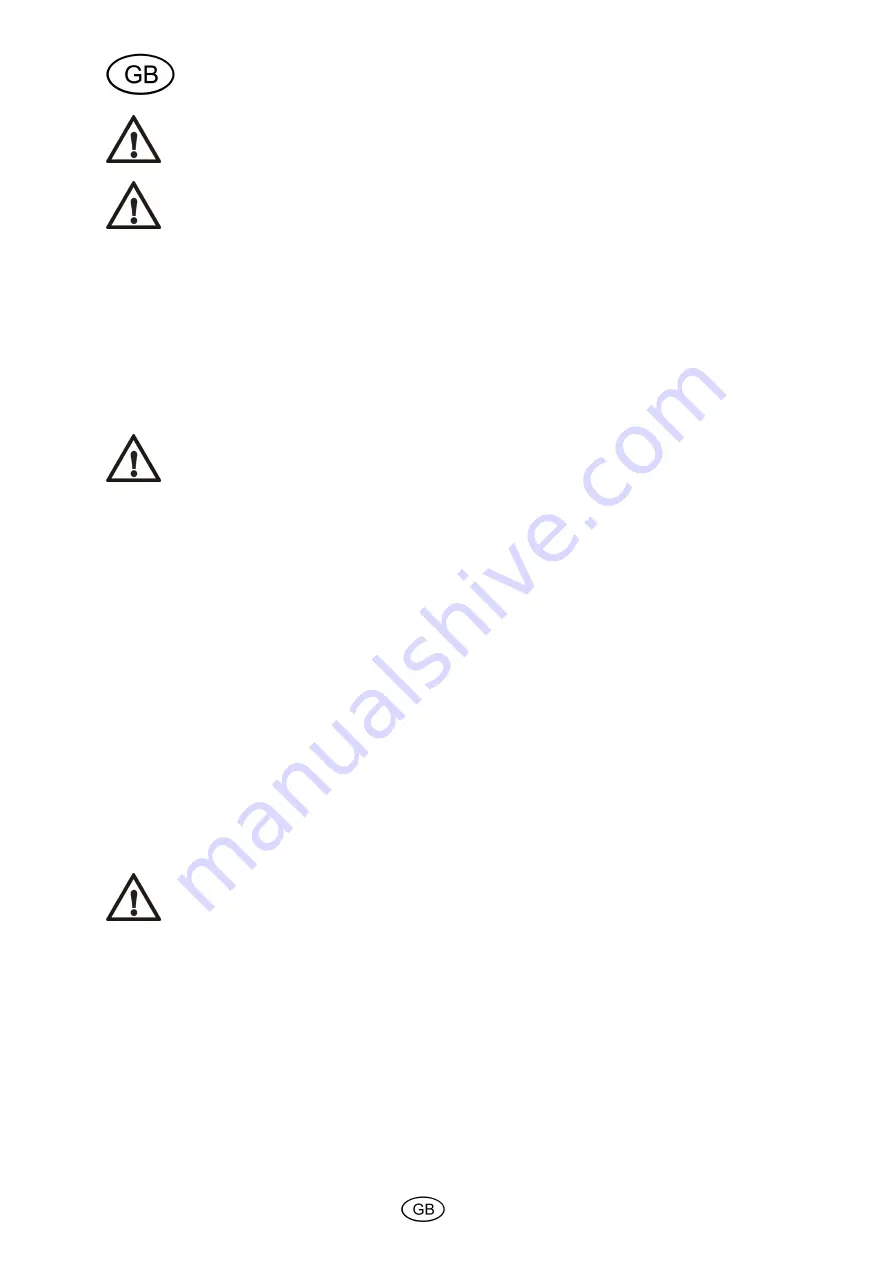
The pump should be installed in a dry place with an ambient temperature not to exceed 40 °C
and not to fall below 5 °C. The pump and the entire connection system have to be protected
from frost and other climatic influences.
When installing the device, please make sure that the motor is sufficiently ventilated.
All connection lines have to be perfectly tight since leaking lines may affect the performance of the pump and
cause considerable damage. Therefore, please use Teflon tape to seal the contact surfaces between the
threaded sections of the lines and the connection with the pump. This use of sealing material such as Teflon tape
is the only way to ensure an airtight assembly.
When tightening threaded connections, please do not apply excessive force which may cause damage.
When laying the connection pipes, you should make sure that the pump is not exposed to any form of weight,
vibration or tension. Moreover, the connection lines must not contain any kinks or an adverse slope.
Please observe the illustrations, too, which are contained as an attachment at the end of the present operating
instructions. The numeric and other details included in brackets below refer to these illustrations.
5.2.
Installation of the suction line
The intake of the suction line has to be equipped with a check valve (or non-return valve) and
an intake filter.
Please use a suction line (2) having the same diameter as the suction port (1) of the pump. If the suction height
(HA) exceeds 4 m, however, it is recommendable to use a 25% larger diameter - including appropriate reducer
elements for the connectors.
