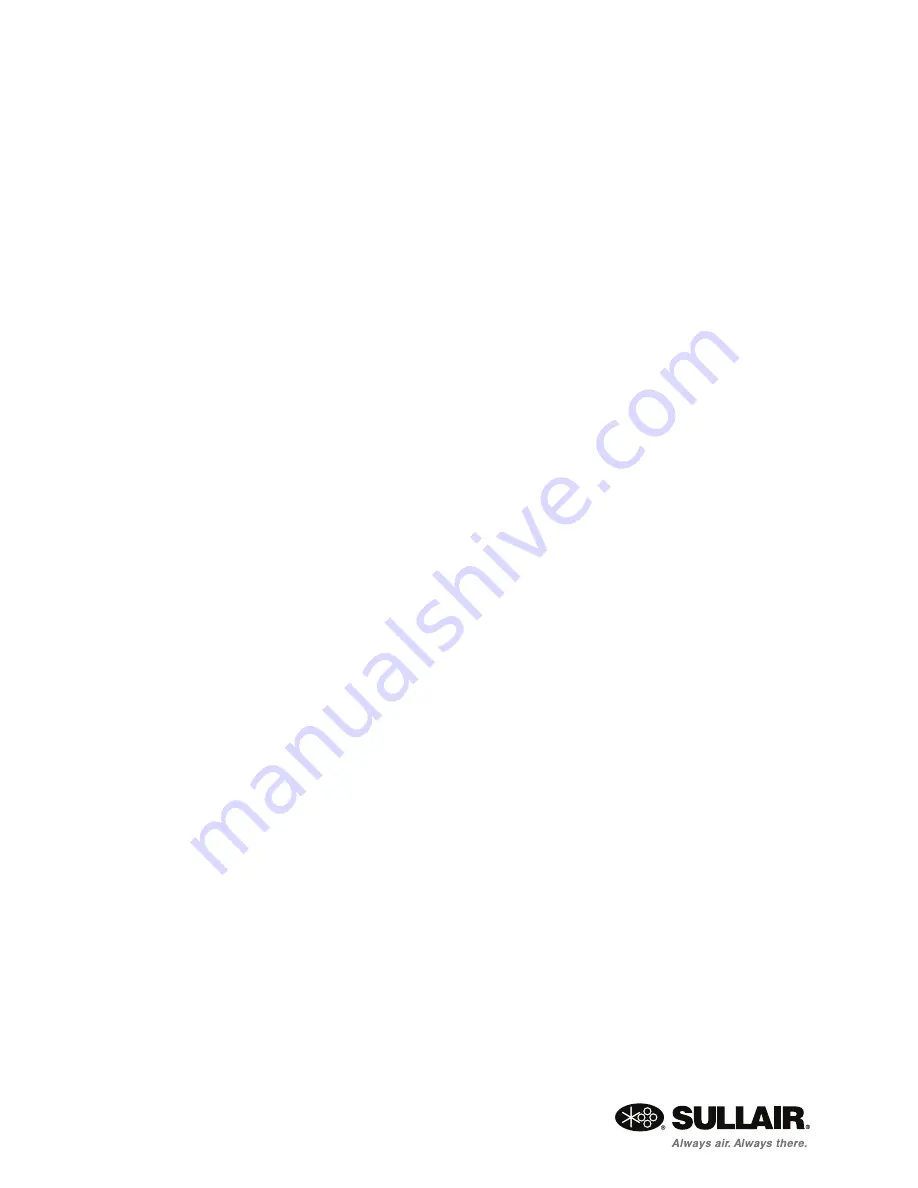
SECTION 1
8
inside diameter to reduce pressure in case of
hose failure.
D.
Flow-limiting valves are listed by pipe size and
flow-rated. Select appropriate valves accordingly,
in accordance with their manufacturer's recom-
mendations.
E. DO NOT
use air tools that are rated below the
maximum rating of the compressor. Select air
tools, air hoses, pipes, valves, filters and other
fittings accordingly.
DO NOT
exceed manufac-
turer's rated safe operating pressures for these
items.
F.
Secure all hose connections by wire, chain or
other suitable retaining device to prevent tools or
hose ends from being accidentally disconnected
and expelled.
G.
Open fluid filler cap only when compressor is not
running and is not pressurized. Shut down the
compressor and bleed the receiver tank to zero
internal pressure before removing the cap.
