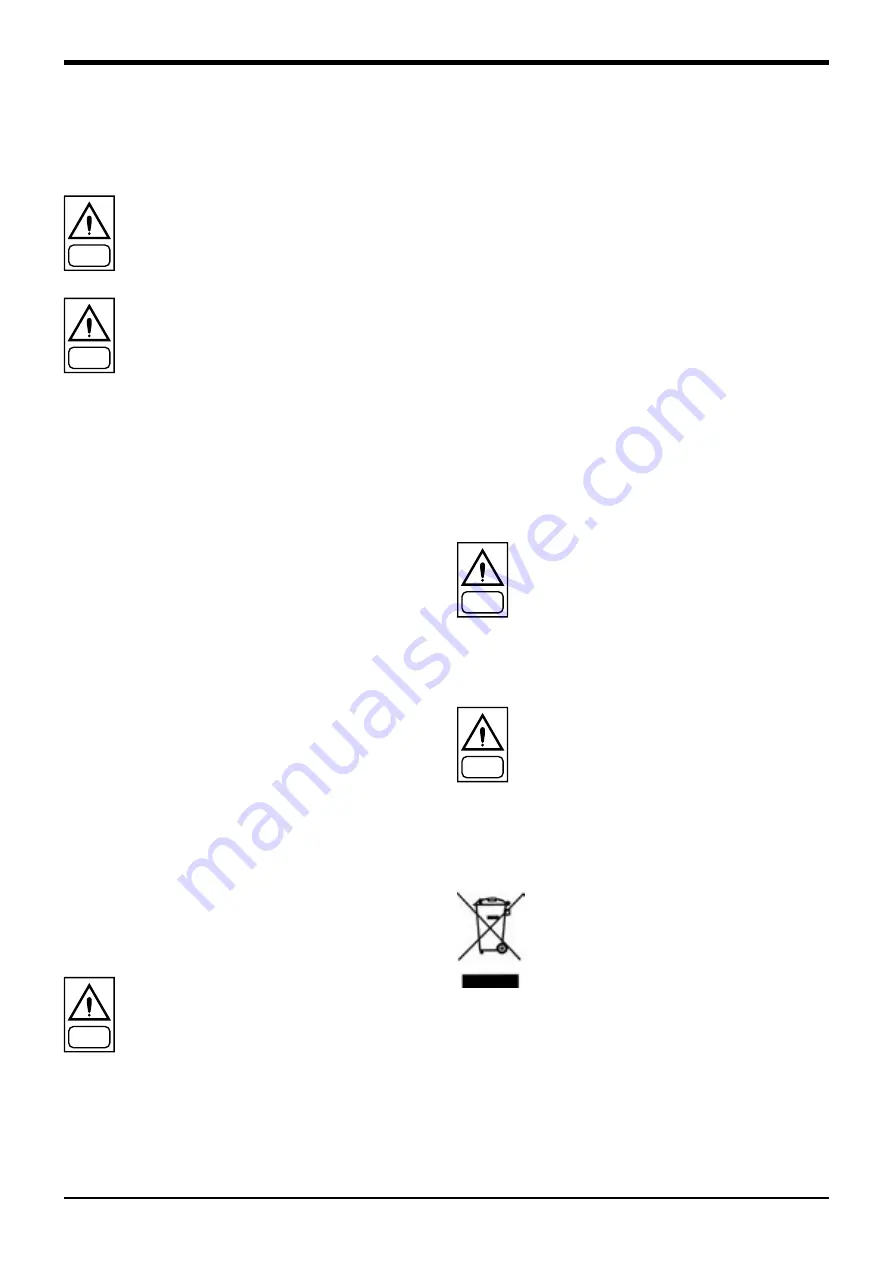
Page 58
Dismantling, Demolition and Scrapping
12 DISMANTLING, DEMOLITION
AND SCRAPPING
During the draining of the refrigeration cir-
cuits, do not let the refrigerant overflow in
the surrounding atmosphere.
The circuit must be drained using suitable
recovery equipment.
Do not disperse the waste oil of the com-
pressors in the environment, since it con-
tains some dissolved refrigerant.
For the disposal, contact the competent authority for
information.
Unless otherwise specified, the maintenance opera-
tions listed below may be carried out by any trained
maintenance operator.
12.1 Generalities
Open each line that supplies the unit, including the
ones of control circuits. Make sure that all disconnect-
ing switches are secured in the off position. The power
cables can be disconnected and disassembled. Refer
to Chapter 4 for the position of connection points.
Remove all the refrigerant from the refrigeration cir-
cuits of the unit and store it in suitable containers,
using a recovery unit. If its characteristics have re-
mained the same, the refrigerant can be used again.
Contact the competent authority to obtain information
about disposal. In
NO
event shall the refrigerant be
discharged into the atmosphere. The oil in each re-
frigeration circuit must be drained and collected into a
suitable container; then it shall be disposes of in con-
formity with local regulations that apply to the disposal
of waste lubricants. Any oil spillage must be recovered
and disposed of in like manner.
Isolate the unit’s heat exchangers from the external hy-
draulic circuits and drain the heat exchange sections
of the plant.
If no shutoff valves have been provided, it
may be necessary to drain the whole plant.
If a glycoled solution or a similar fluid has
been used in the hydraulic circuits, or if
chemical additives have been added to the
circulating water, the circulating fluid MUST
be drained in a proper way.
For NO reason shall a circuit containing
glycoled water or a similar solution be dis-
charged directly into the drains or surface
waters.
After draining operations, the piping of the hydraulic
networks can be disconnected and disassembled.
Once they have been disconnected as specified, the
packaged units can be disassembled in a single piece.
First of all, disassemble the anchoring screws and then
lift the unit from the position of installation, and hook
it to the lifting points provided, using suitable lifting
equipment.
To this end, refer to Chapter 4 for the installation of
these appliances, to Chapter 8 for their weights and
Chapter 3 for handling.
The units that, once disconnected, cannot be removed
in a single piece, must be dismantled on site; in this
case, be very careful with the weight and handling of
every single component.
It is always advisable to dismantle the units following
the installation steps, but in reverse.
Some residues of oil, glycoled water or sim-
ilar solutions may remain in certain parts of
the unit. These residues must be recovered
and disposed of according to the proce-
dures specified above.
It is very important to ensure that, while a component
of the unit is being removed, all the others are prop-
erly supported.
Use only lifting means of adequate capac-
ity.
Once disassembled, the components of the unit can be
disposed of in conformity with current regulations.
12.2 RAEE Directive (only UE)
• The RAEE Directive requires that the
disposal and recycling of electrical and
electronic equipment must be handled
through a special collection, in appropri-
ate centers, separate from that used for
the disposal of mixed urban waste.
• The user has the obligation not to dis-
pose of the equipment at the end of the
useful life as municipal waste, but to send
it to a special collection center.
• The units covered by the RAEE Direc-
tive are marked with the symbol shown
above.
• The potential effects on the environment
and human health are detailed in this
manual.
DANGER
DANGER
DANGER
DANGER
DANGER
Summary of Contents for AQVC 105
Page 60: ...English Page 59 Note...
Page 61: ...Page 60 Note...