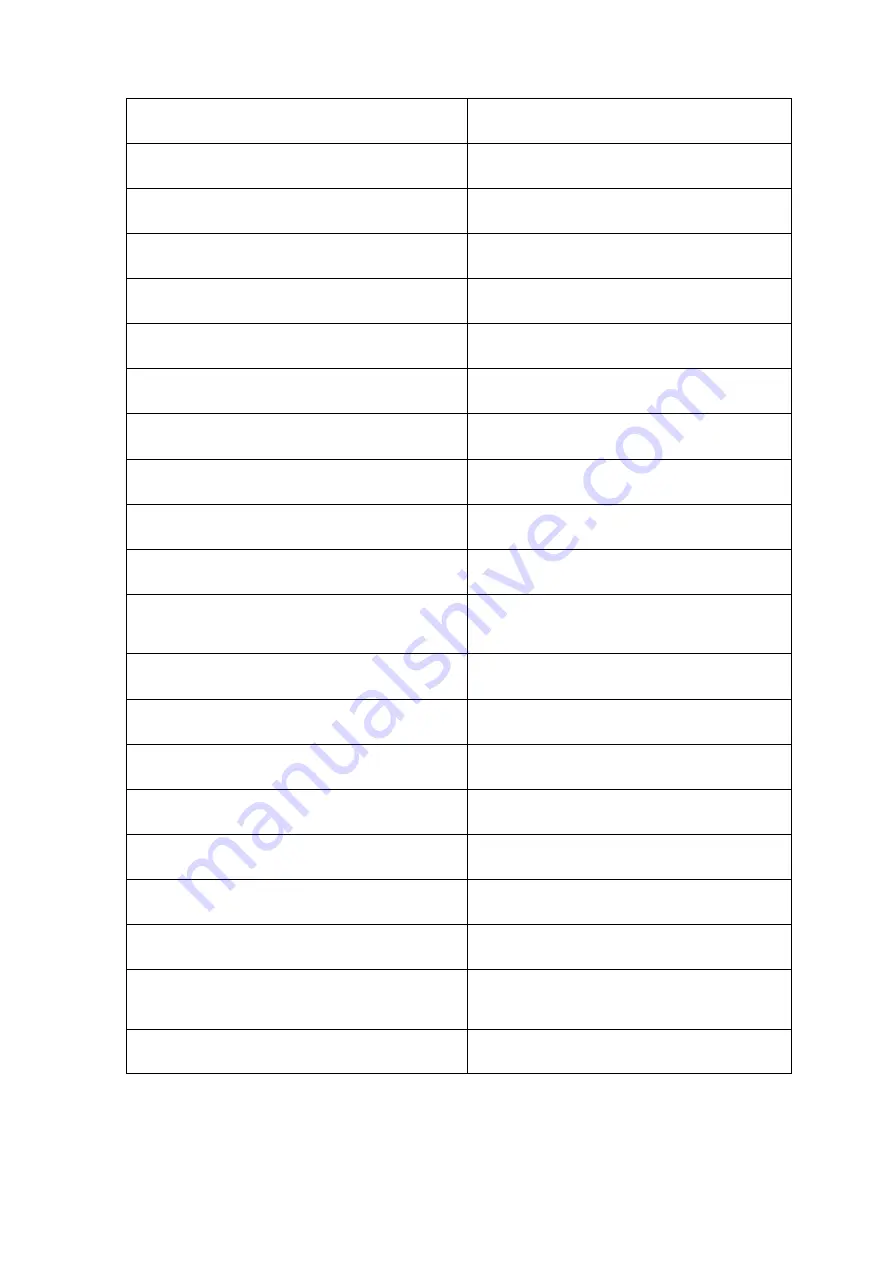
4
2
-
Technical Date of the equipment
Model
SAE
-
F10S
Lifting capacity
4500KG/1000lbs
Lifting height
2000mm/78 3/4″
Min height
110mm/4 5/16″
Width between columns
2880mm/113 3/8″
Drive through
2572.6mm/101 1/4″
Lifting time
About 40 Sec.
Lowering time
About 30 Sec.
Column thickness
5.5mm / 1/4″
Carriage thickness
5.5mm / 1/4″
The thickness of the square pipe for arm
6mm / 1/4″
arm range
680
-
1230mm/880
-
1440mm
Diameter of steel wire rope
Φ9
mm / 3/8″
Voltage
220V
Power
2.2kW
Frequency
60Hz
Circuit Breaker
1ph
Hydraulic oil
30A
Equipment Weight
AW46/AW32
Packing Dimensions
2880×740×810mm
Equipment Weight
610KG/1343lbs
Summary of Contents for SAE-F10S
Page 24: ...24...