_EN_FA036_A_04_00_00 2001 06 Memo ...
Page 61: ...0080_EN_ALLGE_B0_00_00_00 Part B0 Safety Instructions ...
Page 62: ......
Page 90: ...B0 2 Instructions for the crane operator 24 24 0090_EN_FA036_B0_02_00_00_FA029 2003 01 Memo ...
Page 93: ...0100_EN_ALLGE_B_00_00_00 Part B Operating Instructions ...
Page 94: ......
Page 95: ...0105_EN_ALLGE_B1_00_00_00 Part B1 Operating Instructions Chassis ...
Page 96: ......
Page 111: ...Driver s cab B1 2 0115_EN_FA036_B1_02_01_00_FA029 2002 12 1 10 Memo ...
Page 113: ...Driver s cab B1 2 0115_EN_FA036_B1_02_01_00_FA029 2002 12 3 10 Driver s cab X ...
Page 114: ...B1 2 Driver s cab 4 10 0115_EN_FA036_B1_02_01_00_FA029 2001 06 Memo ...
Page 214: ...B1 7 Emergency control functions and elements 4 4 0145_EN_FA036_B1_07_00_00 2003 01 Memo ...
Page 218: ...B1 8 Operation in winter 4 4 0150_EN_FA036_B1_08_00_00_FA029 2003 01 Memo ...
Page 237: ...Instrument panel B1 11 0165_EN_FA036_B1_11_00_00_FA029 2002 12 1 4 Memo ...
Page 239: ...Instrument panel B1 11 0165_EN_FA036_B1_11_00_00_FA029 2002 12 3 4 Instrument panel ...
Page 240: ...B1 11 Instrument panel 4 4 0165_EN_FA036_B1_11_00_00_FA029 2002 12 Memo ...
Page 241: ...Instrument panel B1 11 0165_EN_FA036_B1_11_00_00_FA029_AB106 2002 12 1 4 Memo ...
Page 243: ...Instrument panel B1 11 0165_EN_FA036_B1_11_00_00_FA029_AB106 2002 12 3 4 Instrument panel ...
Page 244: ...B1 11 Instrument panel 4 4 0165_EN_FA036_B1_11_00_00_FA029_AB106 2002 12 Memo ...
Page 245: ...0170_EN_ALLGE_B2_00_00_00 Part B2 Operating Instructions Superstructure ...
Page 246: ......
Page 252: ...B2 1 General information about operation 6 8 0175_EN_FA036_B2_01_00_00 2001 06 Memo ...
Page 254: ...B2 1 General information about operation 8 8 0175_EN_FA036_B2_01_00_00 2003 01 Memo ...
Page 255: ...Crane cabin B2 2 0180_EN_FA036_B2_02_00_00 2003 01 1 10 Memo ...
Page 257: ...Crane cabin B2 2 0180_EN_FA036_B2_02_00_00 2003 01 3 10 Crane cabin X ...
Page 258: ...B2 2 Crane cabin 4 10 0180_EN_FA036_B2_02_00_00 2003 01 Memo ...
Page 338: ...B2 6 Crane movements in no load condition 36 36 0200_EN_FA036_B2_06_00_00 2003 01 Memo ...
Page 389: ...0230_EN_ALLGE_C_00_00_00 Part C Service and Maintenance ...
Page 390: ......
Page 394: ...C1 1 General information 4 4 0235_EN_FA036_C1_01_00_00_FA029 2001 06 Memo ...
Page 395: ...0240_EN_ALLGE_C_01_00_00 Part C1 Service and Maintenance Chassis ...
Page 396: ......
Page 398: ...C1 2 Maintenance intervals 2 16 0245_EN_FA036_C1_02_00_00_FA029 2003 01 Memo ...
Page 412: ...C1 2 Maintenance intervals 16 16 0245_EN_FA036_C1_02_00_00_FA029 2001 06 Memo ...
Page 434: ...C1 6 Axles 8 8 0265_EN_FA036_C1_06_00_00_FA029 2003 01 Memo ...
Page 436: ...C1 7 Propeller shafts 2 2 0270_EN_FA036_C1_07_00_00_FA029 2003 01 Memo ...