The intake of the suction line has to be equipped with a check valve (3) - or non-return valve - and an intake filter
(4). The filter will keep away larger dirt particles contained in the water which might clog or even damage the
piping. The check valve will prevent the pressure to escape after the pump has cut out. Moreover, it simplifies the
venting of the suction line by enabling water to be filled in. The check valve with the intake filter - i.e. the entirety
of the intake section of the suction port - must be immersed by at least 0.3 m below the surface of the liquid to be
pumped (HI). This will prevent air from being taken in. In addition, please ensure a sufficient distance of the
suction line from both the ground and the sides of water courses, rivers, ponds etc in order to prevent stones,
plants etc from being sucked in.
5.3.
Installation of the pressure line
The pressure line (11) conveys the liquids to be discharged from the pump to the point of withdrawal. To avoid
dynamic flow losses, one should use a pressure line having at least the same diameter as the pressure port (5) of
the pump. To protect the pump from damage caused by pressure surges it is advisable to equip the pressure line
with a check valve (6) to be installed directly downstream the pump outlet.
Also, to facilitate maintenance work, it is recommendable to install a shut-off cock (7) after the pump and check
valve. This is a useful feature since it can be closed when the pump has to be dismantled and will thus prevent
the pressure line from draining to empty.
5.4. Stationary
installation
With regard to the electrical connection in the case of stationary installation, please ensure an
adequate visibility and accessibility of the plug.
For stationary installation, please fasten the pump on a suitable, solid surface. To reduce vibration, it is
recommended to apply an anti-vibration material - for instance a rubble layer - between the pump and the
installation surface.
Efficient vibration dampeners are available from T.I.P. as an accessory with the item number 30943.
To begin, pre-drill four holes.
Please use the support feet (18) as a template for marking the bore holes. Place the unit in the desired position,
then lead a centre punch or a pencil through the openings in the support feed to mark the position of the bore
holes.
Put the device aside, then use a suitable drill for pre-drilling the four holes. Place the device back into the desired
position, then fasten it there using suitable screws and washers.
3
11
Summary of Contents for HWW 1300/25 Plus
Page 52: ...T I P 1 1 2 2 3 2 4 2 5 3 6 4 7 4 8 6 9 6 10 T I P 6 11 7 12 8 13 9 14 9 1 8 1 49...
Page 54: ...T I P 5 5 1 40 C 5 C Teflon Teflon 5 2 2 1 HA 4 m 25 3 4 0 3 m HI 5 3 11 5 6 7 3 51...
Page 56: ...8 8 9 2 T I P HWW 7 230V AC T I P HWW 5 53...
Page 58: ...11 12 1 5 bar 70343 service 1 any liquid the motor is not running 1 2 3 4 5 1 GS 2 3 4 5 7 55...
Page 60: ...1 2 3 13 www tip pumpen de 14 2002 96 EC 9 57...
Page 93: ...T I P 1 1 2 1 3 2 4 2 5 3 6 4 7 4 8 5 9 6 10 T I P 6 11 6 12 8 13 9 14 9 1 8 2 T I P 1 90...
Page 95: ...5 5 1 40 C 5 C 5 2 2 1 HA 4 25 l 3 4 0 3 HI 5 3 11 5 6 7 5 4 3 92...
Page 97: ...8 8 9 2 T I P HWW 7 230 V T I P HWW 8 8 1 T I P T I P HWW TLS 8 2 60 70 C 5 94...
Page 99: ...1 1 2 3 4 5 1 GS 2 3 4 5 2 1 2 3 1 2 a 3 3 1 2 3 4 5 1 GS 2 3 4 5 7 96...
Page 100: ...4 1 2 3 4 1 2 1 5 bar 3 2 2 4 5 1 2 1 2 2 2 6 1 2 1 2 2 2 12 vis major a 1 2 3 8 97...
Page 101: ...13 www tip pumpen de 14 EU EU 2002 96 EK 9 98...
Page 133: ...T I P 1 1 2 1 3 2 4 3 5 3 6 4 7 4 8 5 9 6 10 T I P 6 11 6 12 8 13 9 14 9 1 8 2 T I P 1 130...
Page 135: ...4 T I P 5 5 1 40 C 5 C 5 2 2 1 HA 4 25 3 4 0 3 HI 5 3 11 5 6 3 132...
Page 137: ...8 9 8 2 T I P HWW 7 230 T I P HWW 8 8 1 T I P T I P HWW TLS 5 134...
Page 139: ...12 1 5 T I P 30905 1 1 2 3 4 5 1 2 3 4 5 2 1 2 3 1 2 a b c d 3 3 1 2 3 4 5 1 2 3 4 5 7 136...
Page 140: ...4 1 2 3 4 1 2 1 5 3 2 2 4 5 1 2 1 2 2 2 6 1 2 1 2 2 2 12 1 2 3 8 137...
Page 141: ...13 www tip pumpen de 14 2002 96 E 9 138...
Page 142: ...T I P 1 1 2 1 3 2 4 2 5 3 6 4 7 4 8 5 9 6 10 T I P 6 11 6 12 7 13 8 14 8 1 8 2 T I P 1 139...
Page 144: ...5 5 1 5 C 40 C 5 2 2 1 HA 4 25 3 4 0 3 HI 5 3 11 5 6 7 5 4 T I P 30943 3 141...
Page 147: ...9 T I P HWW 2 3 10 T I P T I P T I P G5 31052 G7 31058 G10 31050 11 12 1 5 T I P 30905 6 144...
Page 149: ...1 2 3 13 www tip pumpen de 14 2002 96 E 8 146...