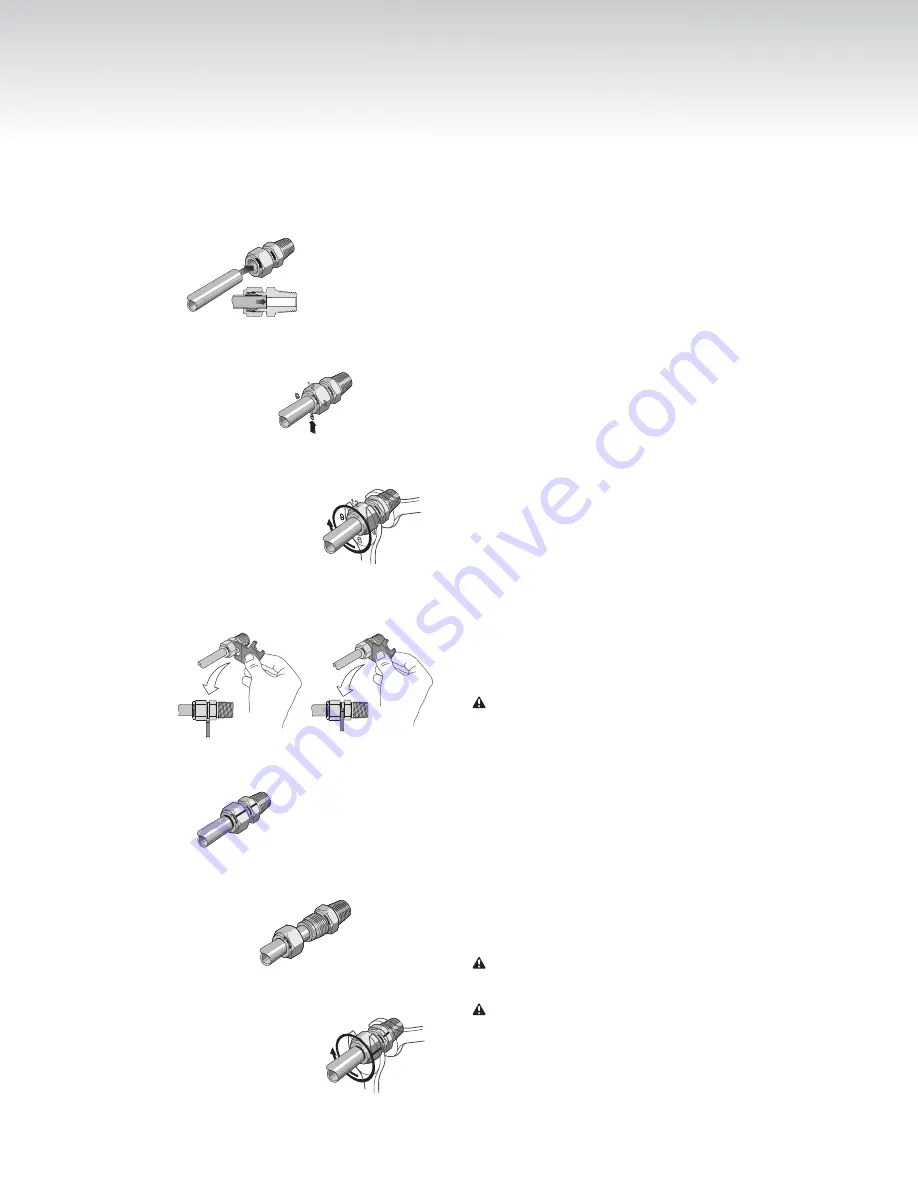
A Swagelok Pre-Engineered Subsystem Fast Loop Module
24
Swagelok Tube Fitting Instructions
for 1 in. (25 mm) and smaller
fittings
Fig. 1
Fig. 2
Fig. 3
Fig. 4
Fig. 5
Fig. 6
Fig. 7
Installation
These instructions apply to both traditional
fittings and to fittings with the advanced back-
ferrule geometry.
1. Fully insert the tube into the fitting and
against the shoulder; rotate the nut finger-
tight.
Fig. 1
.
High-Pressure Applications and High
Safety-Factor Systems:
Further tighten the
nut until the tube will not turn by hand or
move axially in the fitting.
2. Mark the nut at the 6 o’clock position.
Fig. 2
.
3. While holding the fitting body steady, tighten
the nut one and one-quarter turns to the
9 o’clock position.
Fig. 3
.
Note: For
1/16, 1/8,
and
3/16 in.; 2, 3,
and
4 mm
tube fittings, tighten the nut
three-quarters turn to the 3 o’clock position.
Gaugeability
On initial installation, the Swagelok gap
inspection gauge assures the installer or
inspector that a fitting has been sufficiently
tightened.
Position the Swagelok gap inspection gauge
next to the gap between the nut and body.
Fig. 4
.
• If the gauge will not enter the gap, the fitting
is sufficiently tightened.
• If the gauge will enter the gap, additional
tightening is required.
Reassembly Instructions
— You may
disassemble and reassemble Swagelok tube
fittings many times.
Warning
Always depressurize the system before
disassembling a Swagelok tube fitting.
1. Prior to disassembly, mark the tube at the
back of the nut; mark a line along the nut
and fitting body flats.
Fig. 5
.
Use these marks to ensure you return the nut to
the previously pulled-up position.
2. Insert the tube with preswaged ferrules into
the fitting body until the front ferrule seats
against the fitting body.
Fig. 6
.
3. While holding the fitting body steady, rotate
the nut with a wrench to the previously
pulled-up position as indicated by the marks
on the tube and the flats; at this point you
will feel a significant increase in resistance.
Fig. 7
.
4. Tighten the nut slightly.
Caution
Do not use the gap inspection gauge
with reassembled fittings.
Caution
Do not mix or interchange parts with
those of other manufacturers.
For additional information, see the
Gaugeable
Tube Fittings and Adapter Fittings
catalog,
MS-01-140.