Page 472: ...C1 12 Electrical equipment 4 8 0295_EN_FA036_C1_12_00_00_FA029 2003 01 Memo ...
Page 480: ...C1 12 Electrical equipment 4 8 0295_EN_FA036_C1_12_00_00_FA029_AB106 2003 01 Memo ...
Page 490: ...C1 14 Outriggers 4 6 0305_EN_FA036_C1_14_00_00_FA029 2003 03 Memo ...
Page 491: ...Outriggers C1 14 0305_EN_FA036_C1_14_00_00_FA029 2002 12 5 6 cont d 14 Outriggers ...
Page 492: ...C1 14 Outriggers 6 6 0305_EN_FA036_C1_14_00_00_FA029 2002 12 cont d 14 Outriggers ...
Page 508: ...C1 27 Inspection scheme before start up daily 2 2 0335_EN_FA036_C1_27_00_00 2001 06 Memo ...
Page 510: ...C1 28 Inspection and cleaning scheme 2 2 0340_EN_FA036_C1_28_00_00 2001 06 Memo ...
Page 514: ...C1 30 Lubricating scheme 2 2 0350_EN_FA036_C1_30_00_00 2001 06 Memo ...
Page 515: ...0355_EN_ALLGE_C_02_00_00 Part C2 Service and Maintenance Superstructure ...
Page 516: ......
Page 518: ...C2 1 Maintenance intervals 2 12 0360_EN_FA036_C2_01_00_00 2003 01 Memo ...
Page 527: ...Maintenance intervals C2 1 0360_EN_FA036_C2_01_00_00 2003 01 11 12 Memo ...
Page 528: ...C2 1 Maintenance intervals 12 12 0360_EN_FA036_C2_01_00_00 2003 01 Memo ...
Page 538: ...C2 2 Engine 10 10 0365_EN_FA036_C2_02_00_00 2003 01 Memo ...
Page 558: ...C2 7 Electrical equipment 4 10 0390_EN_FA036_C2_07_00_00 2003 01 Memo ...
Page 563: ...Electrical equipment C2 7 0390_EN_FA036_C2_07_00_00 2003 01 9 10 Memo ...
Page 564: ...C2 7 Electrical equipment 10 10 0390_EN_FA036_C2_07_00_00 2003 01 Memo ...
Page 568: ...C2 8 Crane cab 4 4 0395_EN_FA036_C2_08_00_00_FA029 2003 01 Memo ...
Page 574: ...C2 15 Summary of oil types and filling capacities 2 2 0405_EN_FA036_C2_15_00_00 2003 03 Memo ...
Page 580: ...C2 18 Inspection scheme before start up daily 2 2 0420_EN_FA036_C2_18_00_00 2001 06 Memo ...
Page 582: ...C2 19 Inspection and cleaning scheme 2 2 0425_EN_FA036_C2_19_00_00 2001 06 Memo ...
Page 586: ...C2 21 Lubricating scheme 2 2 0435_EN_FA036_C2_21_00_00 2001 06 Memo ...
Page 587: ...0440_EN_ALLGE_D_00_00_00 Part D Circuit and piping diagrams ...
Page 588: ......
Page 597: ...0445_EN_ALLGE_D1_00_00_00 Part D1 Circuit and piping diagrams Chassis ...
Page 598: ......
Page 600: ...D1 1 Electric circuit diagrams 2 34 0450_EN_FA036_D1_01_00_00_FA029 2003 02 ...
Page 601: ...Electric circuit diagrams D1 1 0450_EN_FA036_D1_01_00_00_FA029 2003 02 3 34 ...
Page 602: ...D1 1 Electric circuit diagrams 4 34 0450_EN_FA036_D1_01_00_00_FA029 2003 02 ...
Page 603: ...Electric circuit diagrams D1 1 0450_EN_FA036_D1_01_00_00_FA029 2003 02 5 34 ...
Page 604: ...D1 1 Electric circuit diagrams 6 34 0450_EN_FA036_D1_01_00_00_FA029 2003 02 ...
Page 605: ...Electric circuit diagrams D1 1 0450_EN_FA036_D1_01_00_00_FA029 2003 02 7 34 ...
