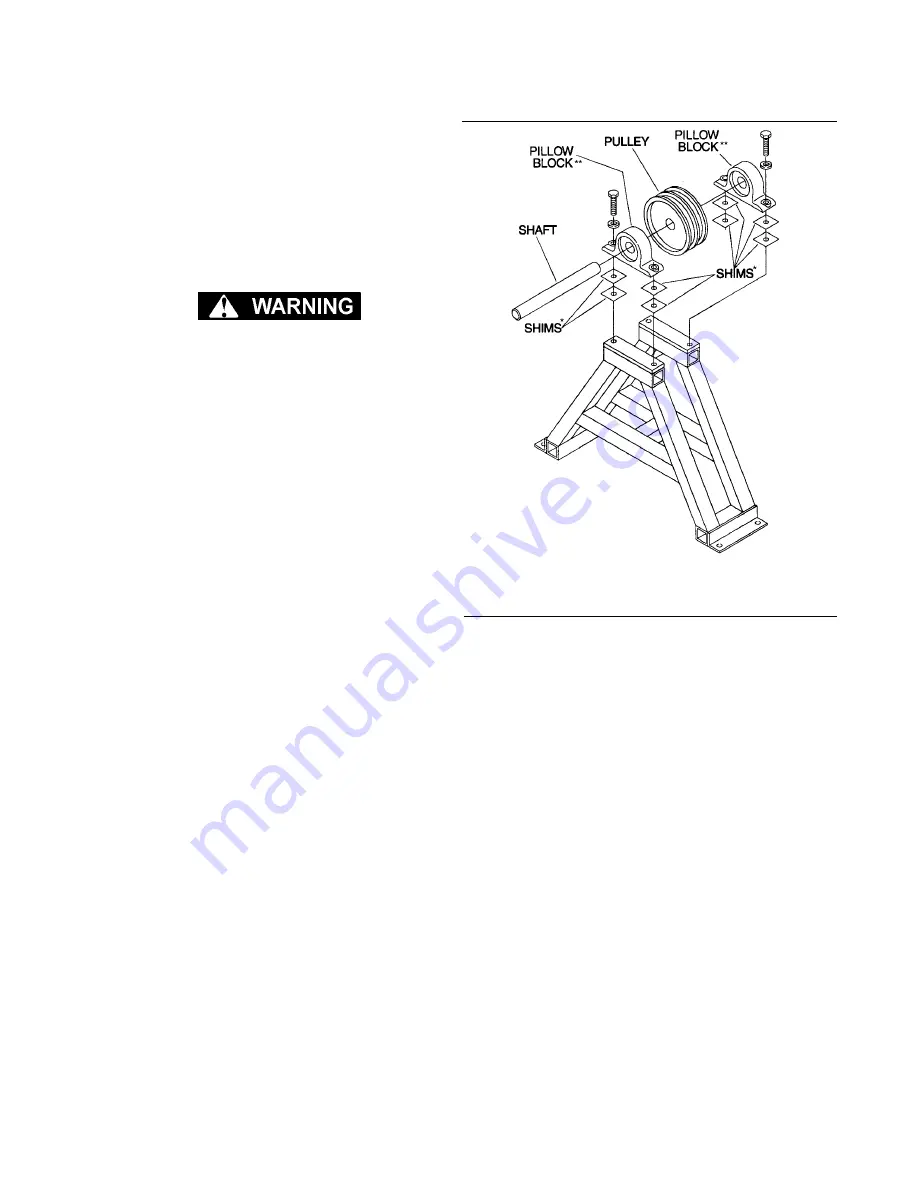
Section 7
MAINTENANCE
31
7.1 GENERAL
As you proceed to study this section, it will be easy
to see that maintenance for the air compressor is
quite minimal. The controller monitors the status of
the air and oil filters. When maintenance to either
device is required, the controller will display the
appropriate maintenance message. For engine
maintenance requirements, refer to the Engine
Operator’s Manual for a detailed description of
service instructions.
DO NOT remove caps, plugs, and/or other com-
ponents when compressor is running or pres-
surized.
Stop compressor and relieve all internal pres-
sure before doing so.
7.2 DAILY OPERATION
Following a routine start, observe the controller dis-
play and local gauges to check that normal read-
ings have been made - previous records are very
helpful in determining the normalcy of the measure-
ments. These observations should be made during
all expected modes of operation (i.e. full load, no-
load, different line pressures, etc.).
7.3 INITIAL MAINTENANCE AFTER 50 HOURS
OF OPERATION
Upon completion of the first 50 hours of operation,
a few maintenance requirements are needed to rid
the system of any foreign materials which may have
accumulated during assembly:
1. Change the compressor oil filter element.
2. Clean the control line filter element.
3. Check/replace the sump breather element.
4. Check/clean condensate drain valves and
screens. Verify auto-drain function.
7.4 MAINTENANCE EVERY 250 HOURS
Perform the following after every 250 hours of
operation:
1. Check the battery level and fill with water if nec-
essary.
2. Change the engine oil and oil filter.
3. Check fan belt tension.
4. Clean the heat exchangers and radiator exterior.
Depending on how contaminated the atmosphere
may be, more frequent cooler and radiator cleaning
may be necessary. To allow easier access to the
heat exchangers, remove the two long access
doors located on each side of the package.
Replace the access doors when complete.
5. Check the Engine Operator’s Manual for addi-
tional service requirements.
6. Check/clean condensate drain valves and
screens. Verify auto-drain function.
block bearings.
DO NOT
over-lubricate. Lubricate
only until a thin bead of fresh grease is visible at
seal lip.
7.5 MAINTENANCE EVERY 8000 HOURS OR
ONE YEAR OF OPERATION
The following items should be checked every 8000
hours of operation or one year, whichever comes
first, although service conditions such as relative
cleanliness of process air or quality of cooling medi-
um may require shorter inspection intervals.
1. Replace compressor oil and filter element.
2. Replace control line filter element.
3. Replace sump breather filter element.
4. Replace air filter element.
5. Check/clean condensate drain valves and
screens. Verify auto-drain function.
6. Measure and record vibration signatures on
compressor and gear box- optional.
Figure 7-1 Pillow Block Assembly
*Use the same shims to maintain alignment of fan. Fan
must be centered into shroud.
**Pillow block replacement P/N 02250120-842 (qty 2).
Summary of Contents for DE-18
Page 6: ...NOTES...
Page 14: ...8 NOTES...
Page 18: ...12 NOTES...
Page 23: ...Section 4 COMPRESSOR SYSTEMS 17 Figure 4 4 Piping and Instrumentation Diagram...
Page 25: ...19 NOTES...
Page 26: ...Section 5 CONTROLLER 20 Figure 5 1 Control Panel...
Page 32: ...26 NOTES...
Page 36: ...30 NOTES...
Page 51: ...45 NOTES...