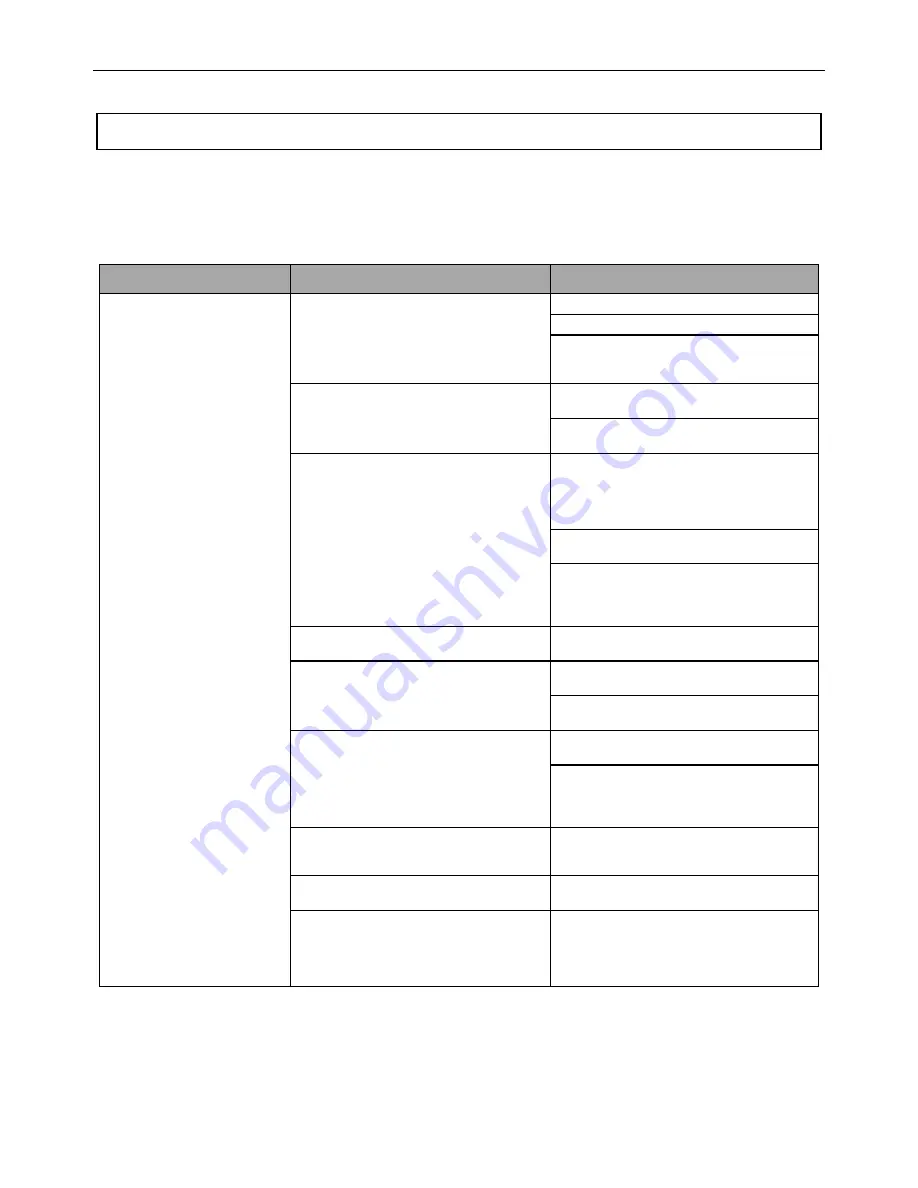
Instruction and Operation Manual
SA-07-11-37 Rev Orig
27
Jan 2009
Pump Mechanical Seals
The following table contains troubleshooting procedures for units equipped with a single seal. The information
also is applicable to single seal with throttle bushing, double and tandem seal units. Repair procedures for
mechanical seals are listed in the maintenance section of this manual.
Table 2. Pump Mechanical Seals
TROUBLE
POSSIBLE CAUSE
INVESTIGATIVE/CORRECTIVE ACTION
Sudden increase in seal
leakage.
Internal boiling or instability due to pump
operation below minimum flow for smooth
operation, causing vibration and bouncing of
seal face.
Increase flow rate.
Provide a cool seal flush.
Bleed vapor in seal cavity through port 6. A
bypass from port 6 back to the supply tank may
be required.
Loss of suction or severe cavitation due to
low NPSH, causing seal damage from lack of
lubrication.
Install a double seal if loss of suction cannot be
prevented.
Correct low NPSH condition. The installation
of an inducer may be required.
Seal icing on low temperature pumps or icing
when handling fluids which vaporize at a
temperature of less than 32
o
F. at atmospheric
pressure.
Inject Iso-Hexane, Methanol or Acetone (or a
similar compatible fluid which will not freeze at
pump temperature) above single seal drain
port 2 or 7 to prevent ice formation on
atmospheric side of seal during startup.
Use single seal with throttle bushing and purge
of dry nitrogen gas.
Install double or tandem seal if ice is caused by
water in process fluid, or supply external seal
flush of compatible fluid which does not contain
water.
Worn or damaged seal.
Disassemble seal and rebuild or replace per
instructions in maintenance section.
Solid particles in seal cavity or seal spring
area (seal faces usually have rough
scratched appearance).
Inspect for clogged integral centrifugal
separator orifice. Clean orifice if necessary.
Supply external clean seal flush or double seal
if particles cannot be removed by separator.
Seal stationary face spring action is rough
and sticky.
If parts are corroded, replace with parts made
from compatible materials.
If formation of solids causes sticky seal,
analyze fluid properties. Use external seal
flush, a double or tandem seal arrangement, or
apply an inert gas purge.
Wear pattern on seal rotating faces not
uniform.
Lightly lap surfaces of shaft sleeve and
impeller hub which contact rotating seal face to
remove high spots. Install new seal faces.
Wear pattern on stationary face smooth but
not uniform.
Replace seal.
Seal rotating face cracked or broken. May be
caused by damage at assembly or thermal
shock caused by (1) seal running dry, or (2)
rotating face spinning on shaft, or (3) loss
and recovery of buffer fluid
Prevent loss of pump suction or supply
continuous external seal flush.