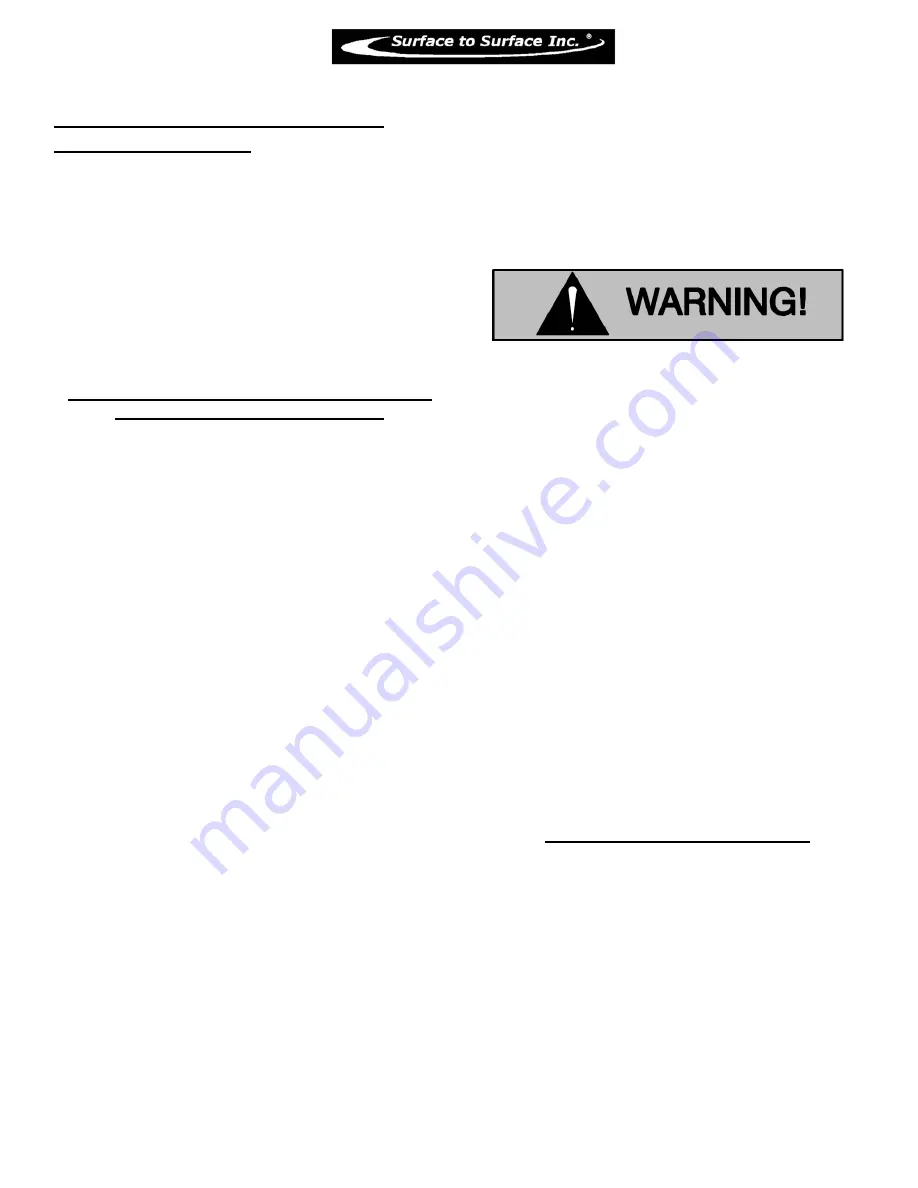
58
GR-82E2
PUMP AND SEAL DISASSEMBLY
AND REASSEMBLY
Impeller Removal
Before removing the impeller, screw the cross arm
on the automatic lubricating grease cup (1) clock-
wise until it rests against the cover (see Figure 4) to
prevent the grease in the cup from escaping.
Remove the grease cup and piping (1).
