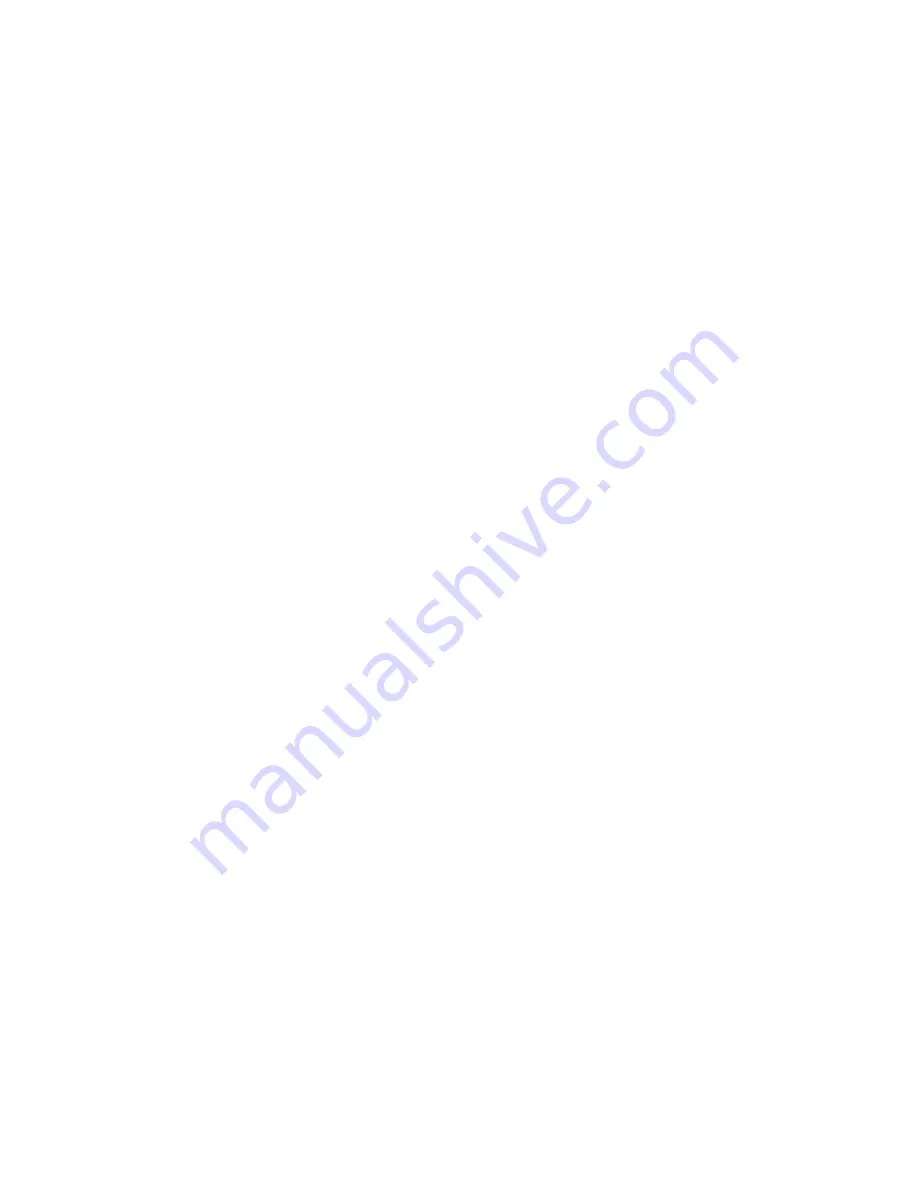
Section 1
SAFETY
3
supplying respirators or other breathing air utiliza-
tion equipment and
DO NOT
discharge air from
these systems into unventilated or other confined
areas.
C.
Operate the compressor only in open or ade-
quately ventilated areas.
D.
Locate the compressor or provide a remote inlet
so that it is not likely to ingest exhaust fumes or
other toxic, noxious or corrosive fumes or sub-
stances.
E.
Coolants and lubricants used in this compressor
are typical of the industry. Care should be taken to
avoid accidental ingestion and/or skin contact. In
the event of ingestion, seek medical treatment
promptly. Wash with soap and water in the event of
skin contact. Consult Material Safety Data Sheet for
information pertaining to fluid of fill.
