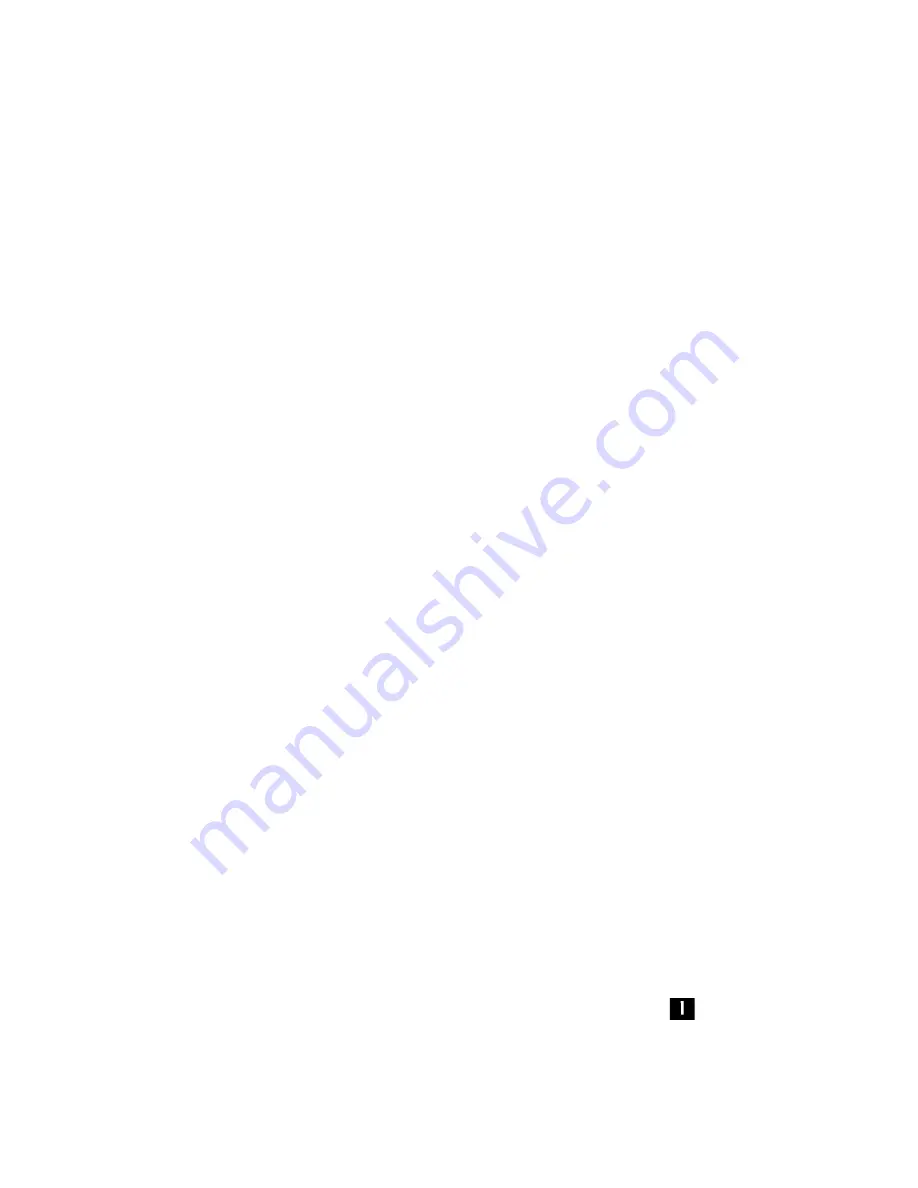
Section 2
DESCRIPTION
11
guidelines apply to all Series 12 & 16 Series com-
pressors. For explanatory purposes this description
will apply to a compressor with an operating pres-
sure range of 125 to 135 psig (8.6 to 9.3 bar). A
compressor with any other pressure range would
operate in the same manner excepting stated pres-
sures.
START - 0 TO 50 PSIG (0 TO 3.5 BAR)
When the compressor START button is depressed,
the sump pressure will quickly rise from 0 to 50 psig
(0 to 3.5 bar). During this period both the pressure
regulator and the solenoid valve are closed, the
inlet valve is fully open due to inlet air flow, and the
compressor pumps at full rated capacity. The rising
compressor air pressure is isolated from the service
line in this phase by the minimum pressure valve,
set at approximately 50 psig (3.5 bar).