Page 606: ...D1 1 Electric circuit diagrams 8 34 0450_EN_FA036_D1_01_00_00_FA029 2003 02 ...
Page 607: ...Electric circuit diagrams D1 1 0450_EN_FA036_D1_01_00_00_FA029 2003 02 9 34 ...
Page 608: ...D1 1 Electric circuit diagrams 10 34 0450_EN_FA036_D1_01_00_00_FA029 2003 02 ...
Page 609: ...Electric circuit diagrams D1 1 0450_EN_FA036_D1_01_00_00_FA029 2003 02 11 34 ...
Page 612: ...D1 1 Electric circuit diagrams 14 34 0450_EN_FA036_D1_01_00_00_FA029 2003 02 ...
Page 614: ...D1 1 Electric circuit diagrams 16 34 0450_EN_FA036_D1_01_00_00_FA029 2003 02 ...
Page 615: ...Electric circuit diagrams D1 1 0450_EN_FA036_D1_01_00_00_FA029 2003 02 17 34 ...
Page 616: ...D1 1 Electric circuit diagrams 18 34 0450_EN_FA036_D1_01_00_00_FA029 2003 02 ...
Page 617: ...Electric circuit diagrams D1 1 0450_EN_FA036_D1_01_00_00_FA029 2003 02 19 34 ...
Page 618: ...D1 1 Electric circuit diagrams 20 34 0450_EN_FA036_D1_01_00_00_FA029 2003 02 ...
Page 619: ...Electric circuit diagrams D1 1 0450_EN_FA036_D1_01_00_00_FA029 2003 02 21 34 ...
Page 620: ...D1 1 Electric circuit diagrams 22 34 0450_EN_FA036_D1_01_00_00_FA029 2003 02 ...
Page 621: ...Electric circuit diagrams D1 1 0450_EN_FA036_D1_01_00_00_FA029 2003 02 23 34 ...
Page 622: ...D1 1 Electric circuit diagrams 24 34 0450_EN_FA036_D1_01_00_00_FA029 2003 02 ...
Page 623: ...Electric circuit diagrams D1 1 0450_EN_FA036_D1_01_00_00_FA029 2003 02 25 34 ...
Page 624: ...D1 1 Electric circuit diagrams 26 34 0450_EN_FA036_D1_01_00_00_FA029 2003 02 ...
Page 625: ...Electric circuit diagrams D1 1 0450_EN_FA036_D1_01_00_00_FA029 2003 02 27 34 ...
Page 634: ...D1 1 Electric circuit diagrams 2 34 0450_EN_FA036_D1_01_00_00_FA029_AB104 2003 02 ...
Page 635: ...Electric circuit diagrams D1 1 0450_EN_FA036_D1_01_00_00_FA029_AB104 2003 02 3 34 ...
Page 636: ...D1 1 Electric circuit diagrams 4 34 0450_EN_FA036_D1_01_00_00_FA029_AB104 2003 02 ...
Page 637: ...Electric circuit diagrams D1 1 0450_EN_FA036_D1_01_00_00_FA029_AB104 2003 02 5 34 ...
Page 638: ...D1 1 Electric circuit diagrams 6 34 0450_EN_FA036_D1_01_00_00_FA029_AB104 2003 02 ...
Page 639: ...Electric circuit diagrams D1 1 0450_EN_FA036_D1_01_00_00_FA029_AB104 2003 02 7 34 ...
Page 640: ...D1 1 Electric circuit diagrams 8 34 0450_EN_FA036_D1_01_00_00_FA029_AB104 2003 02 ...
Page 641: ...Electric circuit diagrams D1 1 0450_EN_FA036_D1_01_00_00_FA029_AB104 2003 02 9 34 ...
Page 642: ...D1 1 Electric circuit diagrams 10 34 0450_EN_FA036_D1_01_00_00_FA029_AB104 2003 02 ...
Page 643: ...Electric circuit diagrams D1 1 0450_EN_FA036_D1_01_00_00_FA029_AB104 2003 02 11 34 ...
Page 646: ...D1 1 Electric circuit diagrams 14 34 0450_EN_FA036_D1_01_00_00_FA029_AB104 2003 02 ...
