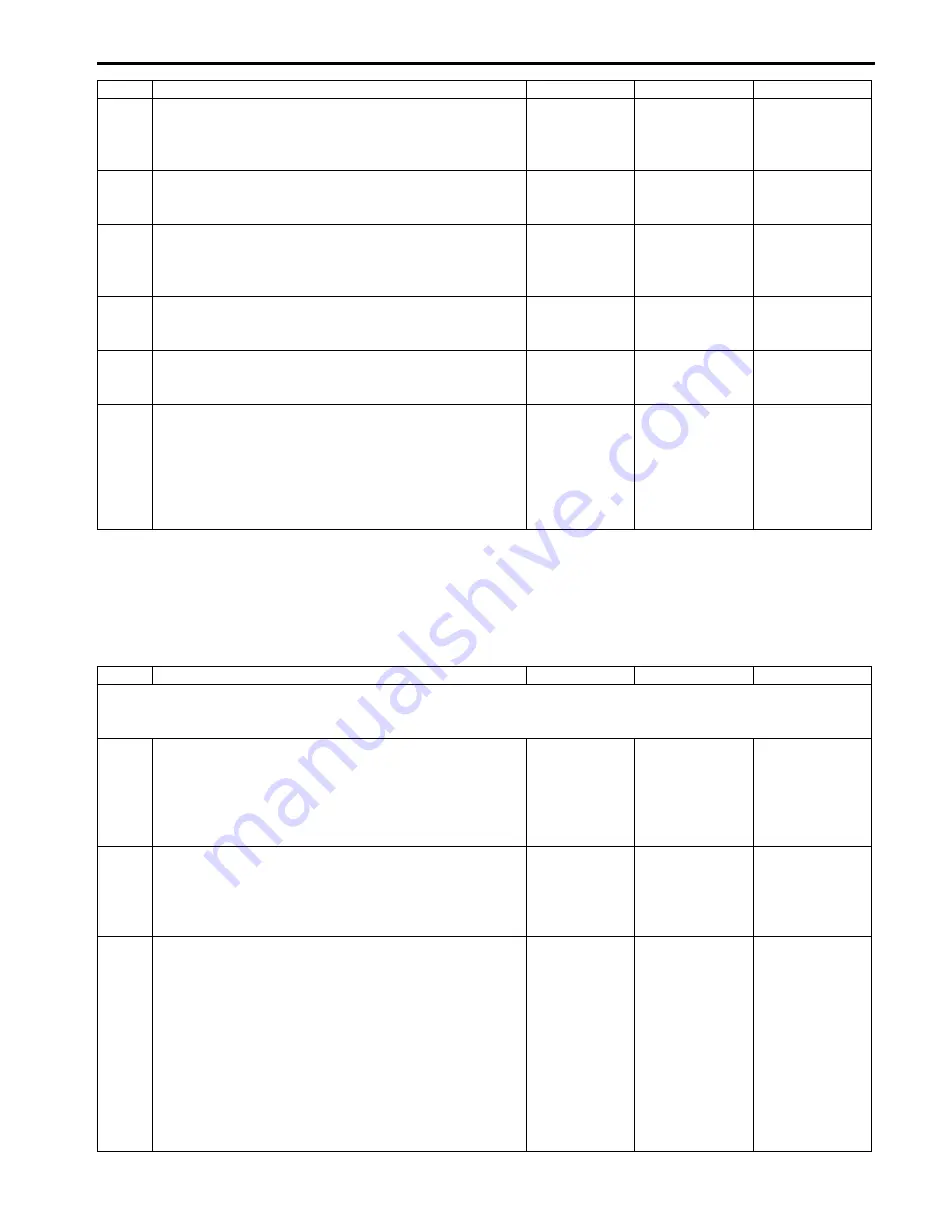
Sun Roof / T-Top / Convertible Top: 9I-11
Power Sunroof Does Not Open to Express Position
Test Description
The number below refers to the step number on the diagnostic table.
2.