NORMAL OPERATING MODE - 50 TO 125 PSIG
(3.5 TO 8.6 BAR)
When the pressure air rises above 50 psig (3.5 bar),
the minimum pressure/check valve opens and
delivers compressed air to the service line. From
this point on, the line air pressure is continually
monitored by a line pressure gauge and a pressure
switch usually set at 135 psig (9.3 bar). The pres-
sure regulator and the solenoid valve remain closed
during this phase. The inlet valve remains fully open
for maximum capacity.
MODULATING MODE - 125 TO 135 PSIG (8.6 TO
9.3 BAR)
If less than the rated capacity of compressed air is
being used, the service line pressure will rise above
125 psig (8.6 bar). The pressure regulator valve
gradually opens, applying air pressure through the
control line to the inlet valve piston. This causes the
inlet valve to partially close reducing the amount of
air entering the compressor until it matches the
amount of air being used. The control system func-
tions continually in this manner, between the limits
of 125 to 135 psig (8.6 to 9.3 bar), in response to
varying demands from the service line.
The pressure regulator has an orifice which vents a
small amount of air to the atmosphere when the
pressure regulator controls the inlet valve. The ori-
fice also bleeds any accumulated moisture from the
control lines.
UNLOAD - IN EXCESS OF 135 PSIG (9.3 BAR)
LINE PRESSURE
When no air is being used,the service line pressure
rises to the setting (cut-out pressure) of the pres-
sure switch. the pressure switch opens, interrupting
the electrical power to the solenoid valve. At this
time, the solenoid valve allows dry sump tank air
pressure or service air pressure through a shuttle
valve to be applied directly to the inlet valve piston
and keep it closed. Simultaneously, the solenoid
valve sends a pneumatic signal to the blowdown
valve. The blowdown valve opens the sump to the
compressor intake reducing the sump pressure to
approximately 20 psig (1.4 bar). The check valve in
the air service line pressure prevents line pressure
from returning to the sump.
When the line pressure drops to the low setting
(cut-in pressure; usually 100 psig [6.9 bar] on low
pressure [“L”] compressors and 125 psig [8.6 bar]
on high pressure [“H”] compressors, 150 psig [10.3
bar] on [“HH”] compressors, 175 psig [12.0 bar]
[“XH”]), the pressure switch closes, re-energizing
the 3-way solenoid valve and allowing the blow-
down valve to close. The re-energized solenoid
valve again prevents pressure from reaching the
inlet valve. The inlet valve is fully open and the com-
pressor delivers full rated capacity. Should the pres-
sure begin to rise, the pressure regulator will
resume its normal function as previously described.
To accommodate varied periods of time when there
are not any air requirements, “Dual-Control” is uti-
lized. This feature allows you to set the compressor
in an automatic position whereby the compressor
will shut down when no compressed air require-
ment is present and restart as compressed air is
needed.
2.7 CONTROL SYSTEM, FUNCTIONAL DESCRIP-
TION- SUPERVISOR CONTROLLER™
. The purpose of the compres-
sor Control System is to regulate the amount of air
being compressed to match the amount of com-
pressed air being used. The Capacity control sys-
tem consists of a solenoid valve, regulator valve
and an inlet valve. The functional description of the
Control System is described below in four distinct
phases of operation. The following description text
applies to all 120 and 160 series compressors with
optional Supervisor Controller. For explanatory pur-
poses, this description will apply to a compressor
with an operating range of 100 to 110 psig (6.9 to
7.6 bar). A compressor with any other pressure
range would operate in the same manner except
stated pressures.
START MODE - 0 TO 50 PSIG (0 TO 3.5 BAR)
When the compressor "
" (
START
) pad is
depressed, the sump pressure will quickly rise from
0 to 50 psig (0 - 3.4 bar). The compressor initially
starts unloaded, then switches to full load when full
Summary of Contents for LS-120 series
Page 16: ...Section 2 DESCRIPTION 10 Figure 2 5 Control System ...
Page 28: ...NOTES 22 ...
Page 43: ...Section 7 MAINTENANCE 37 Figure 7 8 Piping and Instrumentation Diagram Standard ...
Page 44: ...Section 7 MAINTENANCE 38 Figure 7 9 Piping and Instrumentation Diagram Supervisor Controller ...