F.
Wear goggles or a full face shield when adding
antifreeze compound to air line anti-icer systems.
G.
If air line anti-icer system antifreeze compound
enters the eyes or if fumes irritate the eyes, they
should be washed with large quantities of clean
water for fifteen minutes. A physician, preferably an
eye specialist, should be contacted immediately.
H. DO NOT
store air line anti-icer system antifreeze
compound in confined areas.
I.
The antifreeze compound used in air line
antifreeze systems contains methanol and is toxic,
harmful or fatal if swallowed. Avoid contact with the
skin or eyes and avoid breathing the fumes. If swal-
lowed, induce vomiting by administering a table-
spoon of salt, in each glass of clean, warm water
until vomit is clear, then administer two teaspoons
of baking soda in a glass of clean water. Have
patient lay down and cover eyes to exclude light.
Call a physician immediately.
1.8 ELECTRICAL SHOCK
A.
This compressor should be installed and main-
tained in full compliance with all applicable Federal,
State and Local codes, standards and regulations,
including those of the National Electrical Code, and
also including those relative to equipment ground-
ing conductors, and only by personnel that are
trained, qualified and delegated to do so.
B.
Keep all parts of the body and any hand-held
tools or other conductive objects away from
exposed live parts of electrical system. Maintain dry
footing, stand on insulating surfaces and
DO NOT
contact any other portion of the compressor when
making adjustments or repairs to exposed live parts
of the electrical system. Make all such adjustments
or repairs with one hand only, so as to minimize the
possibility of creating a current path through the
heart.
C.
Attempt repairs in clean, dry and well lighted and
ventilated areas only.
D. DO NOT
leave the compressor unattended with
open electrical enclosures. If necessary to do so,
then disconnect, lock out and tag all power at
source so others will not inadvertently restore
power.
E.
Disconnect, lock out, and tag all power at source
prior to attempting repairs or adjustments to rotating
machinery and prior to handling any ungrounded
conductors.
1.9 LIFTING
A.
If the compressor is provided with a lifting bail,
then lift by the bail provided. If no bail is provided,
then lift by sling. Compressors to be air-lifted by hel-
icopter must not be supported by the lifting bail but
by slings instead. In any event, lift and/or handle
only in full compliance with OSHA standards 29
CFR 1910 subpart N and/or any applicable Federal,
State, and Local codes, standards and regulations.
B.
Inspect points of attachment for cracked welds
and for cracked, bent, corroded or otherwise
degraded members and for loose bolts or nuts prior
to lifting.
C.
Make sure entire lifting, rigging and supporting
structure has been inspected, is in good condition
and has a rated capacity of at least the weight of
the compressor. If you are unsure of the weight,
then weigh compressor before lifting.
D.
Make sure lifting hook has a functional safety
latch or equivalent, and is fully engaged and latched
on the bail or slings.
E.
Use guide ropes or equivalent to prevent twisting
or swinging of the compressor once it has been lift-
ed clear of the ground.
F. DO NOT
attempt to lift in high winds.
G.
Keep all personnel out from under and away
from the compressor whenever it is suspended.
H.
Lift compressor no higher than necessary.
I.
Keep lift operator in constant attendance whenev-
er compressor is suspended.
J.
Set compressor down only on a level surface
capable of safely supporting at least its weight and
its loading unit.
K.
When moving the compressor by forklift truck,
utilize fork pockets if provided. Otherwise, utilize
Summary of Contents for LS-120 series
Page 16: ...Section 2 DESCRIPTION 10 Figure 2 5 Control System ...
Page 28: ...NOTES 22 ...
Page 43: ...Section 7 MAINTENANCE 37 Figure 7 8 Piping and Instrumentation Diagram Standard ...
Page 44: ...Section 7 MAINTENANCE 38 Figure 7 9 Piping and Instrumentation Diagram Supervisor Controller ...
Page 48: ...NOTES 42 ...
Page 51: ...Section 9 ILLUSTRATIONS AND PARTS LIST 45 NOTES ...