If the express open feature does operate properly, then suspect the express open signal circuit for a poor connection
or intermittent.
33
Repair the ground circuit of the sunroof module for an
open or high resistance. Refer to “Circuit Testing: ” and
“Wiring Repairs: ”.
Did you complete the repair?
—
Go to Step 38
—
34
Replace the sunroof switch. Refer to “Sunroof Switch
Replacement”.
Did you complete the replacement?
—
Go to Step 38
—
35
Replace the sunroof module. Refer to “Control Module
References: ” for replacement, setup, and
programming.
Did you complete the replacement?
—
Go to Step 38
—
36
Replace the sunroof limit switch. Refer to “Sunroof
Motor/Actuator Replacement”.
Did you complete the replacement?
—
Go to Step 38
—
37
Replace the sunroof motor. Refer to “Sunroof Motor/
Actuator Replacement”.
Did you complete the replacement?
—
Go to Step 38
—
38
1. Remove any jumper wires.
2. Reconnect all previously disconnected components.
3. Replace sunroof fuse, if necessary.
4. Turn ON the ignition, with the engine OFF.
5. Operate the system in order to verify the repair.
Did you correct the condition?
—
System OK
Go to Step 2
Step
Action
Value(s)
Yes
No
Schematic Reference:
Connector End View Reference:
DEFINITION: Express open feature is inoperative.
1
Did you perform the Diagnostic System Check -
Vehicle?
—
Go to Step 2
Go to
2
Operate the power sunroof express open feature.
Does the system operate normally?
—
Go to “Testing for
Intermittent
Conditions and
Poor
Connections: ”
Go to Step 3
3
1. Remove the sunroof switch from the headliner.
2. Turn the ignition ON, with the engine OFF.
3. Operate the sunroof switch to slide the sunroof
glass to the close position.
4. Connect a 3-amp fused jumper wire between the
sunroof switch express signal circuit and the
sunroof switch open signal circuit at the sunroof
switch harness connector.
5. Press the sunroof switch to the express open
position.
Does the sunroof glass express open?
—
Go to Step 7
Go to Step 4
Step
Action
Values
Yes
No
Summary of Contents for 2007 XL7
Page 1: ...SERVICE MANUAL 99500S78J00 33E 2007 JC636...
Page 4: ......
Page 6: ......
Page 12: ...00 5 Precautions...
Page 110: ...1A 5 Engine General Information and Diagnosis Module Power Ground and MIL...
Page 111: ...Engine General Information and Diagnosis 1A 6 5 Volt Reference...
Page 112: ...1A 7 Engine General Information and Diagnosis Low Reference...
Page 114: ...1A 9 Engine General Information and Diagnosis Camshaft Position Sensors and Actuators...
Page 115: ...Engine General Information and Diagnosis 1A 10 Heated Oxygen Sensors...
Page 117: ...Engine General Information and Diagnosis 1A 12 Ignition Coils...
Page 118: ...1A 13 Engine General Information and Diagnosis Knock Sensors and Crank Sensor...
Page 119: ...Engine General Information and Diagnosis 1A 14 Fuel Injectors and Fuel Pump...
Page 121: ...Engine General Information and Diagnosis 1A 16 Controlled Monitored Systems...
Page 747: ...Engine Cooling System 1F 4 Engine Cooling Schematics...
Page 874: ...1I 2 Starting System Starting...
Page 875: ...Starting System 1I 3 Charging...
Page 900: ...1J 7 Charging System Starting...
Page 901: ...Charging System 1J 8 Charging...
Page 1098: ...2D 34 Wheels and Tires...
Page 1158: ...3C 2 Transfer Transfer Case Control...
Page 1216: ...3D 29 Propeller Shafts...
Page 1221: ...Brake Control System and Diagnosis 4A 2 Schematic and Routing Diagram...
Page 1222: ...4A 3 Brake Control System and Diagnosis Hydraulic Brake Schematics...
Page 1286: ...4B 14 Front Brakes Front Brake Caliper Replacement...
