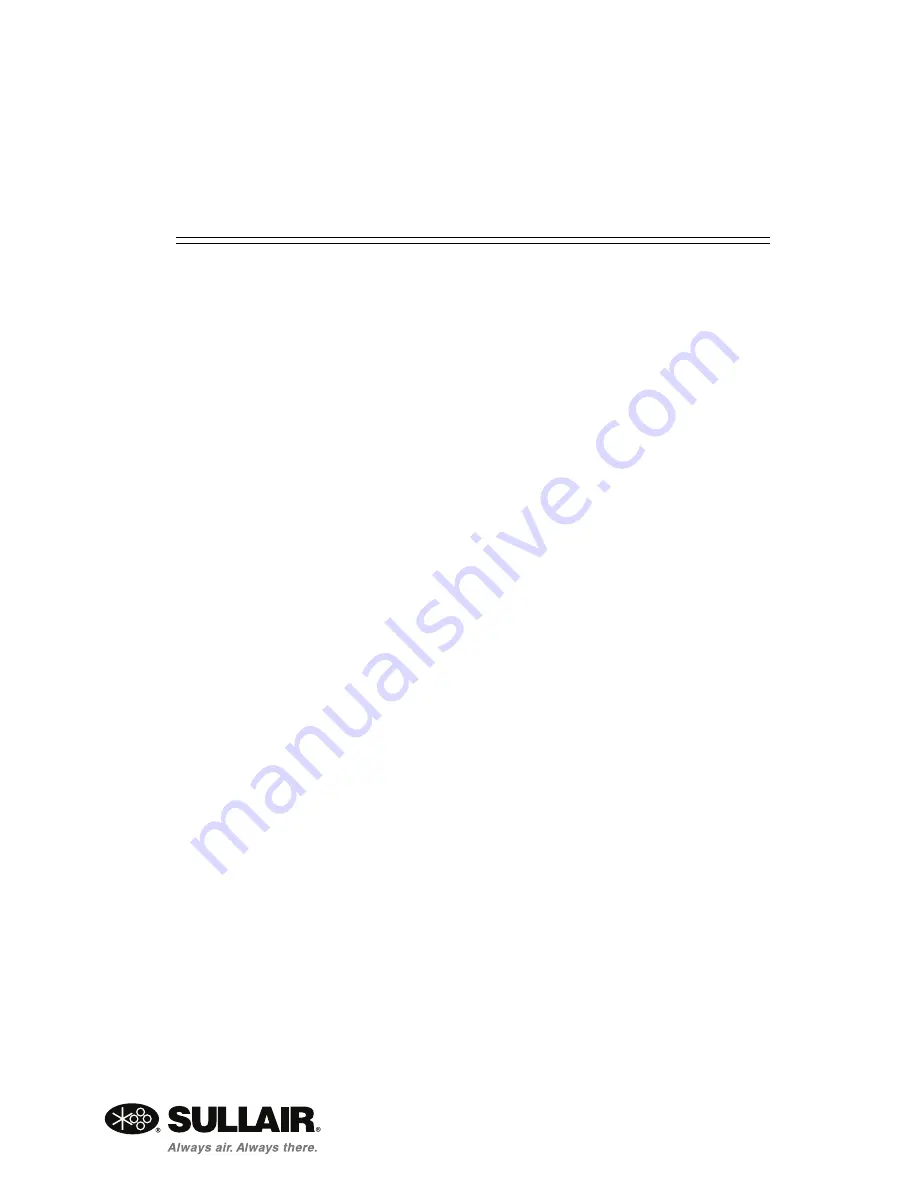
Section 7
75
DBP BLOWER PURGE HEATED DRYER
SYSTEM MAINTENANCE
7.1
WITH YOUR DRYER ONLINE
The following points must be verified at regular
intervals
• Daily, verify the regeneration heater outlet
temperature is correct and conforms to that
listed in
• Daily, verify the prefilter automatic drain is
functional.
• Once a week, verify the operating
sequence at vessel change over with that
previously described in
and
• Once a week, verify the adsorption, regen-
eration heating, cooling and vessel change
over times compared to that listed in
• Weekly, check the dryer, prefilter and after-
filter for excessive pressure drop.
7.2
MONTHLY INSPECTIONS
• Verify the system is leak free.
• Verify the current draw of the regeneration
heater.
• Verify the operation of all pressure gauges,
temperature gauges, temperature switches
and the dewpoint indicator.
7.3
QUARTERLY INSPECTIONS
• Repeat all monthly inspections.
• Check the prefilter and afterfilter elements
for correct installation and excess dirt.
• Check for tightness of flange bolting espe-
cially where high temperatures occur.
7.4
YEARLY INSPECTIONS
• Replace seats and shaft seals on all butter-
fly valves.
• Replace seats and shaft seals on all ball
valves.
• Dismantle the double acting pneumatic
actuators. Inspect internal components for
visual signs of wear and replace parts as
necessary.
• Dismantle and inspect solenoid valve inter-
nal components for visual signs of wear.
Replace parts as necessary.
• Check the function of all temperature con-
trols.