Using a hardwood block of wood positioned against
the impeller vain, strike the hardwood block with a
hammer, in a counter clock-wise rotation (viewed
from the impeller end).
Loosening the impeller is the same rotation as
loosening a standard nut and bolt.
Inspect the impeller and replace it if cracked or
badly worn. Slide the impeller adjusting shims (7)
off the impeller shaft. Tie and tag the shims, or
measure and record their thickness for ease of
reassembly.
Seal Removal and Disassembly
Remove the outer rotating element, shaft sleeve,
and remaining seal parts off the shaft as a unit.
Carefully remove the stationary and rotating seal
elements, packing rings and washers, seal spring
and spacer sleeve from the seal plate.
Inspect the seal plate and replace it if cracked or
badly worn. To remove the seal plate (3) from the
engine, remove the bolts and lock washers, or nuts
and lock washers from the studs. Inspect the seal
liner (4) for wear or grooves that could cause leakage
or damage to the seal packing rings. The seal liner is
a press fit into the seal plate and does not normally
require replacement.
If the seal liner requires replacement, remove
the seal plate assembly as described above, and
position it on the bed of an arbor (or hydraulic) press.
Use a new sleeve to force the old one out. After the
new liner is properly installed, a 1/4-inch (6,4 mm)
diameter hole must be drilled through it to permit the
flow of lubricant to the seal assembly. Be careful to
center the drill in the threaded grease piping hole and
not damage the threads. Debur the hole from the
inside of the seal liner after drilling.
Seal Reassembly and Installation
(Figures 1 and 3)
Clean the seal cavity and shaft with a cloth soaked
in fresh cleaning solvent.
Most cleaning solvents are toxic and
flammable. Use them only in a well ventilated
area free from excessive heat, sparks, and flame.
Read and follow all precautions printed on
solvent containers.
The seal is not normally reused because wear
patterns on the finished faces cannot be realigned
during reassembly. This could result in premature
failure. If necessary to reuse an old seal in an
emergency, carefully wash all metallic parts in fresh
cleaning solvent and allow to dry thoroughly.
Handle the seal parts with extreme care to prevent
damage. Be careful not to contaminate precision
finished faces; even fingerprints on the faces can
shorten seal life. If necessary, clean the faces with a
non-oil based solvent and a clean, lint-free tissue.
Wipe lightly in a concentric pattern to avoid
scratching the faces.
Inspect the seal components for wear, scoring,
grooves, and other damage that might cause
leakage.
Clean and polish the shaft sleeve, or replace it
if there are nicks or cuts on either end. If any
components are worn, replace the complete seal.
Never mix old and new seal parts.
If a replacement seal is being used, remove it from
the container and inspect the precision finished
faces to ensure that they are free of any foreign
matter.
To ease installation of the seal, lubricate the seal
liner (4) with water or a very small amount of oil,
and apply a drop of light lubricating oil on the finished
faces. Assemble the seal as follows, (see Figure 3).
Slide the seal plate assembly over the impeller
shaft and secure the seal plate to the engine using
the bolts and lock washers or nuts and lock washers
on studs.
Slide the inboard rotating element into the lubricated
seal liner with the chamfered side toward the shaft
shoulder.
Summary of Contents for M2-D2
Page 2: ...2 This page left blank intentionally...
Page 12: ...12...
Page 17: ...17 M2 D Identifying Your Machine Components Location of Tags and PIN Plates...
Page 18: ...18 SECTION II Description Care and Maintenance...
Page 30: ...30 SECTION III Set up and Installation of Unit in Detail...
Page 32: ...32 SECTION IV Operating the M2 Unit...
Page 41: ...41 SECTION V Troubleshooting the M2 Unit...
Page 44: ...44 SECTION VI Periodic Maintenance Repair Information...
Page 49: ...49 SECTION VII OEM Repair Information...
Page 63: ...63...
Page 64: ...64...
Page 65: ...65...
Page 66: ...66 SECTION VIII Parts Manual...