Page 648: ...D1 1 Electric circuit diagrams 16 34 0450_EN_FA036_D1_01_00_00_FA029_AB104 2003 02 ...
Page 649: ...Electric circuit diagrams D1 1 0450_EN_FA036_D1_01_00_00_FA029_AB104 2003 02 17 34 ...
Page 650: ...D1 1 Electric circuit diagrams 18 34 0450_EN_FA036_D1_01_00_00_FA029_AB104 2003 02 ...
Page 651: ...Electric circuit diagrams D1 1 0450_EN_FA036_D1_01_00_00_FA029_AB104 2003 02 19 34 ...
Page 652: ...D1 1 Electric circuit diagrams 20 34 0450_EN_FA036_D1_01_00_00_FA029_AB104 2003 02 ...
Page 653: ...Electric circuit diagrams D1 1 0450_EN_FA036_D1_01_00_00_FA029_AB104 2003 02 21 34 ...
Page 654: ...D1 1 Electric circuit diagrams 22 34 0450_EN_FA036_D1_01_00_00_FA029_AB104 2003 02 ...
Page 655: ...Electric circuit diagrams D1 1 0450_EN_FA036_D1_01_00_00_FA029_AB104 2003 02 23 34 ...
Page 656: ...D1 1 Electric circuit diagrams 24 34 0450_EN_FA036_D1_01_00_00_FA029_AB104 2003 02 ...
Page 657: ...Electric circuit diagrams D1 1 0450_EN_FA036_D1_01_00_00_FA029_AB104 2003 02 25 34 ...
Page 658: ...D1 1 Electric circuit diagrams 26 34 0450_EN_FA036_D1_01_00_00_FA029_AB104 2003 02 ...
Page 659: ...Electric circuit diagrams D1 1 0450_EN_FA036_D1_01_00_00_FA029_AB104 2003 02 27 34 ...
Page 668: ...D1 1 Electric circuit diagrams 2 34 0450_EN_FA036_D1_01_00_00_FA029_AB106 2003 02 ...
Page 669: ...Electric circuit diagrams D1 1 0450_EN_FA036_D1_01_00_00_FA029_AB106 2003 02 3 34 ...
Page 670: ...D1 1 Electric circuit diagrams 4 34 0450_EN_FA036_D1_01_00_00_FA029_AB106 2003 02 ...
Page 671: ...Electric circuit diagrams D1 1 0450_EN_FA036_D1_01_00_00_FA029_AB106 2003 02 5 34 ...
Page 672: ...D1 1 Electric circuit diagrams 6 34 0450_EN_FA036_D1_01_00_00_FA029_AB106 2003 02 ...
Page 673: ...Electric circuit diagrams D1 1 0450_EN_FA036_D1_01_00_00_FA029_AB106 2003 02 7 34 ...
Page 674: ...D1 1 Electric circuit diagrams 8 34 0450_EN_FA036_D1_01_00_00_FA029_AB106 2003 02 ...
Page 675: ...Electric circuit diagrams D1 1 0450_EN_FA036_D1_01_00_00_FA029_AB106 2003 02 9 34 ...
Page 676: ...D1 1 Electric circuit diagrams 10 34 0450_EN_FA036_D1_01_00_00_FA029_AB106 2003 02 ...
Page 677: ...Electric circuit diagrams D1 1 0450_EN_FA036_D1_01_00_00_FA029_AB106 2003 02 11 34 ...
Page 680: ...D1 1 Electric circuit diagrams 14 34 0450_EN_FA036_D1_01_00_00_FA029_AB106 2003 02 ...
Page 682: ...D1 1 Electric circuit diagrams 16 34 0450_EN_FA036_D1_01_00_00_FA029_AB106 2003 02 ...
Page 683: ...Electric circuit diagrams D1 1 0450_EN_FA036_D1_01_00_00_FA029_AB106 2003 02 17 34 ...
Page 684: ...D1 1 Electric circuit diagrams 18 34 0450_EN_FA036_D1_01_00_00_FA029_AB106 2003 02 ...