Page 1289: ...Front Brakes 4B 17 Front Disc Brake Hardware Replacement...
Page 1316: ...4C 14 Rear Brakes Rear Brake Caliper Replacement...
Page 1355: ...ABS 4E 5 Serial Data Traction Switch and Instrument Panel...
Page 1356: ...4E 6 ABS Wheel Speed Sensor...
Page 1357: ...ABS 4E 7 Yaw Rate and Lateral Accelerator Sensor and Steering Angle Sensor...
Page 1406: ...4E 56 ABS...
Page 1421: ...Automatic Transmission 5A 11 Park Engine Running...
Page 1424: ...5A 14 Automatic Transmission Reverse...
Page 1427: ...Automatic Transmission 5A 17 Reverse Inhibit...
Page 1430: ...5A 20 Automatic Transmission Neutral Engine Running...
Page 1433: ...Automatic Transmission 5A 23 Drive and M Range First Gear...
Page 1436: ...5A 26 Automatic Transmission M Range First Gear Engine Braking...
Page 1439: ...Automatic Transmission 5A 29 Drive and M Range Second Gear...
Page 1442: ...5A 32 Automatic Transmission Drive and M Range Third Gear...
Page 1445: ...Automatic Transmission 5A 35 Drive Range Fourth Gear...
Page 1448: ...5A 38 Automatic Transmission Drive Range Fifth Gear TCC Released...
Page 1451: ...Automatic Transmission 5A 41 Drive Range Fifth Gear TCC Applied...
Page 1453: ...Automatic Transmission 5A 43 Drive Range Emergency Fifth Gear...
Page 1455: ...Automatic Transmission 5A 45 Power and Ground...
Page 1456: ...5A 46 Automatic Transmission ISS OSS and TFT Sensors...
Page 1457: ...Automatic Transmission 5A 47 Shift and Pressure Solenoids...
Page 1458: ...5A 48 Automatic Transmission Shift Lock Control Schematics...
Page 1812: ...6C 30 Power Assisted Steering System...
Page 1822: ...7A 8 Heating Ventilation and Air Conditioning Air Temperature Sensors Ambient Light Sensor...
Page 1823: ...Heating Ventilation and Air Conditioning 7A 9 Mode Recirculation and Temperature Actuators...
Page 1824: ...7A 10 Heating Ventilation and Air Conditioning Rear HVAC Controls and Actuators...
Page 1825: ...Heating Ventilation and Air Conditioning 7A 11 A C Compressor Controls...
Page 1989: ...Seat Belts 8A 3 Seat Belt Schematics...
Page 2018: ...8B 6 Air Bag System SIR Schematics...
Page 2019: ...Air Bag System 8B 7 Power Ground Roll Over Sensor and PPS...
Page 2020: ...8B 8 Air Bag System Modules and Sensors...
Page 2021: ...Air Bag System 8B 9 Pretensioners and Front End Sensor...
Page 2072: ...8B 60 Air Bag System Inflatable Restraint Instrument Panel Module Replacement...
Page 2124: ...9A 16 Wiring Systems B BUS 1 of 2...
Page 2125: ...Wiring Systems 9A 17 B BUS 2 of 2...
Page 2128: ...9A 20 Wiring Systems AMP BCM CHMSL DIMR HVAC RFA and RDO Fuse...
Page 2130: ...9A 22 Wiring Systems POWER SEATS Circuit Breaker...
Page 2131: ...Wiring Systems 9A 23 BATT MAIN 3 DR LCK RRWPR RSE KEY CAPTR and S ROOF Fuses and POWER WNDW...
Page 2132: ...9A 24 Wiring Systems IGN SWITCH Fuse and Ignition Switch...
Page 2133: ...Wiring Systems 9A 25 PWR TRN BUS ETC ECM EVEN COILS INJ AND ODDCOILS INJ Fuses...
Page 2134: ...9A 26 Wiring Systems PWR TRN BUS EMM DEV1 EMM DEV2...
Page 2135: ...Wiring Systems 9A 27 RUN CRANK BUS MAF PCM IGN SIR DISPLAY and TRANS Fuses...
