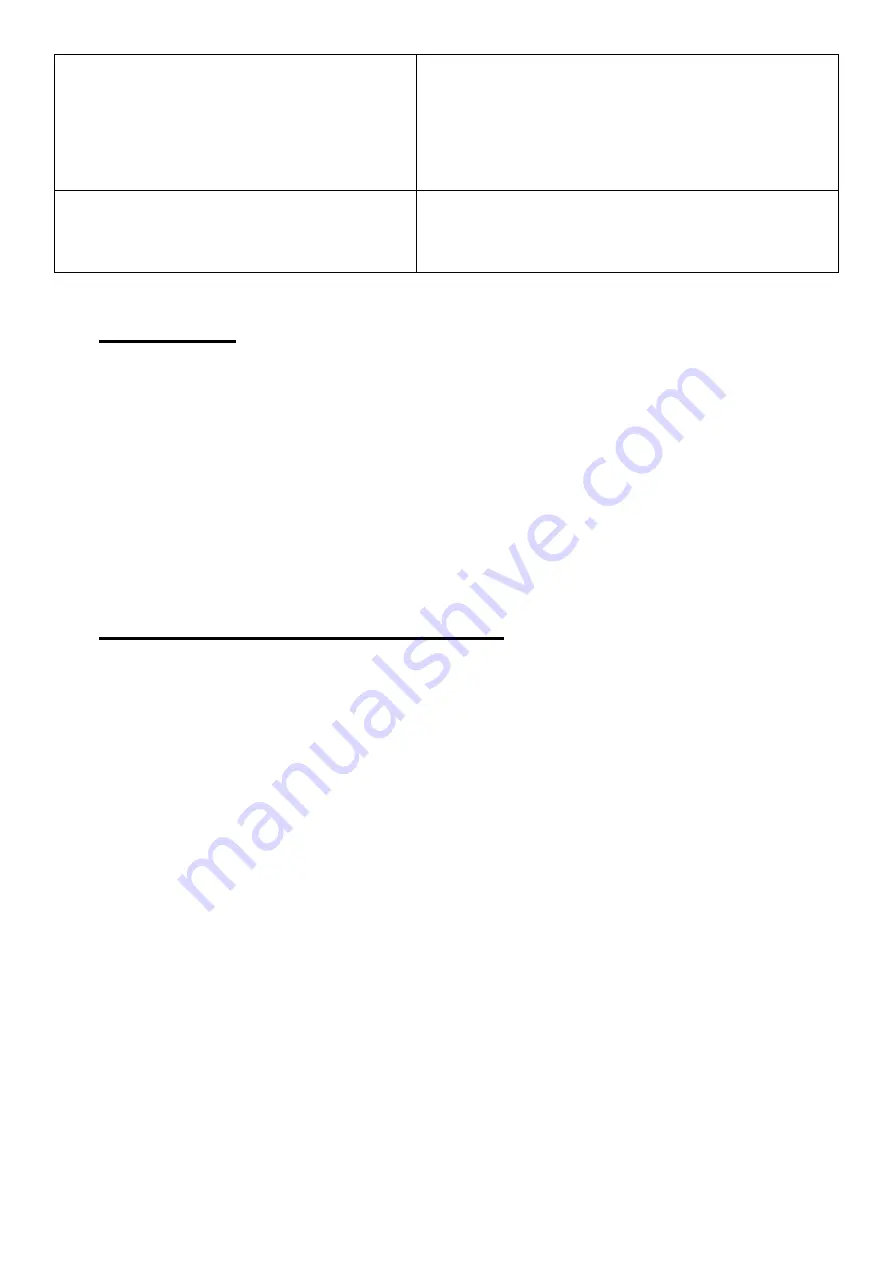
3
equipment, power must be shut off to
all circuits before any work is
attempted. Individual switches must
be opened and the equipment circuits
tested to make sure there is no power.
adjustments while it is running.
7. Be sure all operators are aware of all
areas and operations that require
extra safety measures.
7. Do not allow horseplay in the work area
1.4 AC Supply
1.4.1 Voltage steady state voltage: 0.9 to 1.1 of nominal voltage.
1.4.2 Frequency 099 to 1.01 of nominal frequency continuously; 0.98 to 1.02 for short time.
1.4.3 Harmonics distortion not exceeding 10% of the total r.m.s. voltage between live
conductors for the sum of the 2
nd
through to the 5
th
harmonic.
1.4.4 Voltage Interruption Supply interrupted or at zero voltage for not more than 3ms at any
random time in the supply cycle with more than 1 s between successive interruptions.
1.4.5 Voltage dips not exceeding 20% of the peak voltage of the supply for more than one
cycle with more than 1 s between successive dips.
1.5 General Physical Environments
1.5.1 The minimum requirement for all electrical equipment is correct operation between air
temperature of +5
゚
C and +35
゚
C.
1.5.2 Electrical equipment is capable of operating correctly when the relative humidity does
not exceeding 50% at a maximum temperature of +45
゚
C.
1.5.3 Electrical equipment is capable of operating correctly at altitude up to 1000m.
1.5.4 Electrical equipment is designed to withstand to protect against the effects of
transportation, and storage temperature within a range of -25
゚
C to +55
゚
C and for short
periods not exceeding 24 hours at up to +70
゚
C.
1.5.5 Avoid exposing to vibration environment.
1.5.6 Avoid exposing to direct sunlight or heat rays.
1.5.7 Have to connect to the factory grounding system correctly.
1.5.8 Away from electric magnetic interference source sites, such welding, discharge
machine.
Summary of Contents for CP330B
Page 1: ...CP330B Auto Creaser Operation Manual Revision 18 10 21...
Page 2: ......
Page 24: ...22 touch each other Warning Be careful when opening the safety cover...
Page 27: ...25...