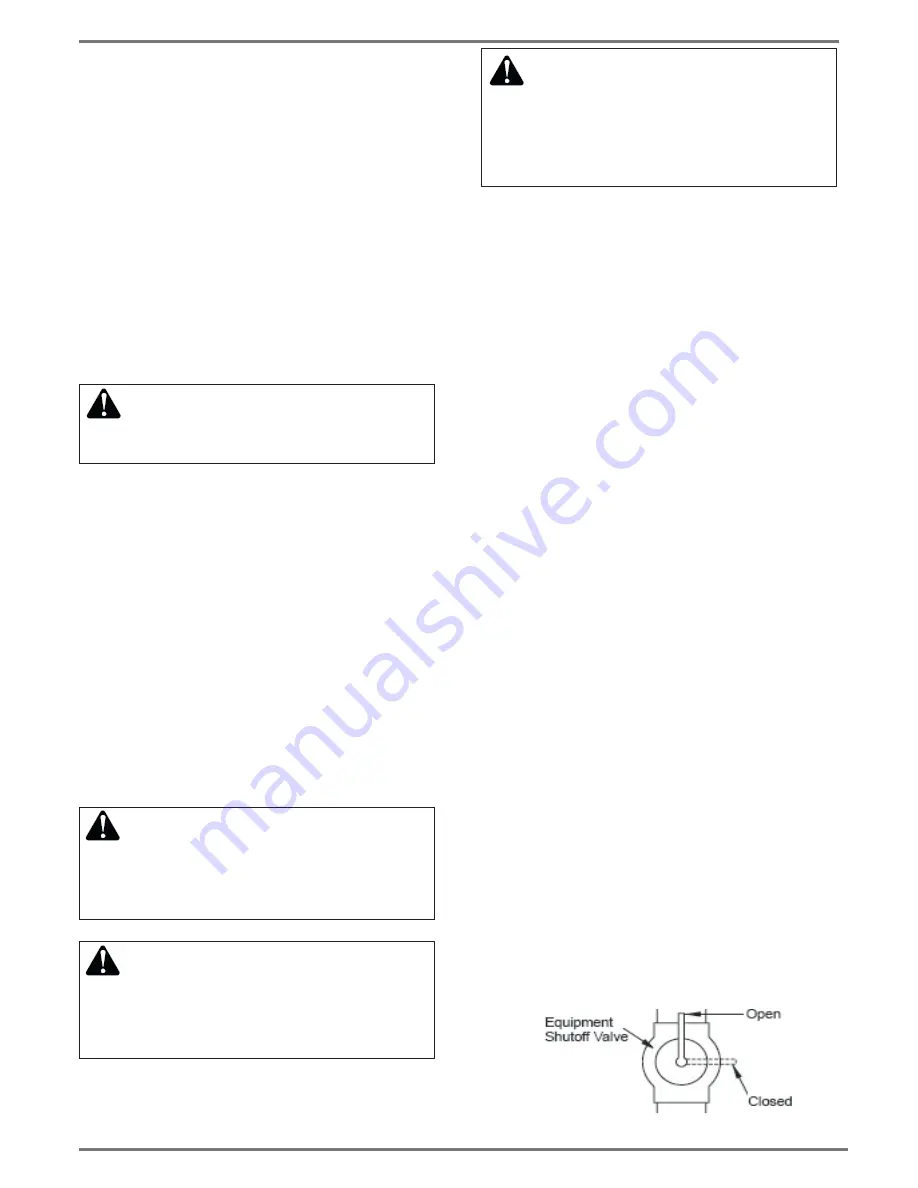
INSTALLATION
Continued
Installation must include equipment shutoff
valve, union and plugged 1/8" NPT tap. Locate
NPT tap within reach for test gauge hook up.
NPT tap must be upstream from heater (see
Figure 14, page 12).
IMPORTANT: Install an equipment shutoff
valve in an accessible location. The equip-
ment shutoff valve is for turning on or shutting
off the gas to the appliance.
Apply pipe joint sealant lightly to male NPT
threads. This will prevent excess sealant from
going into pipe. Excess sealant in pipe could
result in clogged heater valves.
Install sediment trap in supply line as shown
in Figure 14, page 12. Locate sediment trap
where it is within reach for cleaning. Locate
sediment trap where trapped matter is not
likely to freeze. A sediment trap traps mois-
ture and contaminants. This keeps them from
going into heater controls. If sediment trap is
not installed or is installed wrong, heater may
not run properly.
IMPORTANT: Hold the pressure regulator
with wrench when connecting it to gas pip-
ing and/or fi ttings. Do not over tighten pipe
connection to regulator. The regulator body
could be damaged.
CHECKING GAS CONNECTIONS
PRESSURE TESTING GAS SUPPLY
PIPING SySTEM
Test Pressures In Excess Of 1/2 PSIG
(3.5 kPa)
1. Disconnect appliance with its appliance
main gas valve (control valve) and equip-
ment shutoff valve from gas supply piping
system. Pressures in excess of 1/2 psig
will damage heater regulator.
2. Cap off open end of gas pipe where equip-
ment shutoff valve was connected.
3. Pressurize supply piping system by either
opening propane/LP supply tank valve
for propane/LP gas or opening main gas
valve located on or near gas meter for
natural gas or using compressed air.
4. Check all joints of gas supply piping system.
Apply a noncorrosive leak detection fl uid to
all joints. Bubbles forming show a leak.
5. Correct all leaks at once.
6. Reconnect heater and equipment shutoff
valve to gas supply. Check reconnected
fi ttings for leaks.
Test Pressures Equal To or Less Than
1/2 PSIG (3.5 kPa)
1. Close equipment shutoff valve.
2. Pressurize supply piping system by either
opening propane/LP supply tank valve
for propane/LP gas or opening main gas
valve located on or near gas meter for
natural gas or using compressed air.
3. Check all joints from gas meter for natural
gas (see Figure 16, page 14) or propane/
LP supply tank for propane/LP gas, to
equipment shutoff valve (see Figure 17,
page 14). Apply a noncorrosive leak
detection fl uid to all joints. Bubbles forming
show a leak.
4. Correct all leaks at once.
13
Figure 15 - Equipment Shutoff Valve
WARNING: Use pipe joint seala-
nt that is resistant to liquid petroleum
(LP) gas.
WARNING: Test all gas piping
and connections, internal and exter-
nal to unit, for leaks after installing or
servicing. Correct all leaks at once.
WARNING: Never use an open
fl ame to check for a leak. Apply a
noncorrosive leak detection fl uid to
all joints. Bubbles forming show a
leak. Correct all leaks at once.
CAUTION: For propane/LP gas,
make sure external regulator has been
installed between propane/LP supply
and heater. See guidelines under
Connecting to Gas Supply, page 12.