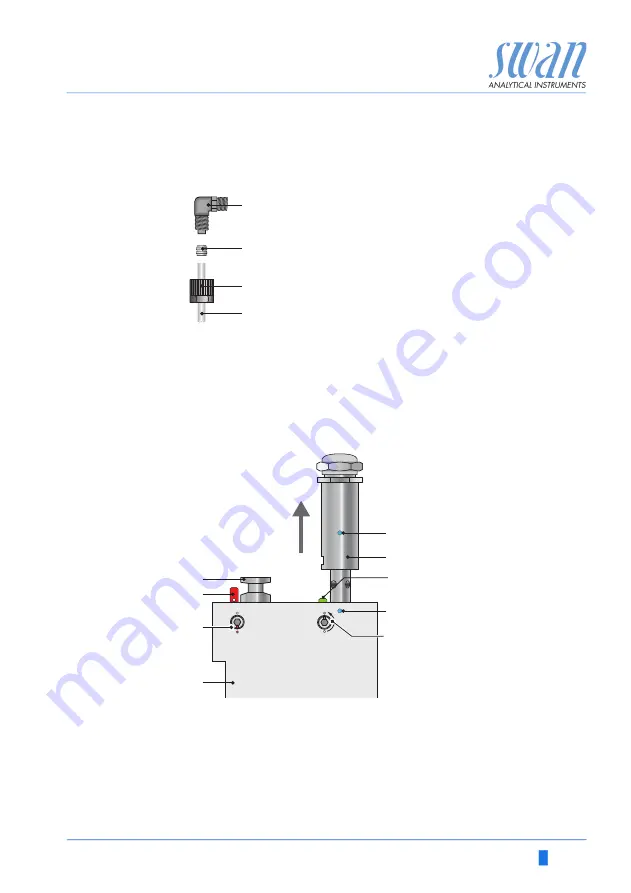
AMU Powercon
Installation
A-96.250.331 / 230320
15
2.4.2
FEP Tube at Sample Outlet
FEP flexible tube 6 mm
Connect the tube to the Serto elbow union and Insert it into an at
-
mospheric drain of sufficient capacity.
Max. tube length is 1.5 m. Do not connect longer tubes.
2.5. Install the Conductivity Sensor
1
Make sure that the locking mechanism is in unlocked position
(locking pin in position [G] and security screw in position [H]).
2
Put the sensor into the flow cell with the alignment marks [E] in
line.
3
Turn the locking screw with a 5 mm allen key clockwise 180°.
The locking pin moves up in lock position.
A
B
C
D
Ellbow union
Compression ferrule
Knurled nut
Flexible tube
B
C
D
A
A
B
C
D
E
F
G
H
Blind plug
Locking pin locked
Locking screw closed
Flow cell
Alignment marks
Conductivity sensor
Locking pin unlocked
Locking screw open
A
C
B
D
G
E
H
F
E