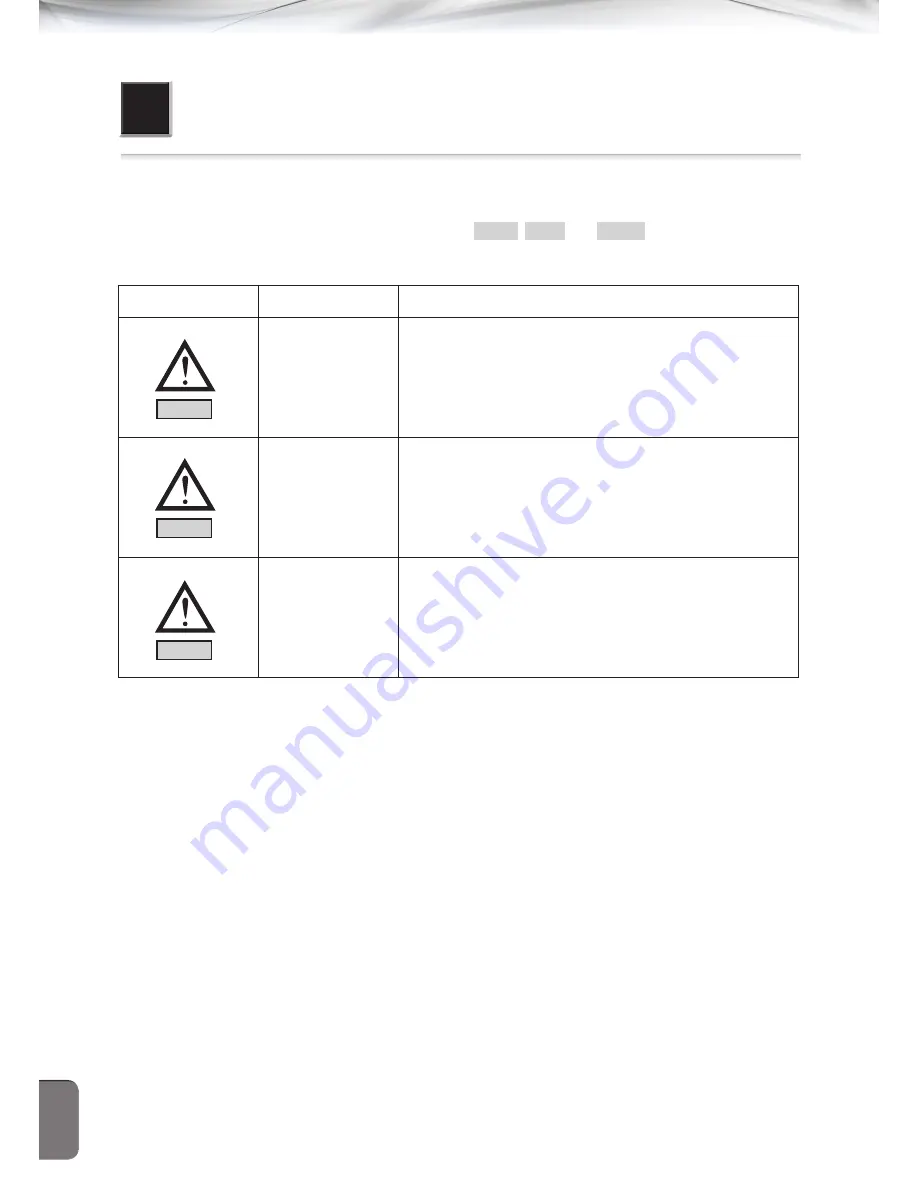
5
6
2
Safety rules
2.1 Description of safety indicators
This guidebook contains such safety indications as caution, danger, and warning. If the instructions are not
observed, it may bring about physical injuries or physical damages or mechanical damages.
No.
Name
Contents
CAUTION
If a user handled with the machine wrongly, it is expected that
physical injury or physical damage may occur.
WARNING
If a user handled with the machine wrongly, it is expected that
a user may be deceased or be in a critical injury.
DANGER
If a user handled with the machine wrongly, it is expected that
a user may be deceased or be in a critical injury and that is in
top emergency situation.
WARNING
WARNING
WARNING
Summary of Contents for SPS/F-1811 Series
Page 2: ......