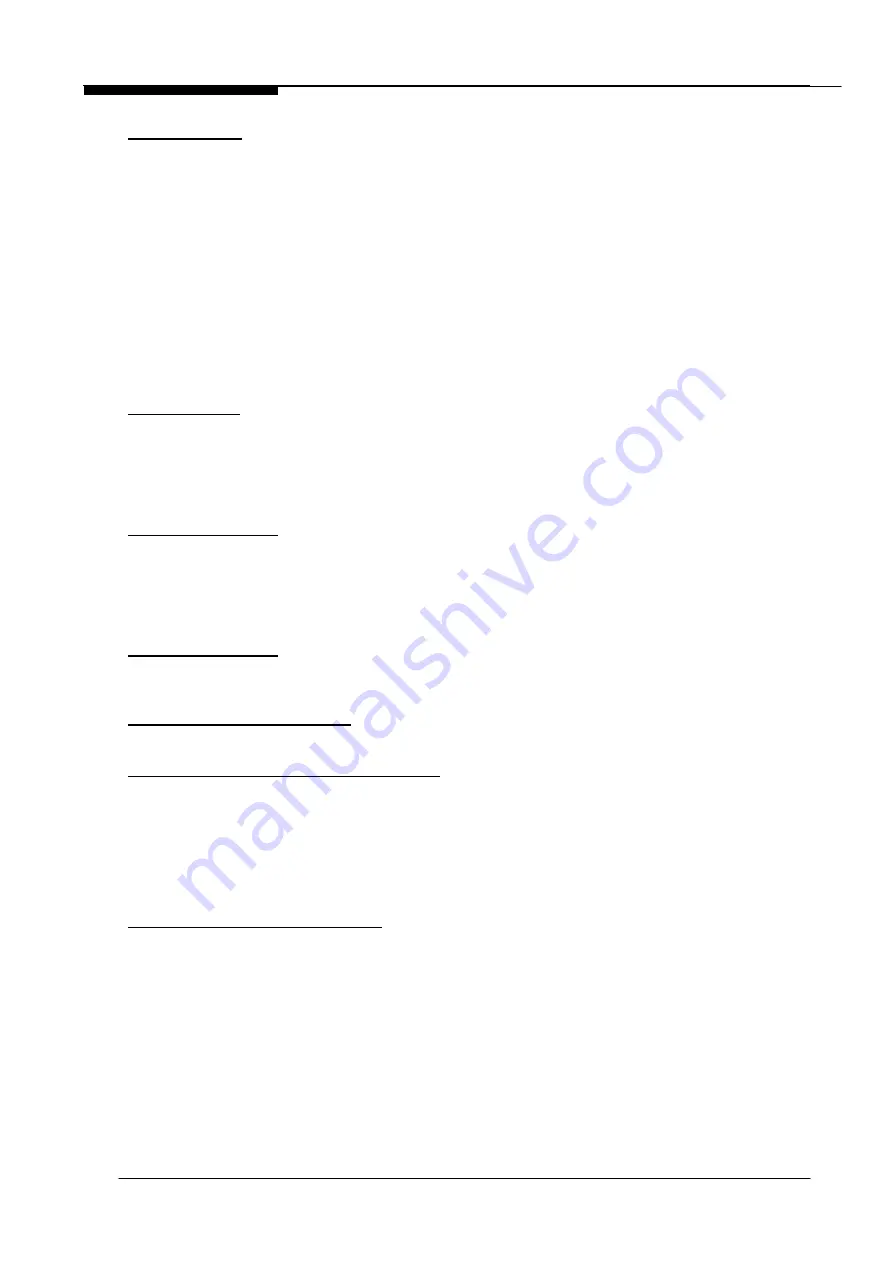
Mk6 Theme Plus (Concentric valve) Issue 1.2 21/05/02
Page 4 of 14
Installation
Site preparation
The appliance must be installed on a level, non-combustible base of dimensions 180mm deep x
400mm wide x 50mm high (Note that the base must be the same height as the hearth). A
separate non-combustible hearth in accordance with BS5871, Part 2 must be provided with
minimum dimensions as shown in Figs.3 and 4. See also approved document J 1/2/3 "Heat
Producing Appliances" issued by the Department of the Environment.
If a suspended timber floor is being used, check that the joists are capable of supporting any
structure that may be used.
If a combustible skirting board is fitted, cut away to give a 75mm minimum clearance either side
of the convector box or minimum width of hearth where applicable.
The distance from the surface of any part of the appliance to any combustible material must be
a minimum of 75mm with an air gap, or 25mm with insulation.
Clear the working area of all debris before removing the appliance from the packaging.
Note:
During building work the cavity in any wall must not be bridged other than by the ducts
provided. Ensure that there is no structural damage or damage to the damp course.
Gas connection
Gas connection shall be with rigid or semi-rigid pipe, by concealed connection only. A 15mm
gas supply pipe with isolation cock
should be brought to within 1M of the fireplace opening. The
8mm pipe, should be brought through the left hand or rear pre-punched hole in the convection
box to the burner. (Left hand only with a slim profile installation).
When passing the pipe through brickwork or plaster, cap the end to prevent entry of debris.
Electrical connection
A 230V 50Hz supply via. a switched fused spur with at least 3mm contact separation between
all poles, and fitted with a 3A fuse is required.
Three pre-wired cables pass through the wall from the fan unit to the burner, supply, and switch
plate. The switch plate may be placed at any convenient position within 2 metres of the
appliance. (This cable may be supplied as an optional extra up to 15 metres long).
Position of appliance
Determine that the location of the appliance and fan flue outlet position is suitable. Check that
the material of the surround or structure is suitable.
Installation of wall components
This section describes the cutting of apertures in the wall, and the fitting of the cable conduit.
Installation in front of an inner wall (Figs. 3 & 2)
1. Mark out on the inside wall the centreline of the duct and the 20mm dia. holes.
2. Drill right through the inner and outer walls on the centre line of the duct using a pilot
drill, taking care to keep the drill square to the wall. This pilot hole will be used later to
align a template on the outer wall.
3. Open out the hole in the inner wall to 125mm dia.
4. Drill the inner wall 20mm dia. for the plastic conduit.
Slim profile "cavity" installation (Fig. 4)
The fire can be inserted into the inner leaf of a non-combustible wall. During building work the
cavity must not be bridged other than by the ducts provided. Ensure that there is no structural
damage or damage to the damp course. Any combustible material in the cavity must be
removed or cut back to give a minimum clearance of 75mm from the top and sides of the wall
box.
1. Mark out the vertical centre line of the fire on the wall, and the 410mm x 560mm
opening for the wall box. (Use the box as a template if required).
2. Remove the inner wall to this size, and insert a suitable lintel if required.
3. Mark out and drill a 20mm dia. hole in the inner wall and insert a 100mm length of
plastic conduit. Make good any internal masonry.
4. Mark the centre line of the flue duct on the inside of the outer wall 500mm from the
base and drill a pilot hole through the outer wall.