Page 48: ...NOTES 42 ...
Page 51: ...Section 9 ILLUSTRATIONS AND PARTS LIST 45 NOTES ...
Page 60: ...Section 9 ILLUSTRATIONS AND PARTS LIST 54 9 5 AIR INLET SYSTEM LS 120 ...
Page 62: ...Section 9 ILLUSTRATIONS AND PARTS LIST 56 9 6 AIR INLET SYSTEM LS 160 AIR COOLED ...
Page 64: ...Section 9 ILLUSTRATIONS AND PARTS LIST 58 9 7 AIR INLET SYSTEM LS 160 WATER COOLED ...
Page 66: ...Section 9 ILLUSTRATIONS AND PARTS LIST 60 9 8 COOLING AND LUBRICATION SYSTEM AIR COOLED ...
Page 68: ...Section 9 ILLUSTRATIONS AND PARTS LIST 62 9 8 COOLING AND LUBRICATION SYSTEM AIR COOLED ...
Page 80: ...Section 9 ILLUSTRATIONS AND PARTS LIST 74 9 11 COOLER ASSEMBLY AIR COOLED ...
Page 82: ...Section 9 ILLUSTRATIONS AND PARTS LIST 76 9 11 COOLER ASSEMBLY AIR COOLED ...
Page 84: ...Section 9 ILLUSTRATIONS AND PARTS LIST 78 9 12 COMPRESSOR DISCHARGE SYSTEM AIR COOLED ...
Page 86: ...Section 9 ILLUSTRATIONS AND PARTS LIST 80 9 12 COMPRESSOR DISCHARGE SYSTEM AIR COOLED ...
Page 88: ...Section 9 ILLUSTRATIONS AND PARTS LIST 82 9 12 COMPRESSOR DISCHARGE SYSTEM AIR COOLED ...
Page 90: ...Section 9 ILLUSTRATIONS AND PARTS LIST 84 9 13 COMPRESSOR DISCHARGE SYSTEM WATER COOLED ...
Page 92: ...Section 9 ILLUSTRATIONS AND PARTS LIST 86 9 13 COMPRESSOR DISCHARGE SYSTEM WATER COOLED ...
Page 94: ...Section 9 ILLUSTRATIONS AND PARTS LIST 88 9 13 COMPRESSOR DISCHARGE SYSTEM WATER COOLED ...
Page 96: ...Section 9 ILLUSTRATIONS AND PARTS LIST 90 9 14 CONTROL SYSTEM LS 120 SUPERVISOR CONTROLLER ...
Page 98: ...Section 9 ILLUSTRATIONS AND PARTS LIST 92 9 15 CONTROL SYSTEM LS 120 ELECTRO MECHANICAL ...
Page 100: ...Section 9 ILLUSTRATIONS AND PARTS LIST 94 9 16 CONTROL SYSTEM LS 160 SUPERVISOR CONTROLLER ...
Page 102: ...Section 9 ILLUSTRATIONS AND PARTS LIST 96 9 17 CONTROL SYSTEM LS 160 ELECTRO MECHANICAL ...
Page 104: ...Section 9 ILLUSTRATIONS AND PARTS LIST 98 9 18 INSTRUMENT PANEL ELECTRO MECHANICAL ...
Page 108: ...Section 9 ILLUSTRATIONS AND PARTS LIST 102 9 20 ELECTRICAL BOX ELECTRO MECHANICAL ...
Page 110: ...Section 9 ILLUSTRATIONS AND PARTS LIST 104 9 21 ELECTRICAL BOX SUPERVISOR CONTROLLER ...
Page 116: ...Section 9 ILLUSTRATIONS AND PARTS LIST 110 9 24 CANOPY WATER COOLED 40 75HP 37 56KW ...
Page 118: ...Section 9 ILLUSTRATIONS AND PARTS LIST 112 9 25 CANOPY WATER COOLED LS 160 100HP 75KW ...
Page 120: ...Section 9 ILLUSTRATIONS AND PARTS LIST 114 9 26 DECAL GROUP ...
Page 122: ...Section 9 ILLUSTRATIONS AND PARTS LIST 116 9 26 DECAL GROUP ...
Page 124: ...Section 9 ILLUSTRATIONS AND PARTS LIST 118 9 26 DECAL GROUP ...
Page 128: ......
Page 129: ......