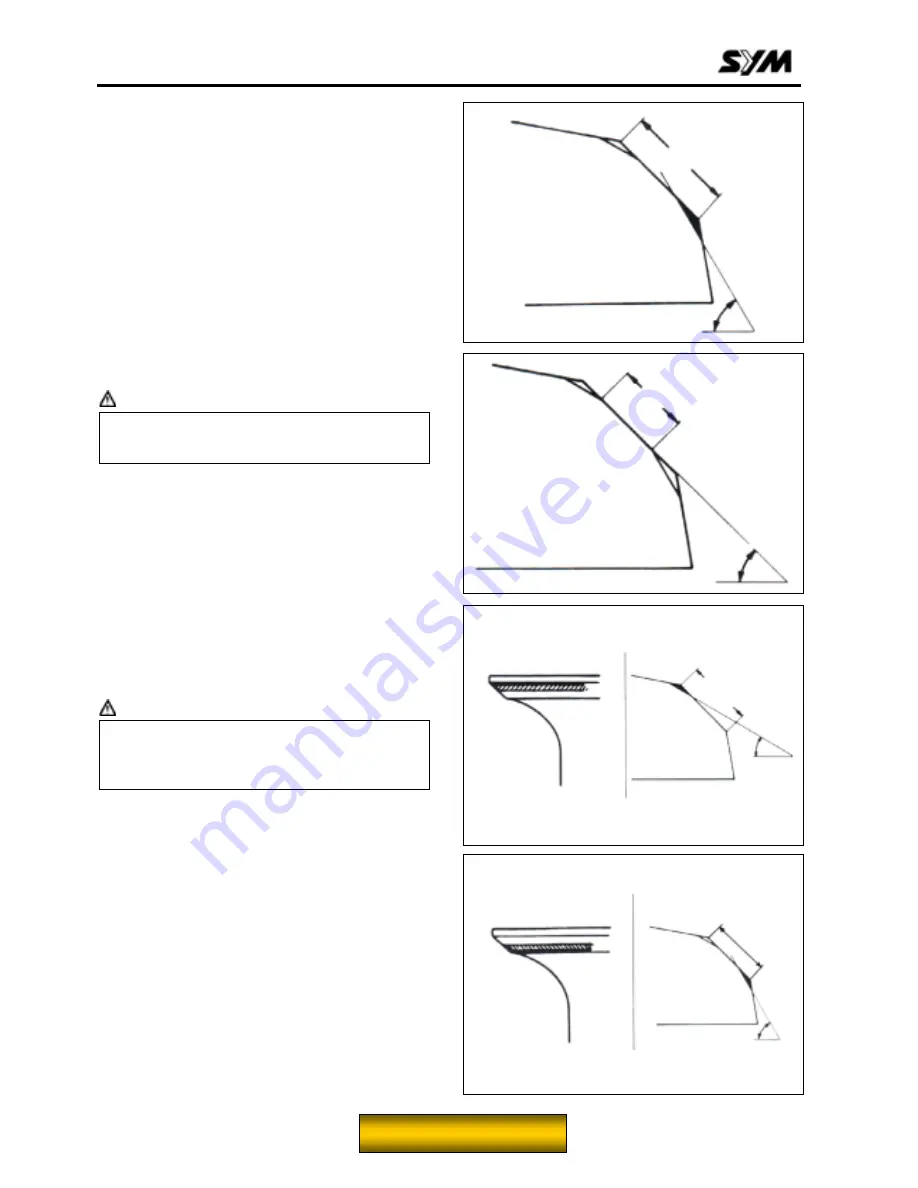
6. CYLINDER HEAD/VALVE
6-10
Use 60° cutter to cut a quarter lower part out.
Remove the cutter and check new valve seat.
Use 45° cutter to grind the valve seat to specified
width.
Caution
Grind valve seat again if necessary.
Coat the valve seat surface with red paint.
Install the valve through valve guide until the
valve contacting with valve seat, slightly press
down the valve but do not rotate it so that a seal
track will be created on contact surface.
Caution
If the contact surface too high, grind the valve
seat with 32° cutter.
Then, grind the valve seat to specified width.
If the contact surface too low, grind the valve
seat with 60° cutter.
Then, grind the valve seat to specified width.
z
Make sure that all roughness and uneven
faces had been ground.
z
The contact surfaces of valve and valve
seat are very important to the valve
sealing capacity.
Old valve seat width
60°
45°
1.0mm (0.04 in)
Contact surface too
high
Contact surface too
low
32°
60°
Old valve seat width
Old valve seat width
To this chapter contents
Summary of Contents for JOYRIDE 100
Page 1: ...SERVICE MANUAL FORWARD HOW TO USE THIS MANUAL CONTENTS...
Page 21: ...1 GENERAL INFORMATION 1 16 NOTES To this chapter contents...
Page 41: ...3 LUBRICATION SYSTEM 3 8 NOTES To this chapter contents...
Page 81: ...7 CYLINDER PISTON 7 8 NOTES To this chapter contents...
Page 103: ...9 FINAL DRIVING MECHANISM 9 8 NOTES To this chapter contents...
Page 111: ...10 ALTERNATOR STARTING CLUTCH 10 8 NTOES To this chapter contents...
Page 145: ...14 BRAKE 14 2 Rear Disk Brake System 4 5 kgf m 0 55 kgf m 3 5 kgf m To this chapter contents...
Page 153: ...14 BRAKE 14 10 Notes To this chapter contents...
Page 191: ...17 ELECTRICAL SYSTEM 17 20 NOTES To this chapter contents...
Page 196: ...18 SPECIAL TOOLS 18 5 BEARING DRIVER To this chapter contents...
Page 200: ...18 SPECIAL TOOLS 18 9 OUTER BEARING PULLER INNER BEARING PULLER To this chapter contents...
Page 202: ...19 WIRING DIAGRAM 19 1 LA12W LA15W SERIER WIRING DIAGRAM Homepage Contents 19...
Page 203: ...19 WIRING DIAGRAM 19 2 LA18W SERIER WIRING DIAGRAM Homepage Contents...