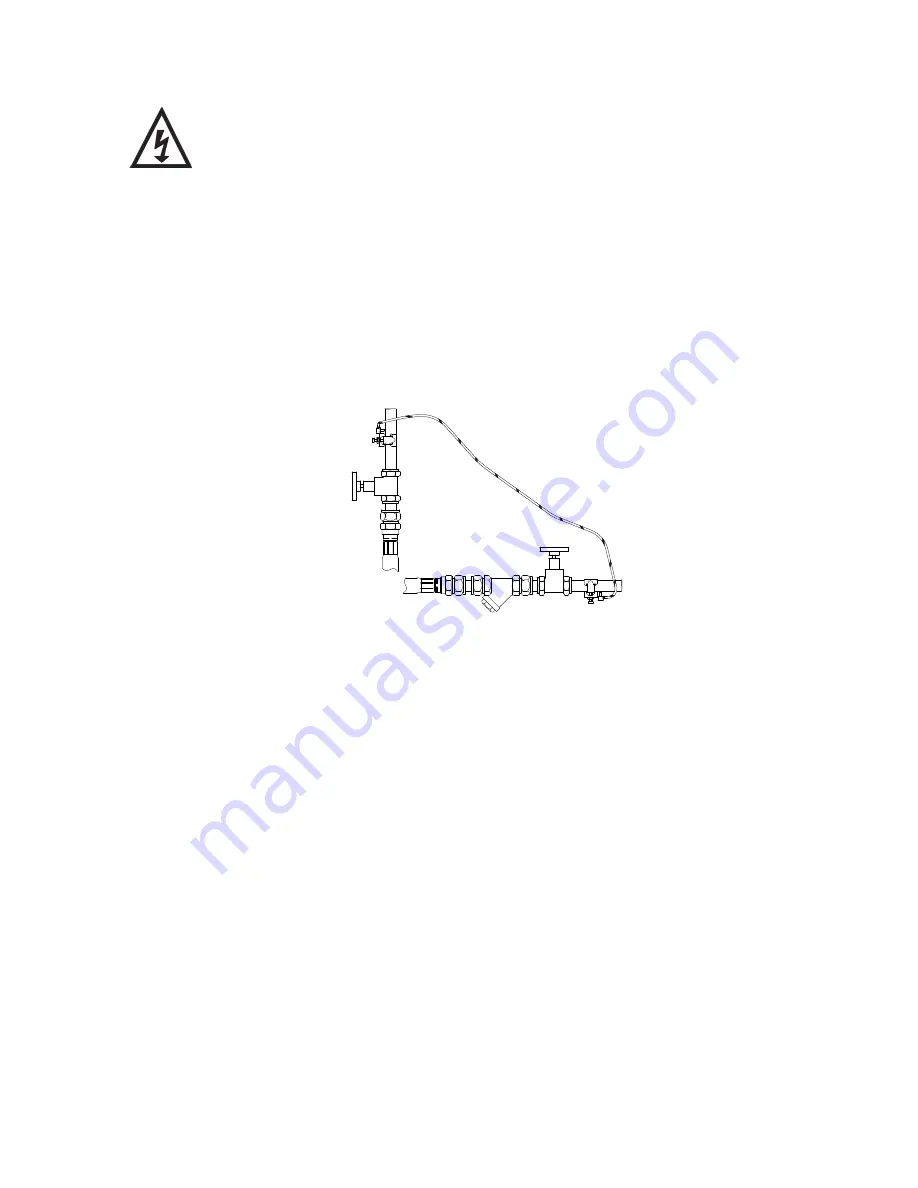
- 12 -
5 ELECTRICAL INSTALLATION / EARTHING
5.11
Regulations:
The electrical installation must be carried out in
accordance with the current national electrical regulations and
installed by a qualified person.
5.12
Safety:
In the interests of electrical safety a 30 mA residual current
device (
R.C.D. not supplied
) should be installed in the supply circuit.
This may be part of a consumer unit or a separate unit.
5.13 Before starting work on the electrical supply ensure power supply is
isolated.
5.14
DO NOT
allow the supply cord to contact hot surfaces, including the
motor shell, pump body or pipework. The cord should be safely routed
and secured by cable clips.
5.15
Adjacent pipes:
Adjacent suction and delivery pipes should be fitted with
earthing clamps in accordance with current regulations (Fig. 9).
5.16
Earthing:
This appliance must be earthed via the supply cord, which must be
correctly connected to the earth point located in the terminal box.
5.17
Pipework:
Copper or metallic pipework must have supplementary earth
bonding where the continuity has been broken by flexible hoses or plastic
components.
5.18
Additional earthing:
Certain installations may require additional earthing
arrangements such as equipotential bonding. Reference should be made to the
relevant regulations concerning this subject to ensure compliance.
5.19
Connections:
The pump must be permanently connected to the fixed wiring of
the mains supply using the factory fitted supply cord, via a double pole
switched (with a minimum of 3 mm contact separation) fused spur off
the ring main and
NOT
connected to the boiler or the immersion heater circuits.
5.20 The electrical connection
must be
made adjacent to (not behind) the iBoost to
allow disconnection of the electrical supply should the pump module need to be
removed for service or maintenance.
Diagram of
earth continuity
connections
Fig. 9