Page 60: ...Section 9 ILLUSTRATIONS AND PARTS LIST 54 9 5 AIR INLET SYSTEM LS 120 ...
Page 62: ...Section 9 ILLUSTRATIONS AND PARTS LIST 56 9 6 AIR INLET SYSTEM LS 160 AIR COOLED ...
Page 64: ...Section 9 ILLUSTRATIONS AND PARTS LIST 58 9 7 AIR INLET SYSTEM LS 160 WATER COOLED ...
Page 66: ...Section 9 ILLUSTRATIONS AND PARTS LIST 60 9 8 COOLING AND LUBRICATION SYSTEM AIR COOLED ...
Page 68: ...Section 9 ILLUSTRATIONS AND PARTS LIST 62 9 8 COOLING AND LUBRICATION SYSTEM AIR COOLED ...
Page 80: ...Section 9 ILLUSTRATIONS AND PARTS LIST 74 9 11 COOLER ASSEMBLY AIR COOLED ...
Page 82: ...Section 9 ILLUSTRATIONS AND PARTS LIST 76 9 11 COOLER ASSEMBLY AIR COOLED ...
Page 84: ...Section 9 ILLUSTRATIONS AND PARTS LIST 78 9 12 COMPRESSOR DISCHARGE SYSTEM AIR COOLED ...
Page 86: ...Section 9 ILLUSTRATIONS AND PARTS LIST 80 9 12 COMPRESSOR DISCHARGE SYSTEM AIR COOLED ...
Page 88: ...Section 9 ILLUSTRATIONS AND PARTS LIST 82 9 12 COMPRESSOR DISCHARGE SYSTEM AIR COOLED ...
Page 90: ...Section 9 ILLUSTRATIONS AND PARTS LIST 84 9 13 COMPRESSOR DISCHARGE SYSTEM WATER COOLED ...
Page 92: ...Section 9 ILLUSTRATIONS AND PARTS LIST 86 9 13 COMPRESSOR DISCHARGE SYSTEM WATER COOLED ...
Page 94: ...Section 9 ILLUSTRATIONS AND PARTS LIST 88 9 13 COMPRESSOR DISCHARGE SYSTEM WATER COOLED ...
Page 96: ...Section 9 ILLUSTRATIONS AND PARTS LIST 90 9 14 CONTROL SYSTEM LS 120 SUPERVISOR CONTROLLER ...
Page 98: ...Section 9 ILLUSTRATIONS AND PARTS LIST 92 9 15 CONTROL SYSTEM LS 120 ELECTRO MECHANICAL ...
Page 100: ...Section 9 ILLUSTRATIONS AND PARTS LIST 94 9 16 CONTROL SYSTEM LS 160 SUPERVISOR CONTROLLER ...
Page 102: ...Section 9 ILLUSTRATIONS AND PARTS LIST 96 9 17 CONTROL SYSTEM LS 160 ELECTRO MECHANICAL ...
Page 104: ...Section 9 ILLUSTRATIONS AND PARTS LIST 98 9 18 INSTRUMENT PANEL ELECTRO MECHANICAL ...
Page 108: ...Section 9 ILLUSTRATIONS AND PARTS LIST 102 9 20 ELECTRICAL BOX ELECTRO MECHANICAL ...
Page 110: ...Section 9 ILLUSTRATIONS AND PARTS LIST 104 9 21 ELECTRICAL BOX SUPERVISOR CONTROLLER ...
Page 116: ...Section 9 ILLUSTRATIONS AND PARTS LIST 110 9 24 CANOPY WATER COOLED 40 75HP 37 56KW ...
Page 118: ...Section 9 ILLUSTRATIONS AND PARTS LIST 112 9 25 CANOPY WATER COOLED LS 160 100HP 75KW ...
Page 120: ...Section 9 ILLUSTRATIONS AND PARTS LIST 114 9 26 DECAL GROUP ...
Page 122: ...Section 9 ILLUSTRATIONS AND PARTS LIST 116 9 26 DECAL GROUP ...
Page 124: ...Section 9 ILLUSTRATIONS AND PARTS LIST 118 9 26 DECAL GROUP ...
Page 128: ......
Page 129: ......