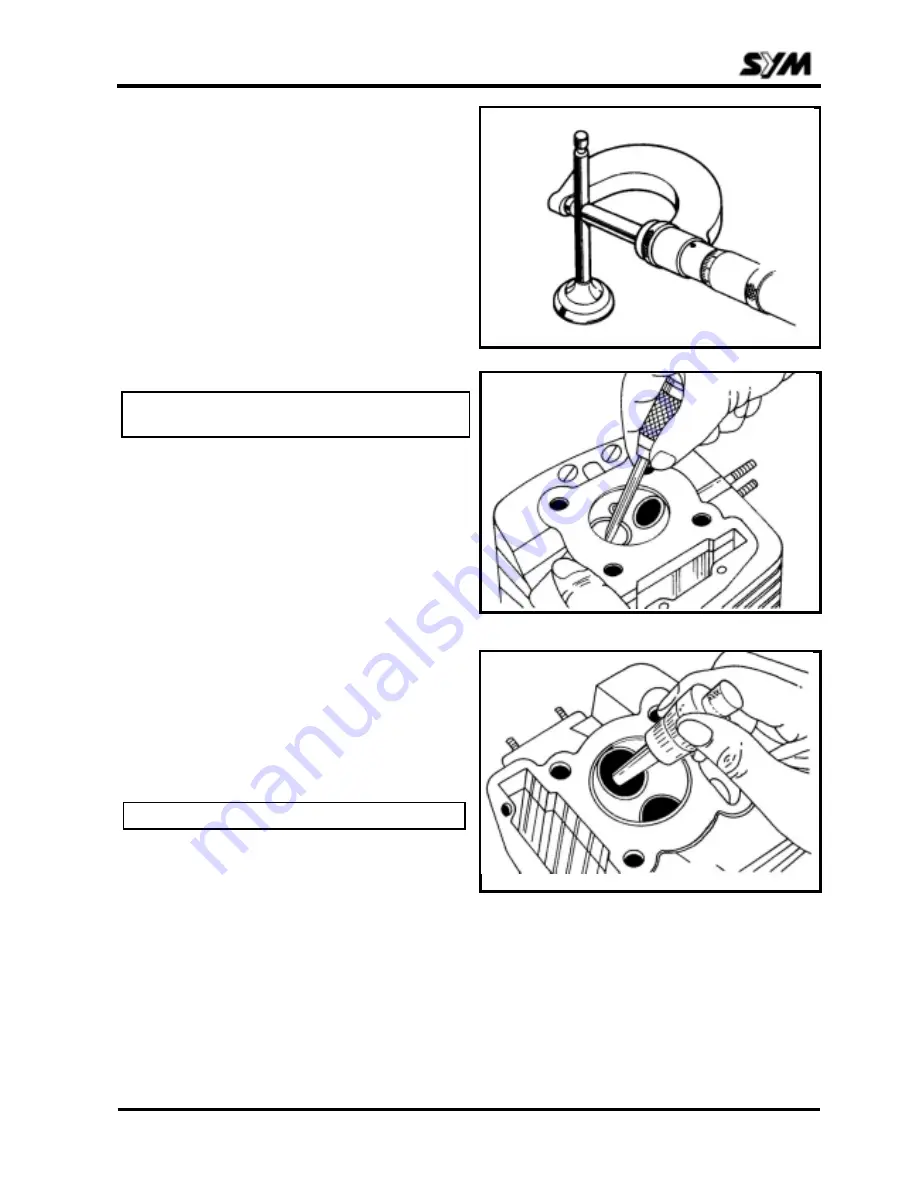
5.
CYLINDER HEAD/
VALVE
5-7
VALVE/VALVE GUIDE
INSPECTION
Inspect valves for scratches, burning or wear.
Check the valve movement in the guide.
Measure the valve stem O.D.
Service limit:
Intake:
∮
5.42mm
Exhaust:
∮
5.40mm
NOTE:
Guide I.D. service limit
Intake:
∮
5.50mm
Exhaust :
∮
5.50mm
Measure the valve guide I.D. and calculate the stem to
guide clearance.
Service limit:
Intake: 0.08mm
Exhaust: 0.10mm
If the stem to guide clearance exceeds the service
limit, replace the valve or guide to fit.
NOTE:
Remove any carbon buildup before checking the valve
guide I.D.
The guide must be reamed when replacing a new one.