H.
Vent all internal pressure prior to opening any
line, fitting, hose, valve, drain plug, connection or
other component, such as filters and line oilers,
and before attempting to refill optional air line
anti-icer systems with antifreeze compound.
I.
Keep personnel out of line with and away from
the discharge opening of hoses or tools or other
points of compressed air discharge.
J. DO NOT
use air at pressures higher than 2.1 bar
for cleaning purposes, and then only with effec-
tive chip guarding and personal protective equip-
ment per OSHA Standard 29 CFR 1910.242 (b)
and/or any applicable Federal, State, and Local
codes, standards and regulations.
K. DO NOT
engage in horseplay with air hoses as
death or serious injury may result.
1.4
FIRE AND EXPLOSION
A.
Clean up spills of lubricant or other combustible
substances immediately, if such spills occur.
B.
Shut off the compressor and allow it to cool.
Then keep sparks, flames and other sources of
ignition away and
DO NOT
permit smoking in the
vicinity when checking or adding lubricant or
when refilling air line anti-icer systems with anti-
freeze compound.
C. DO NOT
permit fluids, including air line anti-icer
system antifreeze compound or fluid film, to
accumulate on, under or around acoustical mate-
rial, or on any external surfaces of the air com-
pressor. Wipe down using an aqueous industrial
cleaner or steam clean as required. If necessary,
remove acoustical material, clean all surfaces
and then replace acoustical material. Any acous-
tical material with a protective covering that has
been torn or punctured should be replaced
immediately to prevent accumulation of liquids or
fluid film within the material.
DO NOT
use flam-
mable solvents for cleaning purposes.
D.
Disconnect and lock out all power at source prior
to attempting any repairs or cleaning of the com-
pressor or of the inside of the enclosure, if any.
E.
Keep electrical wiring, including all terminals and
pressure connectors in good condition. Replace
any wiring that has cracked, cut, abraded or oth-
erwise degraded insulation, or terminals that are
worn, discolored or corroded. Keep all terminals
and pressure connectors clean and tight.
F.
Keep grounded and/or conductive objects such
as tools away from exposed live electrical parts
such as terminals to avoid arcing which might
serve as a source of ignition.
G.
Remove any acoustical material or other material
that may be damaged by heat or that may sup-
port combustion and is in close proximity, prior to
attempting weld repairs.
H.
Keep suitable fully charged Class BC or ABC fire
extinguisher or extinguishers nearby when ser-
vicing and operating the compressor.
I.
Keep oily rags, trash, leaves, litter or other com-
bustibles out of and away from the compressor.
J. DO NOT
operate the compressor without proper
flow of cooling air or water or with inadequate
flow of lubricant or with degraded lubricant.
K. DO NOT
attempt to operate the compressor in
any classification of hazardous environment
unless the compressor has been specially
designed and manufactured for that duty.
1.5
MOVING PARTS
A.
Keep hands, arms and other parts of the body
and clothing away from couplings, belts, pulleys,
fans and other moving parts.
B. DO NOT
attempt to operate the compressor with
the fan, coupling or other guards removed.
Summary of Contents for ES-6 10H
Page 1: ......
Page 6: ...TABLE OF CONTENTS...
Page 12: ...NOTES 12...
Page 18: ...18 NOTES...
Page 23: ...23 NOTES...
Page 26: ...ES 6 USER MANUAL SECTION 3 26 3 6 IDENTIFICATION ES 6 STANDARD WITH ENCLOSURE 02250172 316 R00...
Page 52: ...ES 6 USER MANUAL SECTION 3 52 3 19 WIRING DIAGRAM DUAL CONTROL WYE DELTA 02250058 093 R04...
Page 54: ...ES 6 USER MANUAL SECTION 3 54 3 20 WIRING DIAGRAM SRS 25 100 115 230V 1 60 02250171 733 R00...
Page 56: ...ES 6 USER MANUAL SECTION 3 56 3 21 WIRING DIAGRAM SRS 9 18 220 240V 1 50 02250171 738 R00...
Page 58: ...ES 6 USER MANUAL SECTION 3 58 3 22 WIRING DIAGRAM SRS 24 30 220 240V 1 50 02250171 739 R00...
Page 60: ...60 NOTES...
Page 78: ...78 NOTES...
Page 82: ...82 NOTES...
Page 83: ...NOTES 83...
Page 84: ......