Page 685: ...Electric circuit diagrams D1 1 0450_EN_FA036_D1_01_00_00_FA029_AB106 2003 02 19 34 ...
Page 686: ...D1 1 Electric circuit diagrams 20 34 0450_EN_FA036_D1_01_00_00_FA029_AB106 2003 02 ...
Page 687: ...Electric circuit diagrams D1 1 0450_EN_FA036_D1_01_00_00_FA029_AB106 2003 02 21 34 ...
Page 688: ...D1 1 Electric circuit diagrams 22 34 0450_EN_FA036_D1_01_00_00_FA029_AB106 2003 02 ...
Page 689: ...Electric circuit diagrams D1 1 0450_EN_FA036_D1_01_00_00_FA029_AB106 2003 02 23 34 ...
Page 690: ...D1 1 Electric circuit diagrams 24 34 0450_EN_FA036_D1_01_00_00_FA029_AB106 2003 02 ...
Page 691: ...Electric circuit diagrams D1 1 0450_EN_FA036_D1_01_00_00_FA029_AB106 2003 02 25 34 ...
Page 692: ...D1 1 Electric circuit diagrams 26 34 0450_EN_FA036_D1_01_00_00_FA029_AB106 2003 02 ...
Page 693: ...Electric circuit diagrams D1 1 0450_EN_FA036_D1_01_00_00_FA029_AB106 2003 02 27 34 ...
Page 704: ...D1 3 Hydraulic piping diagrams 2 14 0460_EN_FA036_D1_03_00_00 2003 02 Memo ...
Page 705: ...Hydraulic piping diagrams D1 3 0460_EN_FA036_D1_03_00_00 2003 02 3 14 ...
Page 706: ...D1 3 Hydraulic piping diagrams 4 14 0460_EN_FA036_D1_03_00_00 2003 02 Memo ...
Page 707: ...Hydraulic piping diagrams D1 3 0460_EN_FA036_D1_03_00_00 2003 02 5 14 ...
Page 709: ...Hydraulic piping diagrams D1 3 0460_EN_FA036_D1_03_00_00 2003 02 7 14 Memo ...
Page 710: ...D1 3 Hydraulic piping diagrams 8 14 0460_EN_FA036_D1_03_00_00 2003 02 ...
Page 715: ...Hydraulic piping diagrams D1 3 0460_EN_FA036_D1_03_00_00 2003 02 13 14 3 7 Motor 99707783371 ...
Page 718: ...D1 3 Hydraulic piping diagrams 2 14 0460_EN_FA036_D1_03_00_00_AB104 2003 02 Memo ...
Page 719: ...Hydraulic piping diagrams D1 3 0460_EN_FA036_D1_03_00_00_AB104 2003 02 3 14 ...
Page 720: ...D1 3 Hydraulic piping diagrams 4 14 0460_EN_FA036_D1_03_00_00_AB104 2003 02 Memo ...
Page 721: ...Hydraulic piping diagrams D1 3 0460_EN_FA036_D1_03_00_00_AB104 2003 02 5 14 ...
Page 723: ...Hydraulic piping diagrams D1 3 0460_EN_FA036_D1_03_00_00_AB104 2003 02 7 14 Memo ...
Page 724: ...D1 3 Hydraulic piping diagrams 8 14 0460_EN_FA036_D1_03_00_00_AB104 2003 02 ...
Page 731: ...0465_EN_ALLGE_D2_00_00_00 Part D2 Circuit and piping diagrams Superstructure ...
Page 732: ......
Page 734: ...D2 1 Electric circuit diagrams 2 42 0470_EN_FA036_D2_01_00_00 2003 02 ...
Page 735: ...Electric circuit diagrams D2 1 0470_EN_FA036_D2_01_00_00 2003 02 3 42 ...
Page 736: ...D2 1 Electric circuit diagrams 4 42 0470_EN_FA036_D2_01_00_00 2003 02 ...
Page 738: ......
Page 739: ...Electric circuit diagrams D2 1 0470_EN_FA036_D2_01_00_00 2003 02 7 42 ...
Page 740: ...D2 1 Electric circuit diagrams 8 42 0470_EN_FA036_D2_01_00_00 2003 02 ...
