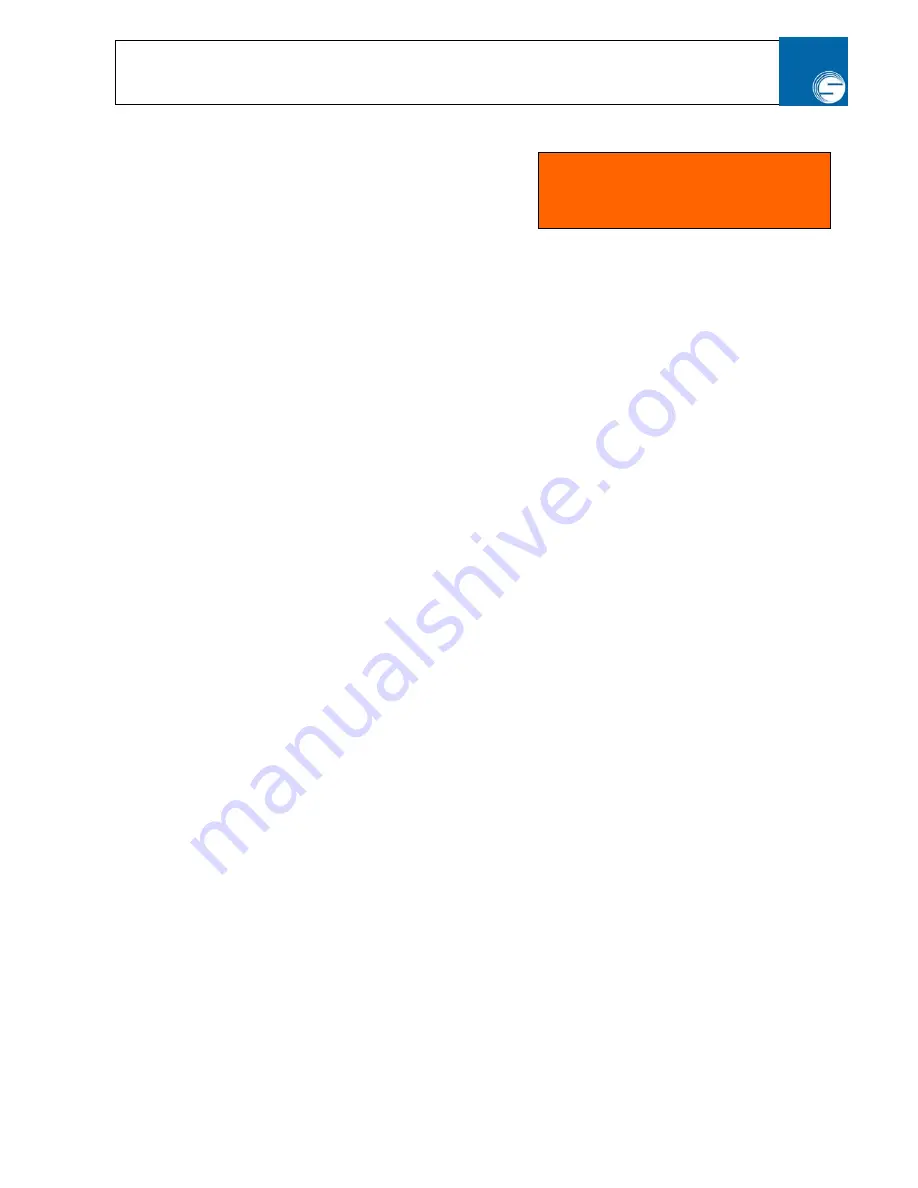
Standard user guide
V51-00-V19 eng
-11-
Rights to changes reserved
2.7 Notes to parameters
The non flashing parameters will normally have the same
functions in the special programs. The flashing parameters
are different from program to program.
Set up the max / min frequency, acceleration and
deceleration first. Then set up the special parameters. The generally parameters are described below.
Par. 1: Max frequency
Set up the maximum output frequency in this parameter.
NOTE (Special function for standard program 0):
When the set up min frequency is higher than the
set up max frequency does the output frequency decrease when the reference signal rises. (Inversely
proportional).
Important!
Please note that the motor torque decreases when frequency exceeds the frequency / voltage top point (at
normally 50Hz) If you are using the inverter for ventilation or pumps does the torque rise a lot, at rising
frequency.
Par. 2: Min frequency
In this parameter you set up the minimum output frequency. Set this value to the point were the motor
loses it’s torque or if slow speeds damages the machinery.
Par. 3/4: Acceleration / deceleration
Do not set Acceleration /deceleration higher than necessary. This will spare the mechanical parts and
avoid damages. The setting is in Hz pr. second.
Exampel:
Value = 5.0 (default) this corresponds to that it would take 10 sec for the motor to reach 50 Hz
when starting.
Acceleration:
Acceleration must not be set too high, this might cause that the current limit of the inverter
is exceeded. At 1,5 times over current does the display flash. At 2 times it TRIPS with the error OC3. In
both cases you need to lower the value of the acceleration. If you need very fast acceleration or need to
move a very big load, use a inverter with a larger power size.
Deceleration:
At fast deceleration it might occurs that the motor will function as a generator. The energy
generated will be stored in the DC link capacitors. If the energy get too high the inverter TRIPS at a OU
error. This could be prevented by using longer deceleration ramps or by using a brake chopper inverter
(option)
Par. 5: V/F-Curve (Voltage/Frequency relation)
(Can only be changed when the controller is in OFF mode – Program 0
→
Terminal 8 Not activated)
Default 50 Hz (normal mode): Voltage and frequency rises equally until 50 Hz, the voltage is constant at
above 50 Hz. This can be adjusted for special motors.
When using inverters type SC3-…and motors with 230 / 400V – 50Hz is it possible to rise the motor
power with factor 1,73 by setting the V/F curve to 87 Hz and connects the motor in delta
∆
3 x 230V. The
inverter power is in this ways 1,73 times bigger. See section 1.5.
Note (Special function for program 0):
If the value is set lower than 25 Hz the inverter goes into FAN
mode. This is used for ventilation or pumps with square falling torque at falling rotations. (The display
shows PAR) The motor would work more soundless and use less energy in FAN mode.
Note:
Most of the parameters in the
Speed Commander can be set up at run
time. This must be done with care