7.5
DESICCANT CHANGE OUT
Depending on the air quality and service conditions,
the desiccant will last 4 to 5 years. Experience has
shown that the period may be even longer.
To change the desiccant, ensure the system is out of
service, locked out and de-pressurized. Remove the
plug from the desiccant drain ports to allow the
desiccant to fall from the vessel. At the end of this
procedure re-install the plug.
To load the new desiccant the plug on the fill ports on
the top head should be removed. Then install the
amount and type of desiccant listed in
in each vessel. Re-install the covers on the
desiccant fill ports.
Prior to placing the dryer in service all plugs and
flanges that were removed should be leak tested. If
any leaks occur they should be repaired and re
tested prior to placing the dryer in service.
7.6
FILTER ELEMENT CHANGE
OUT
The prefilter and afterfilter elements should be
replaced when the following guidelines are
exceeded.
• The differential pressure exceeds 5 PSIG.
• The operating service exceeds 4,500
hours.
• A period of one year is exceeded.
Summary of Contents for 1000-DBP
Page 5: ...TABLE OF CONTENTS SECTION 9 SPARE PARTS LIST 80 9 1 SPARE PARTS LIST ...
Page 6: ...TABLE OF CONTENTS ...
Page 8: ...8 NOTES ...
Page 14: ...14 NOTES ...
Page 18: ...18 NOTES ...
Page 20: ...20 NOTES ...
Page 24: ...DBP BLOWER PURGE HEATED DRYER SECTION 5 24 5 9 ID DBP 500 02250195 346 ...
Page 26: ...DBP BLOWER PURGE HEATED DRYER SECTION 5 26 5 10 ID DBP 650 02250195 347 ...
Page 28: ...DBP BLOWER PURGE HEATED DRYER SECTION 5 28 5 11 ID DBP 800 1000 02250195 348 ...
Page 30: ...DBP BLOWER PURGE HEATED DRYER SECTION 5 30 5 12 ID DBP 1250 1500 02250195 349 ...
Page 32: ...DBP BLOWER PURGE HEATED DRYER SECTION 5 32 5 13 ID DBP 2000 02250195 350 ...
Page 34: ...DBP BLOWER PURGE HEATED DRYER SECTION 5 34 5 14 ID DBP 2500 3000 02250195 351 ...
Page 36: ...DBP BLOWER PURGE HEATED DRYER SECTION 5 36 5 15 P I 02250195 361 ...
Page 38: ...DBP BLOWER PURGE HEATED DRYER SECTION 5 38 5 16 WD DBP 500 02250195 378 ...
Page 40: ...DBP BLOWER PURGE HEATED DRYER SECTION 5 40 5 17 WD DBP 650 02250195 379 ...
Page 42: ...DBP BLOWER PURGE HEATED DRYER SECTION 5 42 5 18 WD DBP 800 02250195 380 ...
Page 44: ...DBP BLOWER PURGE HEATED DRYER SECTION 5 44 5 19 WD DBP 1000 02250195 381 ...
Page 46: ...DBP BLOWER PURGE HEATED DRYER SECTION 5 46 5 20 WD DBP 1250 02250195 382 ...
Page 48: ...DBP BLOWER PURGE HEATED DRYER SECTION 5 48 5 21 WD DBP 1500 02250195 383 ...
Page 50: ...DBP BLOWER PURGE HEATED DRYER SECTION 5 50 5 22 WD DBP 2000 02250195 384 ...
Page 52: ...DBP BLOWER PURGE HEATED DRYER SECTION 5 52 5 23 WD DBP 2500 02250195 385 ...
Page 54: ...DBP BLOWER PURGE HEATED DRYER SECTION 5 54 5 24 WD DBP 3000 02250195 386 ...
Page 56: ...DBP BLOWER PURGE HEATED DRYER SECTION 5 56 5 25 WD DBP 3500 02250195 387 ...
Page 58: ...DBP BLOWER PURGE HEATED DRYER SECTION 5 58 5 26 WD DBP 4000 02250195 388 ...
Page 60: ...DBP BLOWER PURGE HEATED DRYER SECTION 5 60 5 27 WD DBP 5000 02250195 389 ...
Page 62: ...DBP BLOWER PURGE HEATED DRYER SECTION 5 62 5 28 WD DBP 6000 02250195 390 ...
Page 64: ...DBP BLOWER PURGE HEATED DRYER SECTION 5 64 5 29 WD DBP 7000 02250195 391 ...
Page 66: ...DBP BLOWER PURGE HEATED DRYER SECTION 5 66 5 30 WD DBP 8000 02250195 392 ...
Page 68: ...DBP BLOWER PURGE HEATED DRYER SECTION 5 68 5 31 WD DBP 9000 02250195 393 ...
Page 70: ...DBP BLOWER PURGE HEATED DRYER SECTION 5 70 5 32 WD DBP 10000 02250195 394 ...
Page 72: ...72 NOTES ...
Page 76: ...76 NOTES ...
Page 78: ...78 NOTES ...
Page 79: ...Section 9 79 DBP BLOWER PURGE HEATED DRYER SPARE PARTS LIST ...
Page 83: ...NOTES 83 ...