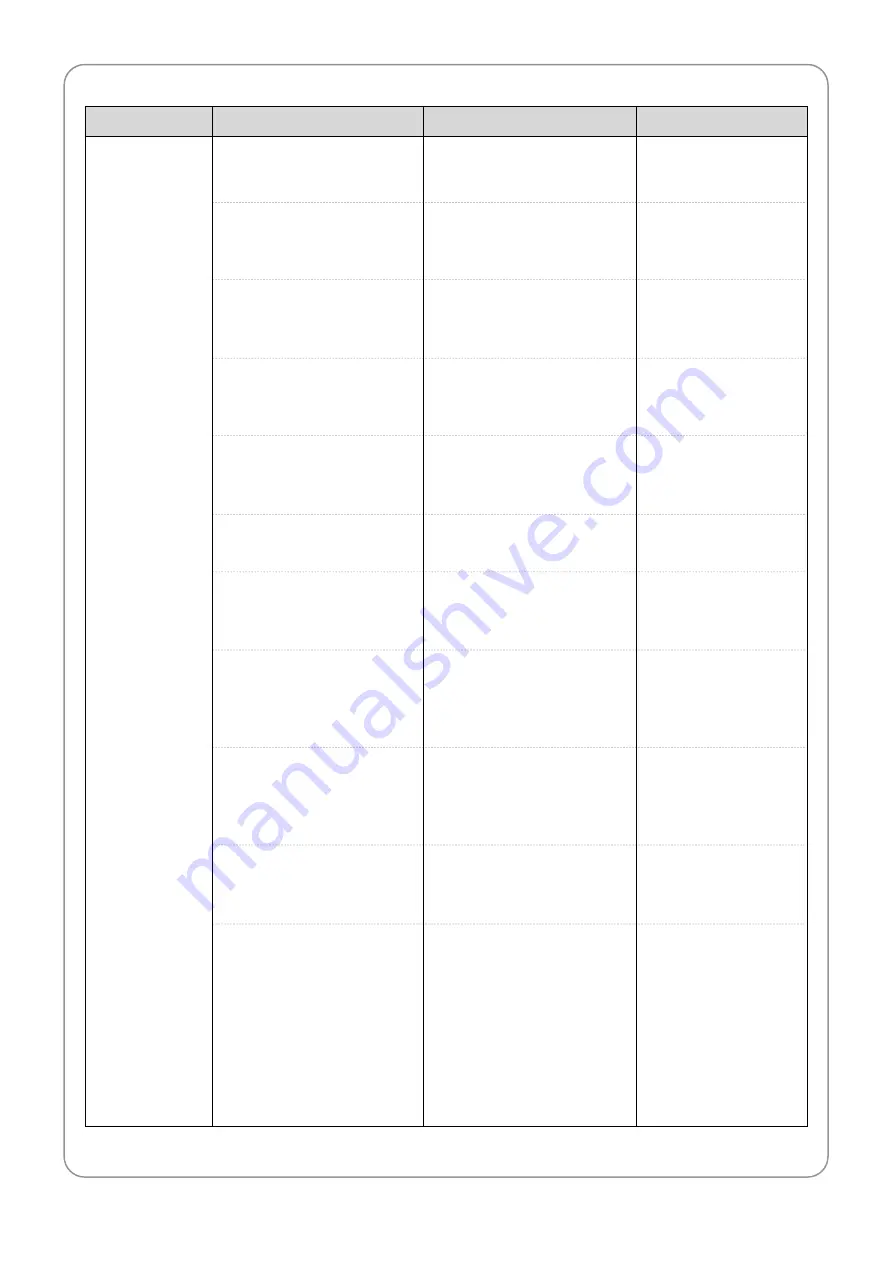
66
Skipped
Stitches
①
Bent needle
②
Inadequate needle size for
thread
③
Incorrect installation of
needle
④
Poor timing of needle and
hook
⑤
Large gap between needle
groove and hook point
⑥
Incorrect lower dead stop
⑦
Damaged hook point
⑧
Thread feeding is interfered
⑨
Inadequate thread
(twist, elasticity, and
flexibility)
⑩
Excessive tension or stroke
on the take-up lever spring
⑪
Fabric moves with needle -
weak or damaged presser
foot (spring)
■
Change needle
■
Change needle to
appropriate size
■
Adjust installation
■
Adjust needle-hook timing
■
Adjust the gap
■
Adjust the lower dead stop
■
Use whetstone to adjust
hook point or change hook
■
Adjust thread tension
For lower thread, change
bobbin or bobbin case
■
Select right thread for
embroidery
■
Adjust stroke or tension of
the spring
■
Change presser foot spring
Inspection & Repair
Cause
Error Type
Reference
Summary of Contents for MA-6
Page 2: ......