Page 741: ...Electric circuit diagrams D2 1 0470_EN_FA036_D2_01_00_00 2003 02 9 42 ...
Page 742: ...D2 1 Electric circuit diagrams 10 42 0470_EN_FA036_D2_01_00_00 2003 02 ...
Page 743: ...Electric circuit diagrams D2 1 0470_EN_FA036_D2_01_00_00 2003 02 11 42 ...
Page 744: ...D2 1 Electric circuit diagrams 12 42 0470_EN_FA036_D2_01_00_00 2003 02 ...
Page 745: ...Electric circuit diagrams D2 1 0470_EN_FA036_D2_01_00_00 2003 02 13 42 ...
Page 746: ...D2 1 Electric circuit diagrams 14 42 0470_EN_FA036_D2_01_00_00 2003 02 ...
Page 747: ...Electric circuit diagrams D2 1 0470_EN_FA036_D2_01_00_00 2003 02 15 42 ...
Page 748: ...D2 1 Electric circuit diagrams 16 42 0470_EN_FA036_D2_01_00_00 2003 02 1 3 AML 99707792040 ...
Page 750: ...D2 1 Electric circuit diagrams 18 42 0470_EN_FA036_D2_01_00_00 2003 02 ...
Page 751: ...Electric circuit diagrams D2 1 0470_EN_FA036_D2_01_00_00 2003 02 19 42 ...
Page 752: ...D2 1 Electric circuit diagrams 20 42 0470_EN_FA036_D2_01_00_00 2003 02 ...
Page 753: ...Electric circuit diagrams D2 1 0470_EN_FA036_D2_01_00_00 2003 02 21 42 ...
Page 754: ...D2 1 Electric circuit diagrams 22 42 0470_EN_FA036_D2_01_00_00 2003 02 ...
Page 755: ...Electric circuit diagrams D2 1 0470_EN_FA036_D2_01_00_00 2003 02 23 42 ...
Page 756: ......
Page 757: ...Electric circuit diagrams D2 1 0470_EN_FA036_D2_01_00_00 2003 02 25 42 ...
Page 758: ...D2 1 Electric circuit diagrams 26 42 0470_EN_FA036_D2_01_00_00 2003 02 ...
Page 759: ......
Page 760: ......
Page 761: ......
Page 763: ...Electric circuit diagrams D2 1 0470_EN_FA036_D2_01_00_00 2003 02 31 42 ...
Page 764: ...D2 1 Electric circuit diagrams 32 42 0470_EN_FA036_D2_01_00_00 2003 02 ...
Page 765: ......
Page 766: ...D2 1 Electric circuit diagrams 34 42 0470_EN_FA036_D2_01_00_00 2003 02 1 9 AML 99707792040 ...
Page 767: ...Electric circuit diagrams D2 1 0470_EN_FA036_D2_01_00_00 2003 02 35 42 1 10 Jib 99707792040 ...
Page 776: ...D2 3 Hydraulic piping diagrams 2 6 0475_EN_FA036_D2_03_00_00 2003 02 Memo ...
Page 777: ...Hydraulic piping diagrams D2 3 0475_EN_FA036_D2_03_00_00 2003 02 3 6 ...
Page 778: ...D2 3 Hydraulic piping diagrams 4 6 0475_EN_FA036_D2_03_00_00 2003 02 Memo ...
Page 779: ...Hydraulic piping diagrams D2 3 0475_EN_FA036_D2_03_00_00 2003 02 5 6 ...
Page 781: ...0480_EN_ALLGE_E_00_00_00 Part E Crane testing instructions ...
Page 782: ......
Page 792: ...E 1 Inspection of supporting steel structures 10 10 0490_EN_FA036_E1_01_01_00 2001 06 Memo ...
Page 794: ...E 2 Inspection of the hook blocks 2 2 0495_EN_FA036_E2_00_00_00_FA029 2003 01 Memo ...
Page 814: ...E 5 Monitoring the slewing device 2 2 0510_EN_FA036_E5_00_00_00_FA029 2003 01 Memo ...
Page 815: ...0515_EN_ALLGE_F_00_00_00 Part F Troubleshooting ...
Page 816: ......
