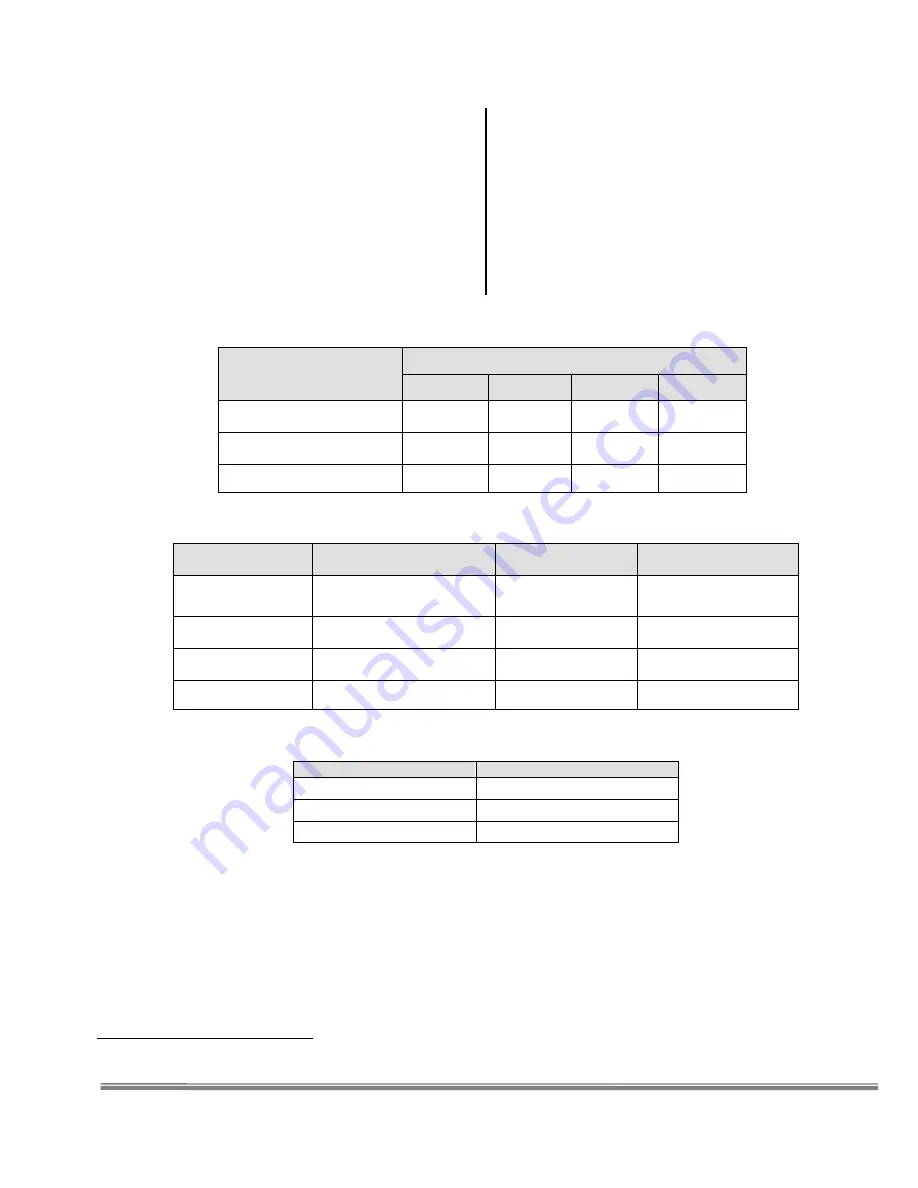
DEZ
S
ERIES
1000
I
NSTALLATION
,
O
PERATION AND
M
AINTENANCE
M
ANUAL
17
5.4.2 Lubrication & Bearings
(For motors with grease fittings only)
The lubricating ability of grease depends primarily on
the type of grease, the size of the bearing, the speed
at which the bearing operates and the severity of the
operating conditions. This ability can be lost over time.
The following steps will provide good results:
1. Use a high grade ball or roller bearing grease.
Consult the motor manufacturer’s nameplate, if
provided, for the recommended grease to use. If
none are listed, the recommended greases for
standard service conditions are Shell Dolium R,
Texaco Polystar, Amoco Rykon Premium #2 or
Chevron SRI#2.
2. Lubrication should be performed at the intervals
shown in the table below. These intervals are
based on average use. See nameplate on motor
for frame size and rated speed.
Table 1 - Blower Motor Lubrication Intervals
NEMA/(IEC) Frame Size
Rated Speed - RPM
3600
1800
1200
900
Up to 210 incl. (132)
5500 Hrs.
12000 Hrs. 18000 Hrs.
22000 Hrs.
Over 210 to 280 incl. (180)
3600 Hrs.
9500 Hrs.
15000 Hrs.
18000 Hrs.
Over 280
2200 Hrs.
1
7400 Hrs.
12000 Hrs.
15000 Hrs.
Table 2 - Service Conditions
Severity of Service
Ambient Temperature
Maximum
Atmospheric
Contamination
Type of Bearing
Standard
40
C
Clean, Little
Corrosion
Deep Groove Ball
Bearing
Severe
50
C
Moderate dirt,
Corrosion
Ball Thrust, Roller
Extreme
>50
C
1
or Class H
Insulation
Severe dirt, Abrasive
dust, Corrosion
All Bearings
Low Temperature
<-30
C
2
Table 3 - Lubrication Interval Multiplier
Severity of Service
Multiplier
Standard 1.0
Severe 0.5
Extreme 0.1
1
Special high temperature grease is recommended (Dow Corning DC44 or Darmex 707).
2
Special low temperature grease is recommended (Aeroshell 7).