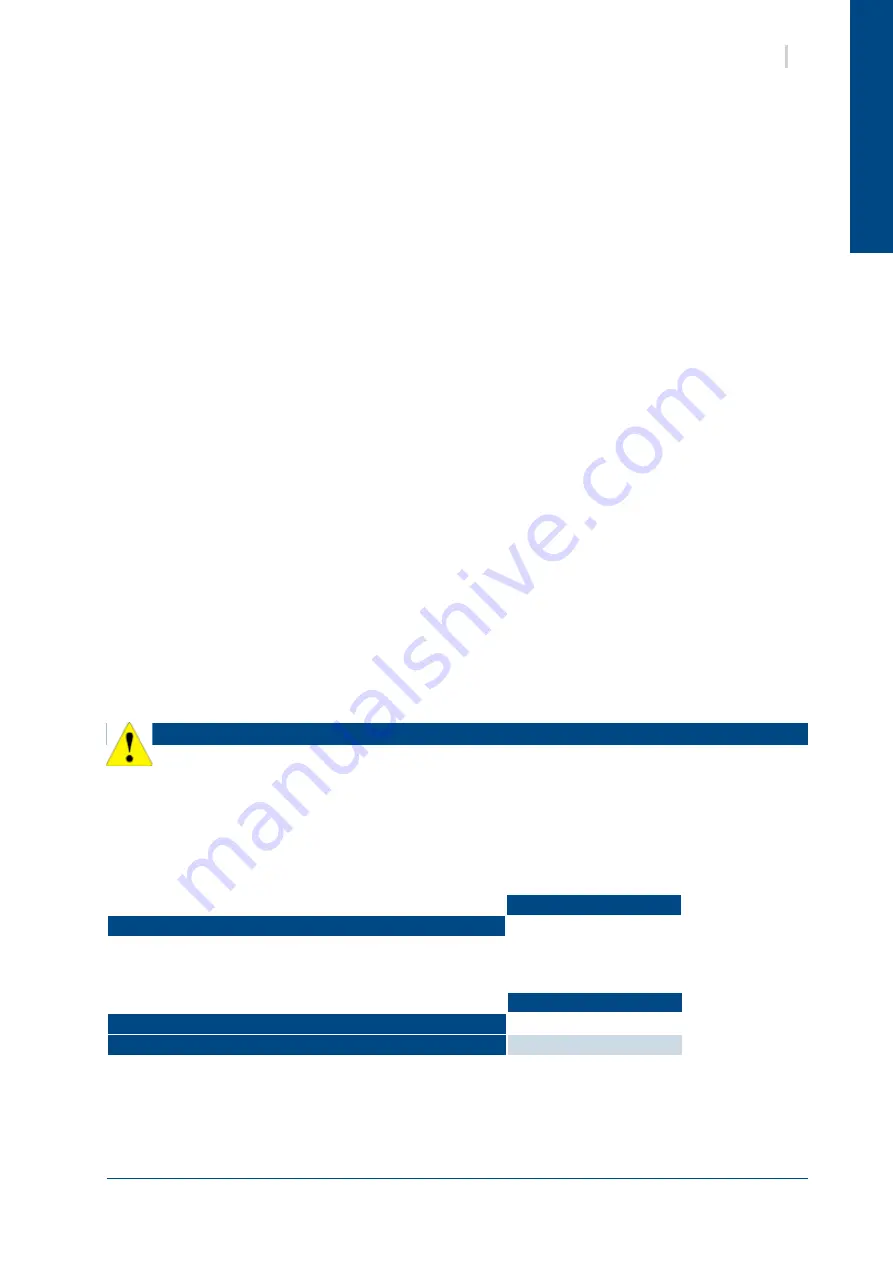
English
It is advisable to manage the unit's ON/OFF switching by way of the RCL/µBMS remote control or
by way of the CLOCK (CLK) dry contact switch present on the STORM2 circuit board, rather than by
switching the power supply on and off.
Caution
23
SysHrw
In the event of mains power supply being cut, and after power has been restored, the appliance will restart
in the same mode and with the same settings as before the power cut.
If the power cut lasts longer than 25 minutes, the RCL control module values will be lost, but the appliance
will restart with the same operating parameters as before the power cut. After a power cut lasting more
than 25 minutes, and after restarting, the RCL values will be false.
To minimise disruptions caused by power cuts the µBMS supervision module is equipped with rechargeable
batteries offering 24 hours autonomy. After 24 hours, the time and date will need to be reprogrammed.
However, the ON/OFF programmes and the various zone parameters will remain stored in its memory.
The battery recharging cycle lasts longer than 24 hours. If another power cut occurs whilst the batteries are
not 100% charged, the 24 hours autonomy cannot be guaranteed.
Theoretically, there is no need to replace the batteries. However, if they are to be replaced, we recommend
using the same type of batteries as those originally fitted. The old batteries should be disposed of in a
recyclable container intended for this purpose.
A dry contact switch can be connected to the CLOCK (CLK) input of the STORM2 circuit board for remote
ON/OFF control.
Effects of changing the CLK switch status:
²
Unit running:
Effect
The contact switch changes from "
Open
" to "
Closed
" status
Unit stops
Effect
The contact switch changes from "
Open
" to "
Closed
" status
None
The contact switch changes from "
Closed
" to "
Open
" status
Unit starts
²
Unit stopped:
General comments:
²
The CLK input has the highest priority level; if the contact is closed, the unit is stopped.
²
A separate dry contact switch must be used for each appliance.
²
We recommend the use of wire with a section not exceeding 1mm².
15.4. RETURN AIR TEMPERATURE MEASUREMENT
As the default factory setting, the jumpers are configured so that return air temperature measurement is
performed via a sensor located on the RCL control module.
If the RCL control module is not sited in the air-conditioned premises or is sited at a distance for various
reasons, we recommend the use of the Return sensor (RT) located on the appliance itself. To activate the
Return sensor (RT) located on the appliance, you just have to cut off the jumper J5 located on of the STORM2
circuit board (Refer to previous paragraph).
If the appliance is installed with an air intake duct and the fan is OFF when there is no demand for Heating
( Jumper J3 Closed) (Refer to previous paragraph), we do NOT recommend the use of the return air sensor
(RT) located on the appliance. It is preferable to install an RCL control module or an ambient sensor box,
available as options from our sales department.
15.5. POWER FAILURE
15.6. REMOTE ON/OFF MAKE/BREAK SWITCH