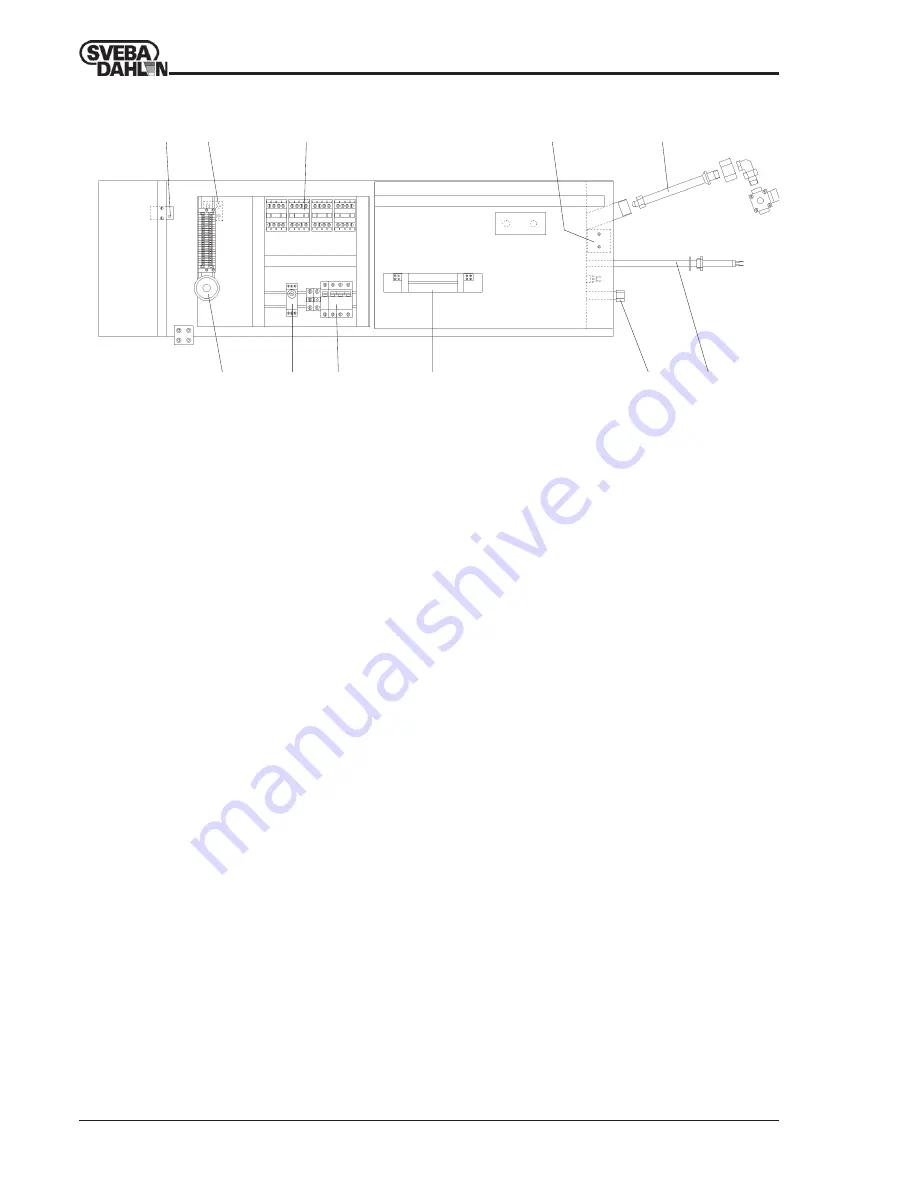
12
Operating Maintenance Installation CLASSIC
3:3500-2 --> 860004-02
1
2
3
7
8
2
4
5
6
9
10
1 Overheating protection
To get a complete disconnection, the fuse F1 of the
elements will also trip (see point 5 too).
If the overheating protection has triggered this can be
reset by pressing the reset button with a pen. The
button is reached through the small round hole in the
oven right-hand side panel.
Never use electrically conductive object when
resetting! Call technician if the protection triggers
repeatedly.
2 Buzzer
This is connected to the baking timer and gives a
signal when the baking time has expired. At the same
time as the buzzer is activated the green pilot lamp on
the instrument panel lights.
3 Contactor
One contactor for each group of elements, top, bot
tom and front heat. If the oven is fitted with a built-
in steam generator, there is a fourth contactor for this.
4 Time relay 0-100 seconds.
This relay only exists if the oven is fitted with steam
generator. The relay decides how long steam will be
sprayed into the over chamber when the steam control
on the front panel has been turned to the steam
position. The relay is set to 20 seconds on delivery but
can be adjusted where necessary.
Never use longer steam times than necessary since
this will reduce the capacity of the steam genera-
tor.
Fig. 12 Distribution box
DISTRIBUTION BOX
5 Automatic fuse
The 3-pole fuse protects the oven elements. On the
lower section there is also a 1-pole fuse. This is the
oven control fuse and is common to all sections in
the oven.
During service work in the oven the power supply to
the oven must be switched off. It is not sufficient to
switch off the oven built-in automatic fuses.
6 Light transformer
Transformer for the halogen light. Two lamps are
connected to each transformer.
7 Thermostat 300-350°C
Thermostat for regulating the steam generator. The
temperature is locked and cannot be changed.
8 Nozzle pipe
There is a nozzle on the pipe which disperses the
water into the steam generator. In the event of inferior
steam function the pipe can be removed and cleaned.
The nozzle at the end of the pipe is dismantled after
which the strainer and nozzle can easily be cleaned.
9 Drain pipe
This pipe is plugged on delivery. We recommend that
this pipe be connected to a drain by means of a steam
trap. This considerably lengthens the service-life of
the steam generator and its elements.
10 Element
The steam generator has four 500 W elements.