Page 2137: ...Wiring Systems 9A 29 LH PRK LP RH PRK LP and RH PRK LP TRLR Fuses...
Page 2138: ...9A 30 Wiring Systems HORN LH TRLR STOP TURN RH TRLR STOP TURN and STOP LP Fuses...
Page 2139: ...Wiring Systems 9A 31 Power Moding Schematics...
Page 2140: ...9A 32 Wiring Systems Power Moding...
Page 2141: ...Wiring Systems 9A 33 Ignition Lock Schematics...
Page 2142: ...9A 34 Wiring Systems Ground Distribution Schematics...
Page 2143: ...Wiring Systems 9A 35 G101...
Page 2144: ...9A 36 Wiring Systems G103 G105 G107 G108 and G109...
Page 2145: ...Wiring Systems 9A 37 G201...
Page 2146: ...9A 38 Wiring Systems G203 and G205...
Page 2147: ...Wiring Systems 9A 39 G301...
Page 2148: ...9A 40 Wiring Systems G311...
Page 2149: ...Wiring Systems 9A 41 G401...
Page 2150: ...9A 42 Wiring Systems G403...
Page 2151: ...Wiring Systems 9A 43 Trailer Connector Provision Schematics...
Page 2152: ...9A 44 Wiring Systems Trailer Wiring...
Page 2154: ...9A 46 Wiring Systems Body Harness Engine Compartment 1 C102 2 C101...
Page 2155: ...Wiring Systems 9A 47 Battery Cable Harness 1 C102 3 G103 2 Battery Current Sensor...
Page 2157: ...Wiring Systems 9A 49 Engine Harness Top of Engine 1 S115 3 S106 2 S114...
Page 2158: ...9A 50 Wiring Systems Fuel Injector and Transmission Harness 1 C105 3 S101 2 S104...
Page 2160: ...9A 52 Wiring Systems Console Harness 1 S301 3 C202 2 S300 4 C305...
Page 2162: ...9A 54 Wiring Systems Headliner and Sunroof Harness 1 C415 3 C417 U3U 2 C412 UUC...
Page 2238: ...9A 130 Wiring Systems G112 1 Rear Exhaust Manifold 2 G112...
Page 2239: ...Wiring Systems 9A 131 G107 and G105 1 G107 3 G105 2 Front Cylinder Head 4 Starter...
Page 2240: ...9A 132 Wiring Systems Engine Harness Rear 1 G108 2 G109...
Page 2325: ...Lighting Systems 9B 4 Headlights Daytime Running Lights DRL Schematics...
Page 2326: ...9B 5 Lighting Systems Fog Lights Schematics...
Page 2327: ...Lighting Systems 9B 6 Exterior Lights Schematics...
Page 2328: ...9B 7 Lighting Systems Left Park Lamps...
Page 2329: ...Lighting Systems 9B 8 License Lamps Right Park Lamps...
Page 2330: ...9B 9 Lighting Systems Turn Signal Lamps...
Page 2331: ...Lighting Systems 9B 10 Stop Lamps...
Page 2332: ...9B 11 Lighting Systems Backup Lamps...
Page 2333: ...Lighting Systems 9B 12 Trailer Tow Connector...
Page 2334: ...9B 13 Lighting Systems Interior Lights Schematics...
Page 2335: ...Lighting Systems 9B 14 Interior Lights Dimming Schematics...
Page 2439: ...Instrumentation Driver Info Horn 9C 8 Indicators...
Page 2440: ...9C 9 Instrumentation Driver Info Horn Gages...
Page 2441: ...Instrumentation Driver Info Horn 9C 10 Driver Information System Schematics...
Page 2442: ...9C 11 Instrumentation Driver Info Horn Audible Warnings Schematics...
Page 2443: ...Instrumentation Driver Info Horn 9C 12 Cigar Lighter Power Outlet Schematics...
Page 2444: ...9C 13 Instrumentation Driver Info Horn Horn Schematics...
