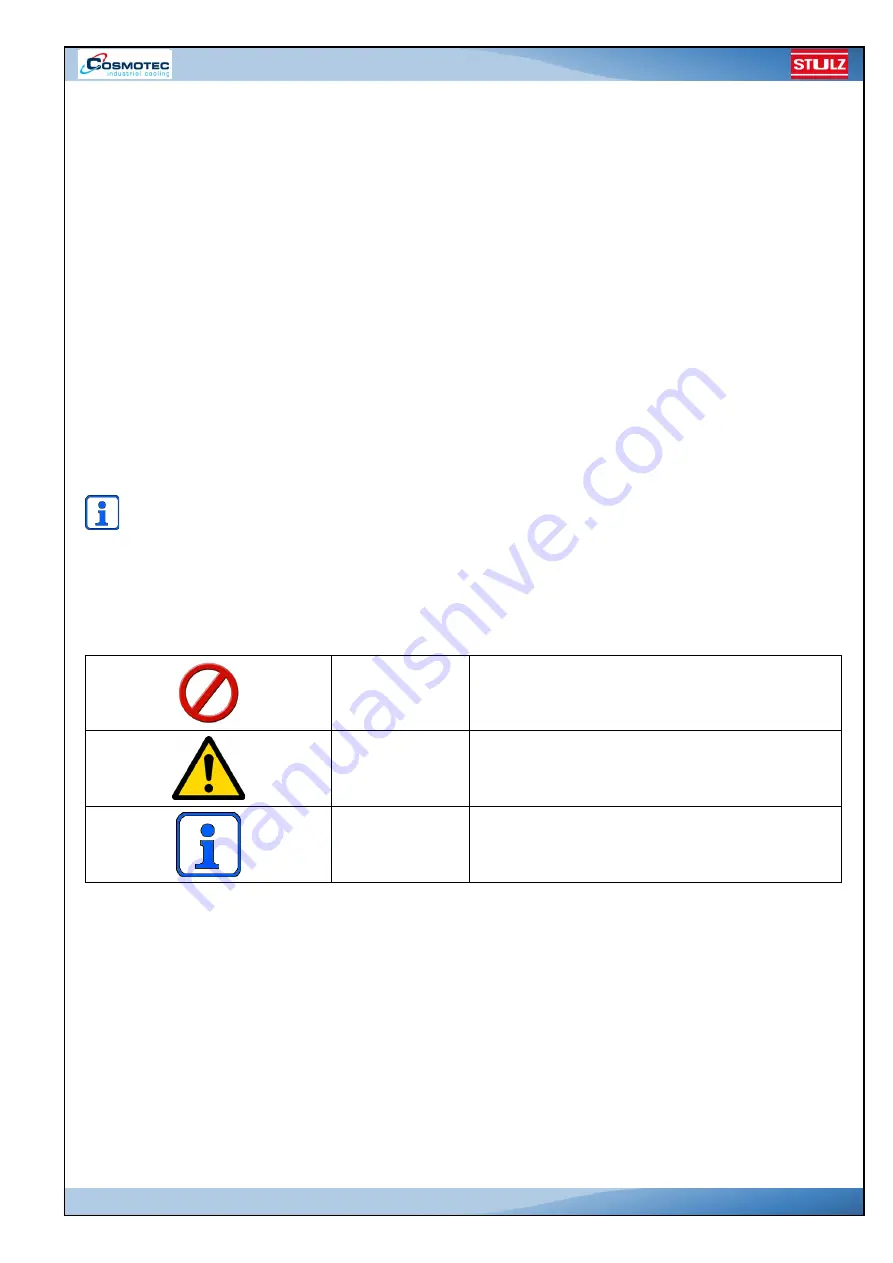
EN/
/0915/WLA Compact
/5
1.
Introduction
1.1.
General information
The units described in this manual belong to the vapour compression refrigerator system family that use chillers of
group 2, intended for water cooling. This manual contains safety operating instructions to be complied with during
installation, use, and maintenance. Therefore, read and comply with the instructions contained herein.
This manual is intended for the following professionals, who are considered authorised personnel:
The INSTALLER must check that the handling and installation of the chiller is performed according to the occupational
standards and instructions contained in this manual.
The OPERATOR must know and comply with the occupational standards and instructions contained in this manual
in order to use and adjust the chiller correctly.
MAINTENANCE TECHNICIANS (or service technicians) are authorised by the chiller manufacturer to commission
the unit, provide technical assistance, perform routine and special maintenance, and repairs.
Qualified personnel are those who, thanks to their training, education, experience and specific knowledge regarding
occupational standards, are authorised by the safety manager to perform the above mentioned activities.
The manufacturer declines any liability for improper use of the chiller, for any unauthorised
modifications applied, and for failure to comply with the instructions contained in this manual. The
occurrence of any of the above-mentioned conditions will make the product warranty immediately
void and null.
The customer must store this manual and make it available to the personnel in charge of installing,
running, and performing maintenance on the chiller.
1.2.
Symbols used in the manual
Danger
Danger of death or injury for the operator
Attention
Danger of damage to the equipment
Information
Important information, usage note
1.3.
Annexes
The following annexes are an integral part of this manual.
•
Manual part 2: consisting of water-refrigeration diagram, electrical diagram, and CE declaration of conformity;
•
electronic control manual (user version).
•
accessory (if available) manuals