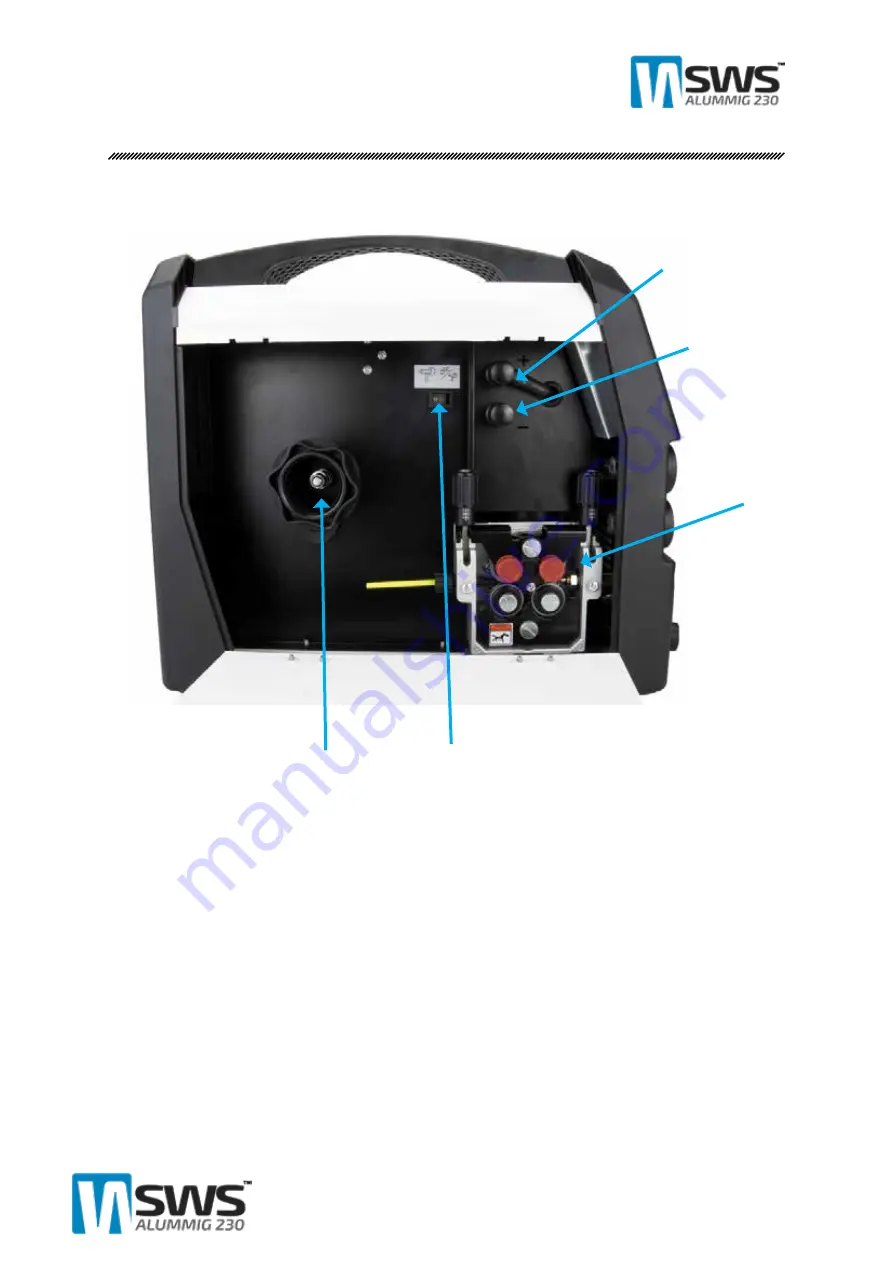
Manual Version 1.0
7
SIDE DOOR
1
2
3
5
4
1. MIG Torch EP Terminal - Electrode positive terminal with this connected the MIG torch
is positive (EP) the ground lead goes to (-) port
2. MIG Torch EN Terminal - Electrode negative terminal with this connected the MIG
torch is negative (EN) the ground lead goes to (+) port
3. Wire feeding unit
4. MIG wire spool carrier 200mm Diameter rolls only
5. Select spool gun or MIG torch and push pull torch operation