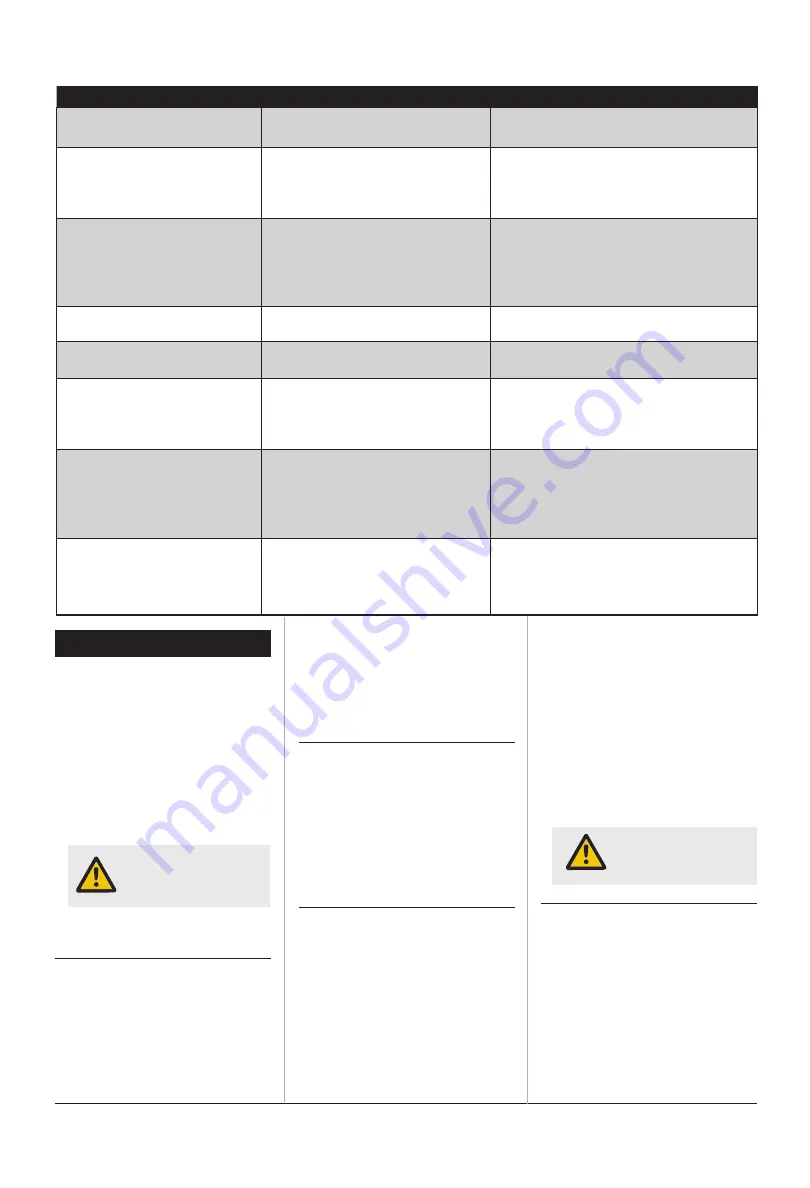
Service Instructions
Removing control spindle assembly
(Ref. Parts Assembly figure)
■Shut off water supply to valve
and remove control valve handle
and dome cover.
■Remove escutcheon plate by first
removing escutcheon screws.
■Turn valve’s
control spindle
to half
way position between minimum
and maximum rotation.
Important:
Failure to
do this can damage
control spindle assembly
.
■Unscrew both
spindle cap
and
control spindle assembly.
Hot/Cold Seat Repair Kit
Order p/n TA-4, T-35A and T-35B.
Installation requires both hot & cold
removal tools, p/n
T-35A & T-35B
.
■Remove
control spindle assembly
.
■Remove both seats with removal
tools.
■Replace both seats even if only
one appears worn.
■Install and tighten both seats to
15 foot pounds of torque.
Control Spindle Washer Repair Kit
Order p/n TA-9.
■Remove
control spindle assembly
.
■Remove
cold washer
by holding
spindle using valve handle and
unscrew
cold washer retainer
using channel lock pliers.
■Remove
hot washer
by removing
hot washer screw
.
Checking Water Pressure
Balancing Piston
The perforated end of the
control
spindle assembly
houses the water
pressure balancing piston which is
the heart of the valve.
■Remove
control spindle assembly
.
■Shake spindle assembly and listen
for clicking noise. Piston should
be free to slide back and forth the
full length of its travel.
■If piston appears restricted then
do the following:
(1) Tap the handle or stem end of
the spindle against a solid object
to free the piston.
(2) Try soaking in household
vinegar and repeat step (1).
■If unable to free piston, replace
control spindle
,
p/n
TA-10.
Important:
Do not
attempt removal of
the piston.
Valve re-assembly
Reassemble by reversing above
procedures.
After the
control spindle assembly
(TA-10) is threaded back into the
spindle cap assembly (TA-12A)
ensure
control spindle
is rotated 1/2
turn clockwise from its maximum
counter clockwise rotational
position. Failure to do this will
damage assembly.
Symmons Industries, Inc.
■
31 Brooks Drive
■
Braintree, MA 02184
■
Phone: (800 )796-6667
■
Fax: (800) 961-9621
Copyright © 2017 Symmons Industries, Inc.
■
symmons.com
■
■
ZV-1092R REV A
■
110917
Trouble Shooting Chart
Problem
Cause
Solution
Valve will not pass water.
Both hot and cold water supplies are
not turned on.
Turn on both supplies. Valve will not operate
unless both hot and cold water pressure is on.
Valve leaks when shut off.
Hot and cold washers are worn or
foreign matter (dirt, chips) is lodged
between washers and seat surfaces.
1) Replace washers using
control spindle
washer repair kit
, p/n TA-9.
2) Replace hot & cold seats using
hot/cold
seat repair kit
, p/n TA-4.
Temperature control handle is
turned from cold to hot (or hot
back to cold) and volume from
spout or head is not constant.
Pressure-balancing piston housed in
spindle assembly is restricted from free
movement by foreign matter.
1) Open valve halfway, remove handle and
tap spindle with plastic hammer.
2) Check
water pressure balancing piston
in
control spindle
. See service instructions.
3) Replace
control spindle
, p/n TA-10.
Valve delivers sufficient quantity of
cold, but little hot, or the reverse.
Same as above
Same as above
Temperature varies without
moving handle.
Same as above
Same as above
Valve delivery temperature reduces
gradually during use; handle must
be turned to hotter positions to
maintain constant temperature.
Overdraw on hot water supply
(i.e. running out of hot water).
Reduce maximum flow by using volume
control adjustment on valve or showerhead.
This will allow longer period of use before
overdrawing hot water supply.
Valve delivers hot water when
initially opened. Water turns
colder as handle is rotated in
a counter-clockwise direction
toward the hot position.
Valve is piped incorrectly (i.e. the hot
supply is piped to the valve’s cold inlet
and the cold supply is piped to the hot
inlet.)
If piping is accessible, correct connections to
the valve. If piping is not accessible, order
a
reverse seat and tool kit
, p/n T-108. Older
installations may also require replacing the
hot seat,
hot/cold seat repair kit,
p/n TA-4.
.