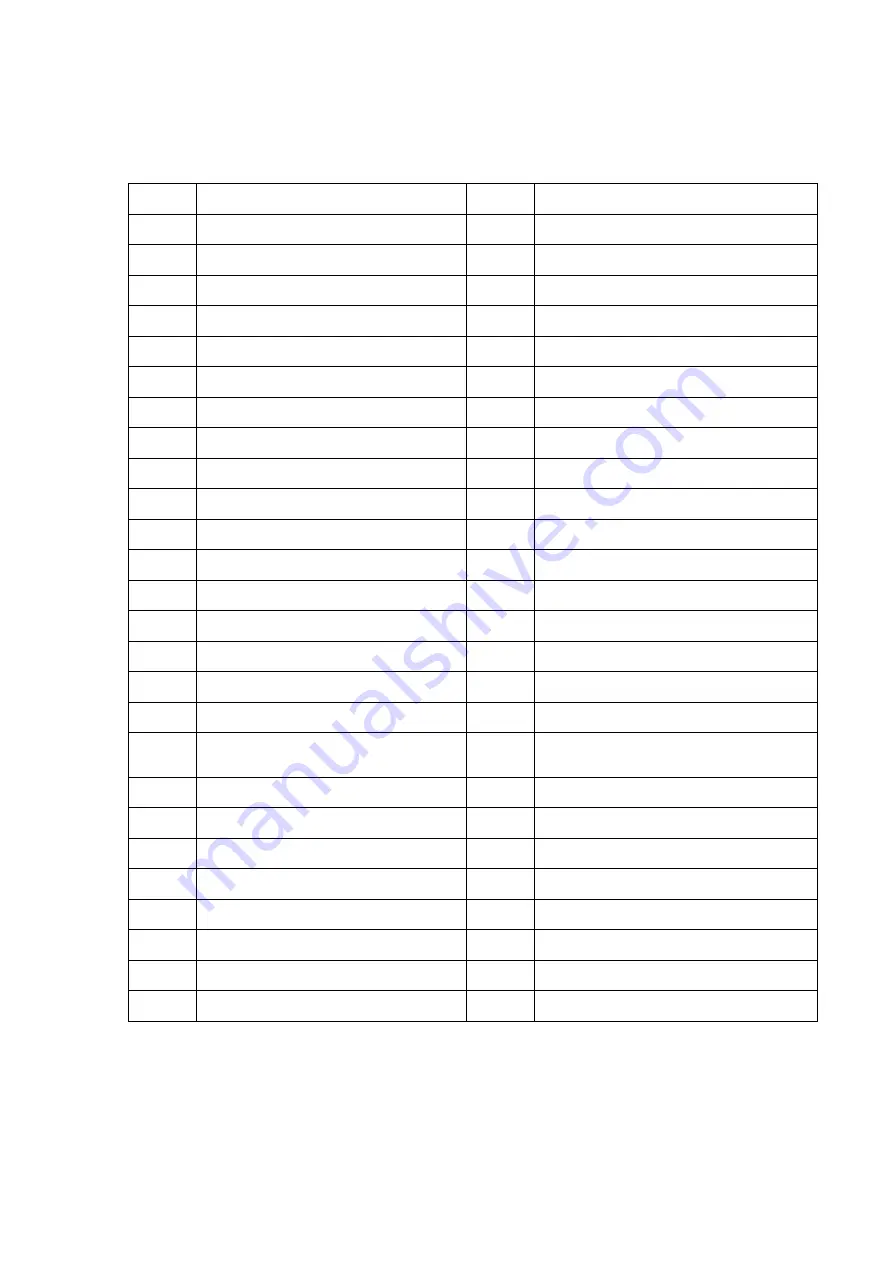
137
6.3.5 Electrical Elements table
NO.
NAME
NO.
NAME
1
Gear performer relay
27
Press button switch cover
2
Main relay
28
Ignition lock
3
Boom lamp relay
29
Monitor meter
4
Platform work lamp relay
30
Warm up relay
5
Starter
31
Controller
6
Head light relay
32
Electric oil pump
7
generator
33
Radio
8
Water temperature sensor
34
Washer assy.
9
Air filter indicator
35
Wiper controller
10
Overheat warning switch
36
Horn
11
Engine oil pressure warning switch
37
Lighter
12
Solenoid power switch
38
GPS
13
Throttle drive plate
39
Electric control case assy.
14
Pressure switch
40
Starting control relay
15
Work light
41
Connector
16
Oil level sensor
42
Single core plug
17
Micro-active switch
43
1S Delayed module
18
Press button switch end mounting
frame
44
15S Delayed module
19
Press button switch mid-frame
45
Horn relay
20
Auto-idle switch
46
Fuel gasoline pump
21
Quick selection switch
47
18 Core junctor
22
Front light switch
48
22 Core junctor
23
Work light switch
49
Warning lamp
24
Alarm light switch
50
Accumulator100Ah
25
Wiper switch
51
Battery clamp
(
with protective
)
26
Washer switch
52
Engine controller
Summary of Contents for SWE50B
Page 24: ...17 2 1 CAB As figure 2 1 shown Figure 2 1...
Page 38: ...31 No step on label...
Page 92: ...85 5 4 11 Hose...
Page 119: ...112 Engine Fault Diagnosed Code...
Page 120: ...113...
Page 121: ...114...
Page 129: ...122 6 1 4 Circuit Diagram 2R 2RL 2B FUSE 100 F 50V 100 F 50V motor sw motor relay FUSE B G R...
Page 131: ...124 6 1 6 Hydraulic Diagram...
Page 136: ...129 6 2 4 Circuit Diagram 2R 2RL 2B FUSE 100 F 50V 100 F 50V motor sw motor relay FUSE B G R...
Page 138: ...131 6 2 6 Hydraulic Diagram...
Page 143: ...136 6 3 4 Circuit Diagram...
Page 145: ...138 6 3 6 Hydraulic Diagram...
Page 150: ...143 6 4 4 Circuit Diagram...
Page 152: ...145 6 4 6 Hydraulic Diagram...
Page 157: ...150 6 5 4 Circuit Diagram...
Page 159: ...152 6 5 6 Hydraulic Diagram 280...
Page 164: ...157 6 6 4 Circuit Diagram...
Page 166: ...159 6 6 6 Hydraulic Diagram...
Page 171: ...164 6 7 4 Circuit Diagram...
Page 173: ...166 6 7 6 Hydraulic Diagram...
Page 178: ...171 6 8 4 Circuit diagram...
Page 185: ...178 6 9 4 Circuit Diagram...