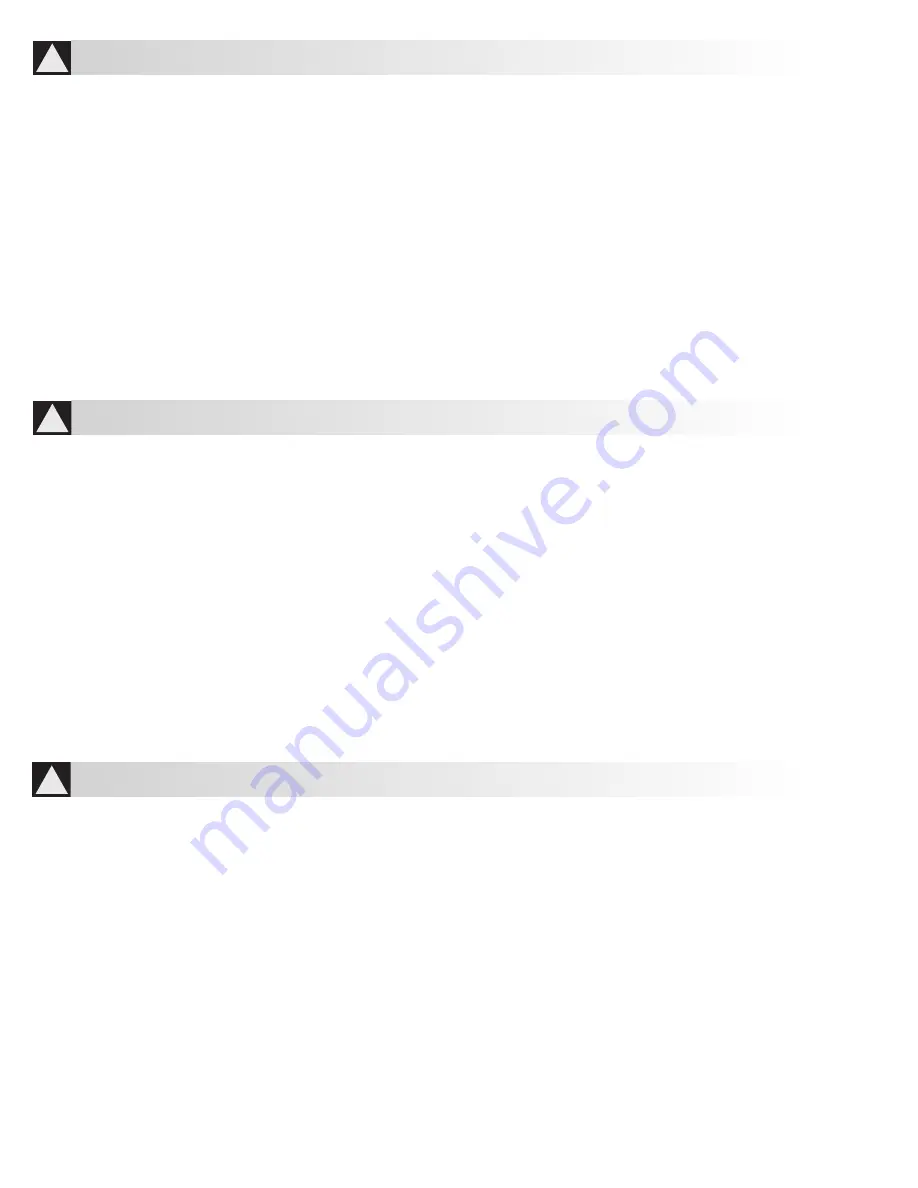
2
!
SETUP
Visually inspect all components for shipping damage. If any shipping damage is found, notify carrier at once. Shipping damage is NOT covered by
warranty. The carrier is responsible for all repair or replacement cost resulting from damage in shipment.
1 Visually inspect all components for shipping damage. If any shipping damage is found, notify carrier at once. Shipping damage is NOT covered
by warranty. The carrier is responsible for all repair or replacement cost resulting from damage in shipment.