Page 817: ...0520_EN_ALLGE_F1_00_00_00 Part F1 Troubleshooting Chassis ...
Page 818: ......
Page 820: ...F1 0 Troubleshooting in the chassis 2 2 0525_EN_FA036_F1_00_00_00_FA029 2003 01 Memo ...
Page 824: ...F1 2 Gearbox 2 2 0535_EN_FA036_F1_02_00_00_FA029 2003 01 Memo ...
Page 826: ...F1 3 Transfer box 2 2 0540_EN_FA036_F1_03_00_00_FA029 2003 01 Memo ...
Page 840: ...F1 7 Electrical equipment 2 2 0560_EN_FA036_F1_07_00_00_FA029 2003 01 Memo ...
Page 842: ...F1 8 Eddy current brake 2 2 0565_EN_FA036_F1_08_00_00_FA029 2003 01 Memo ...
Page 843: ...0570_EN_ALLGE_F2_00_00_00 Part F2 Troubleshooting Superstructure ...
Page 844: ......
Page 846: ...F2 0 Troubleshooting 2 2 0575_EN_FA036_F2_00_00_00_FA029 2003 01 Memo ...
Page 848: ...F2 1 Engine 2 2 0580_EN_FA036_F2_01_00_00_FA029 2003 01 Memo ...
Page 852: ...F2 3 Slewing gear 2 2 0590_EN_FA036_F2_03_00_00_FA029 2003 01 Memo ...
Page 854: ...F2 4 Telescoping mechanism 2 2 0595_EN_FA036_F2_04_00_00_FA029 2003 01 Memo ...
Page 856: ...F2 5 Boom elevation 2 2 0600_EN_FA036_F2_05_00_00_FA029 2003 01 Memo ...
Page 858: ...F2 6 Hoisting gear 2 2 0605_EN_FA036_F2_06_00_00_FA029 2003 01 Memo ...
Page 860: ...F2 7 Counterweight 2 2 0610_EN_FA036_F2_07_00_00 2003 01 Memo ...
Page 862: ...F2 8 Electrical equipment 2 2 0615_EN_FA036_F2_08_00_00_FA029 2003 01 Memo ...
Page 863: ...0630_EN_ALLGE_F4_00_00_00 Part F4 Connection diagram Chassis ...
Page 864: ......
Page 869: ...0640_EN_ALLGE_G_00_00_00 Part G Annex ...
Page 870: ......
Page 871: ...0645_EN_ALLGE_G1_00_00_00 Part G1 Annex Chassis ...
Page 872: ......
Page 873: ...0650_EN_ALLGE_G1_01_00_00 Operating instructions for ZF gearbox ...
Page 874: ......
Page 875: ...12AS 2301 16AS 2601 ZF Standard 1328 758 104 ...
Page 881: ...16 AS 2601 with Intarder 1 1 013165 ...
Page 904: ......
Page 910: ......
Page 914: ...0660_EN_ALLGE_G1_02_00_00 Operating instructions for ZF Intarder ...
Page 915: ......
Page 955: ...0670_EN_ALLGE_G1_03_00_00 Chart of lubricants for ZF gearbox ...
Page 956: ......
Page 974: ...0680_EN_ALLGE_G1_04_00_00 Centralized lubrication system ...
Page 975: ......
Page 977: ...G1 4 Overview of lubricating points 2 2 0685_EN_FA029_G1_04_00_00_SCHMIERSUEBERS 2003 01 Memo ...
Page 990: ...0695_EN_ALLGE_G2_00_00_00 Part G2 Annex Superstructure ...
Page 991: ......
Page 992: ...0700_EN_ALLGE_G2_01_00_00 Load Moment Limiter AML ...
Page 993: ......
Page 995: ...G2 1 AML 2 2 0705_EN_FA036_G2_01_00_00_FA029 2003 01 Memo ...
Page 1033: ...Counterweight status 38 38 0710_EN_FA036_G2_01_01_00_AML 2003 01 Memo ...
Page 1048: ...0720_EN_ALLGE_G2_02_00_00 Centralized lubrication system ...
Page 1049: ......
Page 1065: ......
Page 1078: ......