Page 2449: ...Instrumentation Driver Info Horn 9C 18 Horn Component Views Horn Location 1 Horn...
Page 2513: ...Wipers Washers 9D 2 Front Wiper Washer...
Page 2514: ...9D 3 Wipers Washers Rear Wiper Washer...
Page 2554: ...9E 6 Glass Windows Mirrors Moveable Window Schematics...
Page 2555: ...Glass Windows Mirrors 9E 7 Defogger Schematics...
Page 2556: ...9E 8 Glass Windows Mirrors Inside Rearview Mirror Schematics...
Page 2557: ...Glass Windows Mirrors 9E 9 Outside Rearview Mirror Schematics...
Page 2565: ...Glass Windows Mirrors 9E 17 Rear Window Defogger 1 Rear Defogger Grid 2 Liftgate...
Page 2566: ...9E 18 Glass Windows Mirrors RR Door 1 Window Switch RR 3 Window Motor RR 2 Door Latch RR...
Page 2567: ...Glass Windows Mirrors 9E 19 LR Door 1 Door Latch LR 3 Window Motor LR 2 Window Switch LR...
Page 2627: ...Security and Locks 9F 6 Schematic and Routing Diagram Door Lock Indicator Schematics...
Page 2628: ...9F 7 Security and Locks Door Lock Motors and Relays...
Page 2629: ...Security and Locks 9F 8 Door Latches and Switches...
Page 2630: ...9F 9 Security and Locks Release Systems Schematics...
Page 2631: ...Security and Locks 9F 10 Remote Function Schematics...
Page 2632: ...9F 11 Security and Locks Theft Deterrent System Schematics...
Page 2633: ...Security and Locks 9F 12 Theft Deterrent...
Page 2640: ...9F 19 Security and Locks LR Door 1 Door Latch LR 3 Window Motor LR 2 Window Switch LR...
Page 2641: ...Security and Locks 9F 20 RR Door 1 Window Switch RR 3 Window Motor RR 2 Door Latch RR...
Page 2643: ...Security and Locks 9F 22 Liftgate Latch Location 1 Liftgate Latch...
Page 2689: ...Seats 9G 3 Driver Seat Schematics...
Page 2690: ...9G 4 Seats Heated Cooled Seat Schematics...
Page 2813: ...Sun Roof T Top Convertible Top 9I 3 Sunroof Schematics...
Page 2955: ...Body Structure 9K 63 Body Side Opening Underbody...
Page 2988: ...9O 7 Cellular Entertainment Navigation Audio Radio UC1...
Page 2989: ...Cellular Entertainment Navigation Audio 9O 8 Radio U65...
Page 2990: ...9O 9 Cellular Entertainment Navigation Audio Speaker U65...
Page 2991: ...Cellular Entertainment Navigation Audio 9O 10 Digital Radio Receiver U2K...
Page 2992: ...9O 11 Cellular Entertainment Navigation Audio Steering Wheel Controls...
Page 2993: ...Cellular Entertainment Navigation Audio 9O 12 Power Ground and Video Signal...
Page 2994: ...9O 13 Cellular Entertainment Navigation Audio Audio Signals...
Page 2996: ...9O 15 Cellular Entertainment Navigation Audio Remote Radio Steering Wheel Controls UK3...
Page 3061: ...Cruise Control System 10A 3 Cruise Control Schematics...
Page 3081: ...Data Communications 10B 5 Low Speed GMLAN...
Page 3082: ...10B 6 Data Communications High Speed GMLAN...
Page 3083: ...Data Communications 10B 7 Body Control System Schematics...
Page 3084: ...10B 8 Data Communications Power and Ground Starting and Charging...
Page 3086: ...10B 10 Data Communications Shift Lock Headlights Cruise Wiper and I P...
Page 3121: ...Immobilizer Control System 10C 2 Vehicle Theft Deterrent...
Page 3150: ...10D 13 Tire Pressure Monitoring System...
Page 3159: ...Prepared by 1st Ed Dec 2006 3154...