2 Take out all the parts from the wooden box.
3 Assembling the casters (53/5)to the legs(48)by using Nut(50) Lock Washer(51) and Washer(52).
4 Assembling the legs(48)to pump(36) by using Washer (54) Lock Washer (55)and Bolt(56).
5 Assembling the support rod: First, assembling the Adjusted support rod(24)to support ring(19)by using Bolt(21)Lock Washer(22)and Nut(23),
and making the upper end of support ring(19) close to the lower end of Nut(25)(refer to Fig.1);Then adjusting the length of Round nut
base(17)and Bolt(26), making the hole of Bolt(26) align to the hole of the leg(48)(refer to Fig.2) and fix the Adjusted support rod(24) to leg(48)
by using Lock Washer(22), Nut(23)and Bolt(49), then tighten the Round nut base(17). At last, tighten the Bolt(20)to the Oil thank(27) cross
support ring(19).
6 Assembling the saddle(57): First loosen Bolt(S19) and take it out, then put saddle(57) on the Second piston rod(7), and tighten Bolt(S19)
saddle(57) on the Second piston rod(7), and tighten Bolt(S19).
!
WARNING!
•
The technician using this jack must be trained, qualified, fully familiar with safe work practices, and have prior experience in the use of
hydraulic equipment. Lack of knowledge in any of these areas can lead to equipment damage and/or personal injury.
•
Read, understand, and follow all instructions before operating this jack.
•
Inspect the jack before each use. Do not use jack if damaged, altered, modified, leaking hydraulic fluid or with missing or loose components.
•
Never modify or weld hydraulic equipment.
•
Never lift more that the rated capacity of the jack: overloading causes equipment failure and possible personal injury.
•
The jack is a load lifting device, not a load holding device. Once the load is raised, it must always be firmly supported with auxiliary stands.
Never work under or around a load supported only by hydraulic devices.
•
Never put unbalanced or off-centre loads on the jack saddle. Use saddle adapters and saddle extenders along with straps and chains to secure
load to the saddle head. Incorrect loading can result in equipment failure.
•
This jack was designed for lifting transmissions only. Consult the vehicle manufacturer for the transmission's centre of balance.
•
Secure the transmission to the jack’s saddle with the anchorage restraint system provided before raising or lowering the transmission.
•
Use of this product is limited to the removal, installation and transportation in the lowered position. Jack should only be used on a flat, clean,
unobstructed concrete floor.
•
Always wear safety glasses and/or other protective equipment that meet or exceed ANSI Z87.1 and OSHA standards.
•
Use the jack ONLY on hard, level surfaces capable of sustaining the load.
!
WARNING!
1. SERVICE/INSPECTION
Visual inspection shall be performed before each use of this equipment and its adapters, checking for abnormal conditions, such as cracked
welds, leaks, and damaged, loose or missing parts. This equipment shall be removed immediately from service if it is believed to have been
subjected to an abnormal or shock load and shall be inspected by a qualified repair facility. Owners and/or operators should be aware that repair
of this equipment may require specialized knowledge and facilities. It is recommended that this equipment be inspected annually by a qualified
repair facility. Defective parts, decals, safety labels or signs should be replaced with Strongarm specified parts.
The use of shop equipment is subject to certain hazards that cannot be prevented by mechanical means, but only by exercise of intelligence, care, and
common sense. It is therefore essential to have personnel involved in the use and operation of equipment who are careful, competent, trained, and
qualified in the safe operation of this equipment and its proper use when servicing motor vehicles and their components. Examples of hazards are
dropping, tipping, or slipping of motor vehicles or their components caused primarily by improperly securing loads, overloading, off-centered loads,
use on other than hard level surfaces, and using equipment for a purpose for which it was not designed. Only Strongarm attachments and/or adapters
may be used on this equipment.
The owner and/or operator shall study and understand the product and safety instructions before operating this equipment. Safety information shall
be emphasized and understood. If the operator is not fluent in English, the product and safety instructions shall be read to and discussed with the
operator in the operator’s native language by the purchaser/owner or his designee, making sure that the operator comprehends their contents. A
copy of these instructions/warnings shall be retained for future reference.
Summary of Contents for 030538
Page 6: ...6 PARTS...